How does an IA deal with a situation like this?
The maintenance officer of a small flying club asked if my company would be willing to manage the maintenance of the club’s 1976 Cessna 172M. The airplane had been flying about 200 hours a year, and had faced a number of maintenance challenges. After trying a number of different maintenance shops, the maintenance officer decided he could use some professional help. My firm usually doesn’t take on flying club aircraft for a number of reasons. But the club’s maintenance officer was persuasive and convinced me to make an exception for this particular Skyhawk.
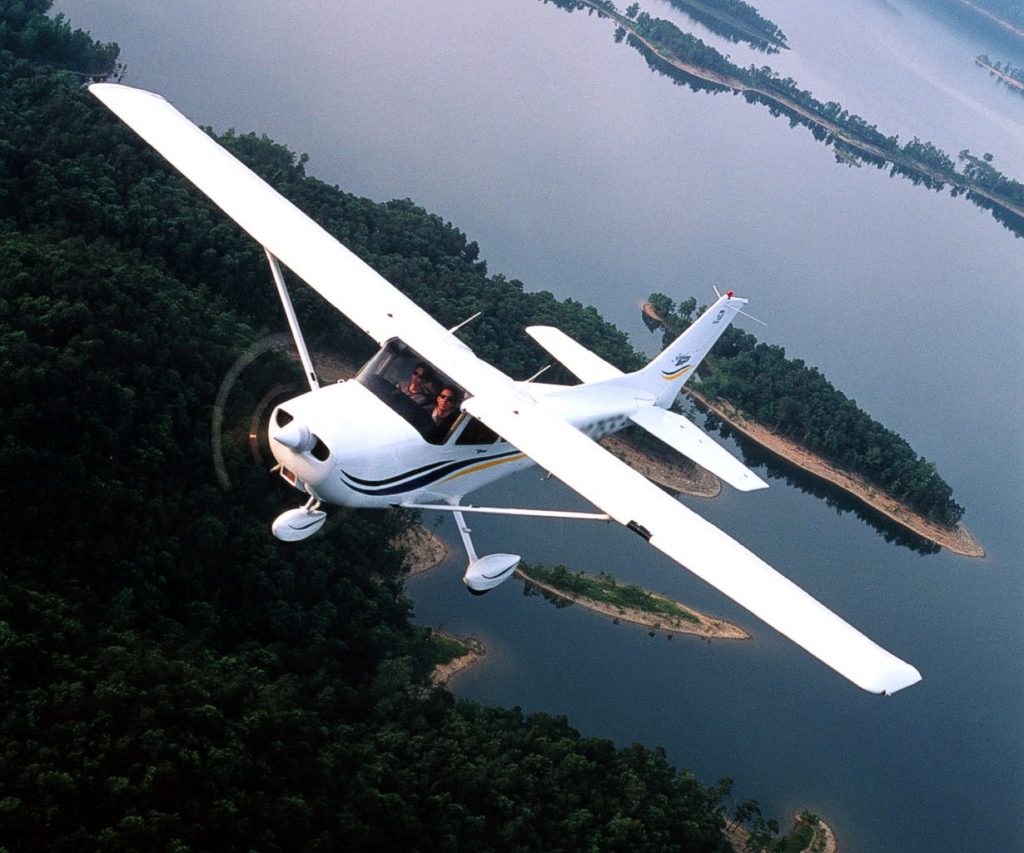
We enrolled the airplane in our managed maintenance program, and assigned one of our most senior IAs—the Director of Maintenance of a Cessna Authorized Service Center—to serve as its “account manager.” The account manager contacted the club’s maintenance officer and started gathering information about the airplane and its maintenance history, while I turned my attention to other matters, knowing that the Skyhawk’s maintenance was now in capable hands.
Within hours, the account manager pinged me and suggested that I might want to take a closer look at the club’s “highly modified 172.” That got my attention. I reviewed the online ticket that we’d opened for the club’s Skylane. The more I read, the more I squirmed.
Chronicle of a powerplant
When Cessna delivered this Skyhawk in 1976, it came equipped with a Lycoming O-320-E2D engine rated at 150 horsepower, and a McCauley 1C160/CTM 7553 fixed-pitch prop with a 75” diameter and a 53” pitch.
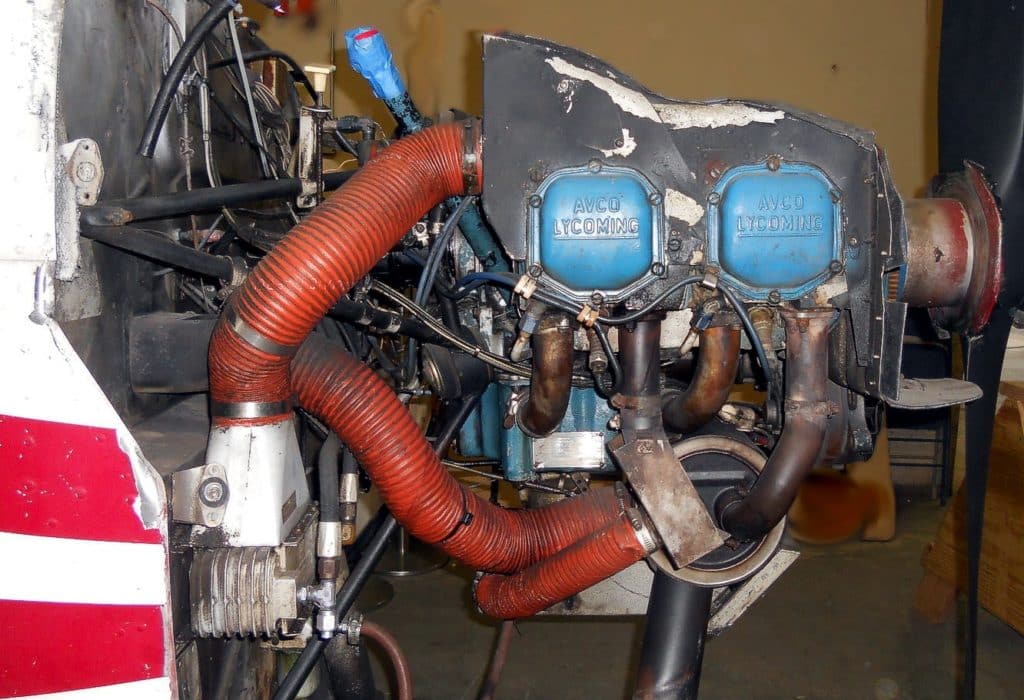
(The prop pitch is the theoretical distance that the prop would travel forward in one revolution if there were no slippage. The larger the pitch, the greater the blade angle and the lower the static RPM at a given horsepower.)
In 1986, the club installed the Pearce high-compression STC (SE1226CE) and the Pearce prop twist STC (SA1225CE). These alterations increased rated takeoff power from 150 hp to 160 hp (limited to 5 minutes), compression ratio from 7.0 to 8.5, prop pitch from 53” to 57”, maximum static RPM from 2370 to 2400, and minimum avgas grade from 80 to 100. (Both of the Pearce STCs are now owned by Ly-Con Rebuilding Company.)
In 2000, the club further modified the Skyhawk by installing a Power Flow tuned exhaust system (STC SA01801AT). This is considered by the FAA to be an airframe alteration rather than an engine alteration (which is why the STC number starts with “SA” rather than “SE”), but the purpose of the tuned exhaust system is to increase engine horsepower and fuel efficiency. Power Flow does not make any specific horsepower increase claims, but they do claim that most fixed-pitch Cessna 172 customers report an increased rate-of-climb of 150 to 225 feet-per-minute. Assuming an aircraft weight of 2,300 pounds and a prop efficiency of 80%, that would calculate out to a climb power increase of 13 to 20 horsepower. This suggests that the Skyhawk’s modified O-320 might be putting out 173 to 180 horsepower on takeoff.
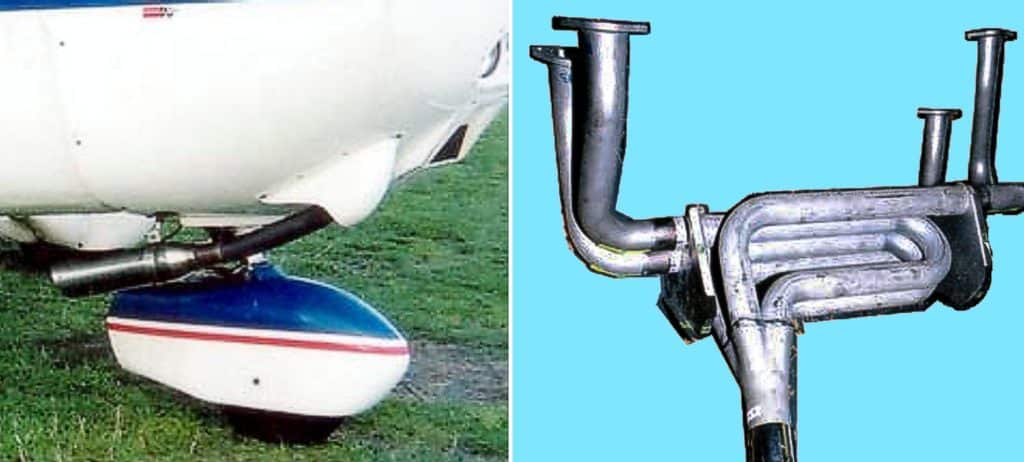
Indeed, the club found that the 57” pitch prop was “overpowered” by the modified engine. Club members reported a number of episodes of engine overspeed. In 2008, the club had a prop shop increase the pitch even further, which helped with the overspeed issue according to the club’s maintenance officer. Indeed, the Power Flow Systems website FAQ page states:
You can utilize the extra RPM our exhaust provides to increase airspeed, but you would have to allow the RPM to increase. To boost your ultimate top speed, your only possible alternative is to consider “re-pitching” your propeller. Some of our customers have reported that experienced prop shops have re-pitched their propeller to obtain a better cruise performance by sacrificing some of the improved climb performance from installing a Power Flow Systems Tuned Exhaust.
Meanwhile, in 2006 the club performed a top overhaul on the engine when three of the four cylinder heads exhibited excessive heat signatures. They installed a digital engine monitor, which showed excessive CHTs during climbs, especially at higher altitudes. The club imposed amended climb procedures to keep CHTs better controlled. But when the engine underwent major overhaul, the engine shop found annealed compression rings. During post-overhaul test flights, it was determined that the cylinders were running too lean even at full-rich mixture. As a result, the engine shop had the carburetor re-jetted to increase full-power fuel flow from 12.5 gph to 13.5 gph. And the club revised its operating procedures to make them more conservative and less abusive.
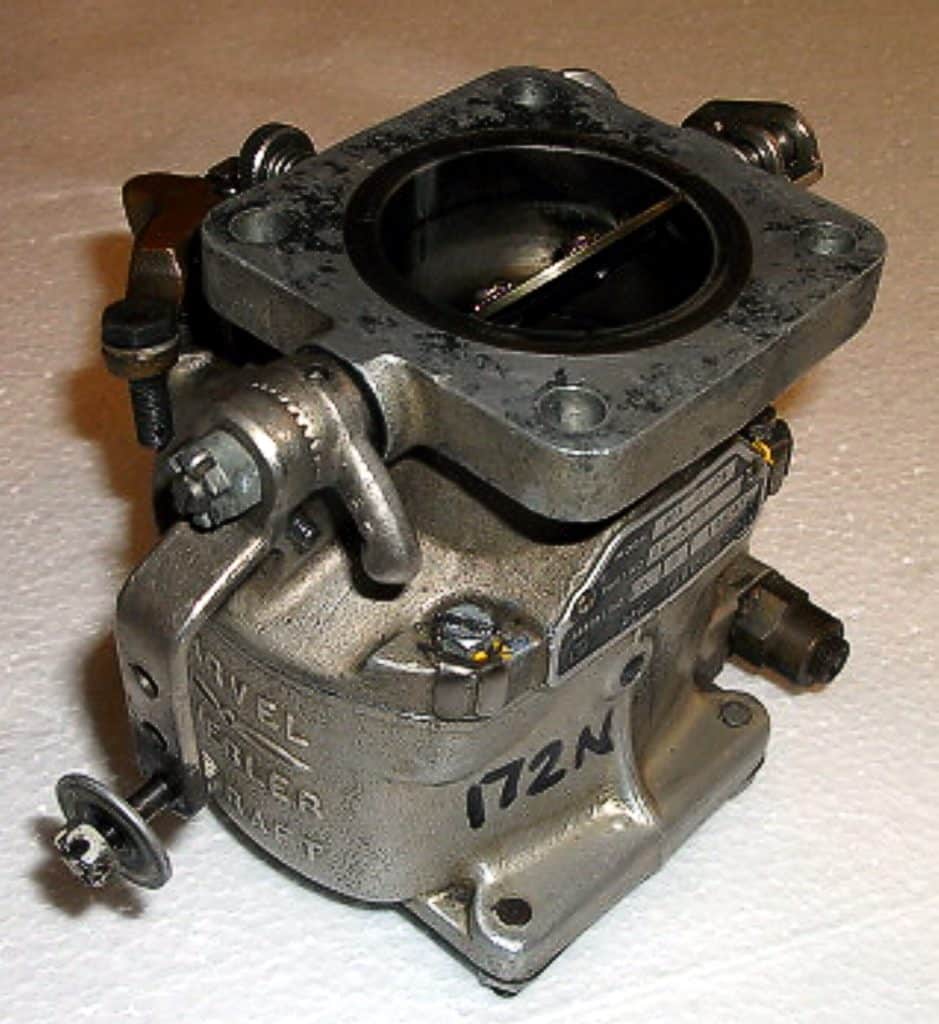
Finally, in 2013—just before the club enrolled the Skyhawk in our managed maintenance program—the right magneto was removed and replaced with an Electroair electronic ignition system (STC SA02987CH). This system produces a hot, long-duration spark, and incorporates a manifold pressure sensor and a controller that advances the ignition timing far beyond Lycoming’s standard 25° BTDC at reduced manifold pressures. Electroair claims that this provides increased horsepower, better high-altitude performance, and significantly improved fuel economy.
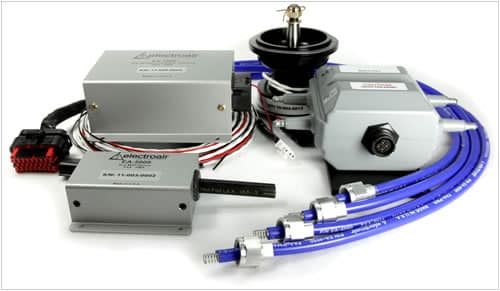
The Electroair system had just been installed at the recently completed annual inspection, and the club hadn’t had an opportunity to fully evaluate its effects at the time the aircraft was enrolled in our program.
After reviewing the history of this Skyhawk and its powerplant modifications, all I could think to say was “Yikes!” This is certainly not what I bargained for when I agreed for my company to take responsibility for managing the maintenance of this aircraft.
A question of airworthiness
My dilemma, of course, was to decide whether or not the Skyhawk was still airworthy with its highly modified powerplant. If unairworthy, I couldn’t allow it to remain in our managed maintenance program. Whether or not it was airworthy was not immediately obvious to me.
For a certified aircraft to be “airworthy” it needs to meet two criteria:
- It must comply with its original or properly altered type design; and
- It must be in condition for safe operation
The first criterion is theoretically objective: Either the aircraft complies with its type design or it doesn’t. The second criterion is subjective: It’s somebody’s opinion (usually an IA) as to whether the aircraft is safe to fly or not.
But in the case of this Skyhawk, it was not at all obvious to me whether or not the first criterion was met. The airplane obviously did not comply with its original type design which called for a 150-hp Lycoming O-320-E2D engine with two Slick magnetos, a McCauley 53”-pitch prop, a Marvel-Schebler LVC-5-4PA carburetor, and a standard Cessna exhaust system. Clearly the type design had been massively altered from the original. The question was: Had it been PROPERLY altered?
Some of the alterations were made pursuant to Supplementary Type Certificates (STCs), including the high-compression pistons, the 57”-pitch prop, the Power Flow tuned exhaust, and the Electroair electronic ignition system. Some others weren’t, including re-pitching the prop beyond 57” pitch and re-jetting the carb to flow 13.5 gph instead of 12.5 gph.
Surely the four STC’d mods were proper alterations of the type design, right? Well, I wasn’t so sure. The first two alterations that the club made in 1986—the Pearce high-compression mod and the Pearce prop-twist mod—were clearly proper alterations. But what about the tuned exhaust added in 2000; was it proper to make that alteration to the previously altered powerplant? And what about the electronic ignition system added in 2013; was it okay to add that on top of the other three alterations?
Who decides these things, anyway?
A question of compatibility
The regulations make it clear that whenever an alteration is installed on an aircraft, it is the responsibility of the installing mechanic to determine whether the alteration is or is not compatible with any other previously-installed alterations. In fact, both the Power Flow and Electroair STCs contain the following language:
Compatibility of this design change with previously approved modifications must be determined by the installer.
But how is the installing mechanic supposed to determine whether or not the multiple STC’d alterations are compatible with one another? Aye, there’s the rub! The FAA offers no guidance.
In fact, on May 24, 2012, the National Transportation Safety Board (NTSB) sent a safety recommendation to FAA Administrator Huerta highlighting the problem of determining STC compatibility. The NTSB cited two GA accidents to illustrate the problem. The first involved the the crash of a Cessna Turbo Skymaster N12NA following in-flight separation of the outboard section of the right wing and killing all five occupants. The Skymaster was modified with 22 different STCs, including a STOL kit, extended wingtip fuel tanks, and winglets. The NTSB determined that the combination of STCs installed on the wing created wing loads that had not been evaluated, and the FAA issued an AD to address the specific issue.
The second accident involved a Beech Baron 58 that crashed into a house during an instructional flight, killing the pilot and his flight instructor, and destroying the house. The Baron had two STCs installed. One STC involved installation of vortex generators (VGs) that reduced the airplane’s Vmca (one-engine minimum control speed) from 81 knots to 74 knots. The other STC included horsepower increases of 15 hp per engine plus installations of winglets, modified engine nacelle nose bowls, and different propellers, and would have increased Vmca from 81 knots to 87 knots on an airplane without VGs. Investigators determined that the Baron’s airspeed indicators was marked with a blue line (indicating Vmca) at 74 knots, and that no determination had been made as to what the actual Vmca was with both STCs installed, but clearly it would have been significantly higher than 74 knots.
The NTSB recommended that the FAA:
- Develop specific guidelines and/or a checklist to help installers determine the compatibility and interaction between a new STC and any previously installed STCs to ensure that the new STC will not adversely affect the aircraft’s structural strength, performance or flight characteristics.
- Instruct installers to document on the Form 337 how the installer determined the compatibility and interaction between the new STC and previously installed STCs.
- Educate owners and operators of all aircraft with multiple STCs about the potential hazards of incompatible STCs, and encourage them to have their aircraft evaluated for compatibility.
So…are the four STCs installed on the Skyhawk compatible? I still don’t have a good answer, but frankly I’m not at all comfortable that they are. Each of the STCs increases engine horsepower. Each of the STCs was approved by the FAA on the assumption that it was the only horsepower-increase STC being applied to the Lycoming O-320. Combining them all together struck me as being eerily similar to the Skymaster with the STOL kit, tip tanks and winglets. And the heat-distressed cylinder heads and annealed compression rings seemed like warning signs.
Non-STC’d alterations
What about the re-jetted carb and the re-pitched prop, both alterations that were made without benefit of any STC? Neither of those worried me technically, because neither increased the horsepower of the engine. However, for such alterations, the installing mechanic must determine whether they are “major” or “minor” alterations.
A mechanic is permitted to make a minor alteration on his own authority with just a simple logbook entry. But a major alteration requires approved data and the filing of an FAA Form 337. The most common form of approved data for a major alteration is an STC, but if no STC is available, then the alteration requires a Field Approval from the local FSDO.
FAR Part 43 Appendix A provides guidance to mechanics as to whether a particular alteration is major or minor. After reviewing that guidance, I became convinced that both re-jetting the carburetor and re-pitching the propeller beyond 57” pitch constituted major alterations that required Field Approvals. Just to be sure, I checked with my Principal Maintenance Inspector at the FSDO and he agreed that they sound like major alterations to him, too.
Obtaining Field Approvals for those mods would very likely require the involvement of the FAA Aircraft Certification Office (ACO) or hiring a Designated Engineering Representative (DER), which would probably make the approval process prohibitive in terms of cost and elapsed time.
Epilog
After agonizing over this situation for several days, and consulting with several veteran IAs whose judgment I respect, I reluctantly concluded that I couldn’t expose my company to the risk of managing the maintenance of this highly modified Skyhawk. I just wasn’t comfortable that it was legal, and I wasn’t comfortable that it was safe.
I phoned the club’s maintenance officer, explained the situation in detail, and told him that would be asking my Manager of Operations to refund the management fee that the club paid and to terminate the service agreement.
The maintenance officer seemed surprised and disappointed, but not upset. He asked my advice on how to proceed. I suggested that he find a local powerplant DER, buy an hour or two of his time, and see if the DER could give him a good idea of which of the modifications could be most easily established as legal and compatible, and which would be best removed. I also suggested that he contact Power Flow Systems and Electroair to see if either of them could provide a letter stating that their STCs were compatible with the O-320 powerplant modified with Pearce high-compression pistons and prop twist STCs. Finally, I suggested he speak with his local FSDO about the possibility of obtaining Field Approvals for the re-jetted carb and re-pitched prop.
Had this been an RV or a LongEZ, my only concern would have been whether the aircraft was safe. Compliance with type design wouldn’t have been an issue, since an experimental amateur-built aircraft has no type design to comply with. But it was a certificated Cessna 172M, so things got complicated.
You bought a plane to fly it, not stress over maintenance.
At Savvy Aviation, we believe you shouldn’t have to navigate the complexities of aircraft maintenance alone. And you definitely shouldn’t be surprised when your shop’s invoice arrives.
Savvy Aviation isn’t a maintenance shop – we empower you with the knowledge and expert consultation you need to be in control of your own maintenance events – so your shop takes directives (not gives them). Whatever your maintenance needs, Savvy has a perfect plan for you: