The care and feeding of aircraft batteries.
Last month, in Part 1 of this article, we discussed the construction, chemistry, types and characteristics of lead-acid aircraft batteries. This month, we’ll talk about the care and feeding of those batteries, including charging and discharging, conditioning, capacity testing, and deciding when a battery should be retired and replaced.
Charging
Charging a lead-acid battery involves three phases: (1) a constant-current phase during which charging voltage gradually increases; (2) a constant-voltage phase during which charging current gradually tapers off to very low levels as the battery approaches its fully-charged state; and (3) a float (or trickle) charge phase that maintains the battery in its fully-charged condition and offsets the battery’s natural tendency to self-discharge.
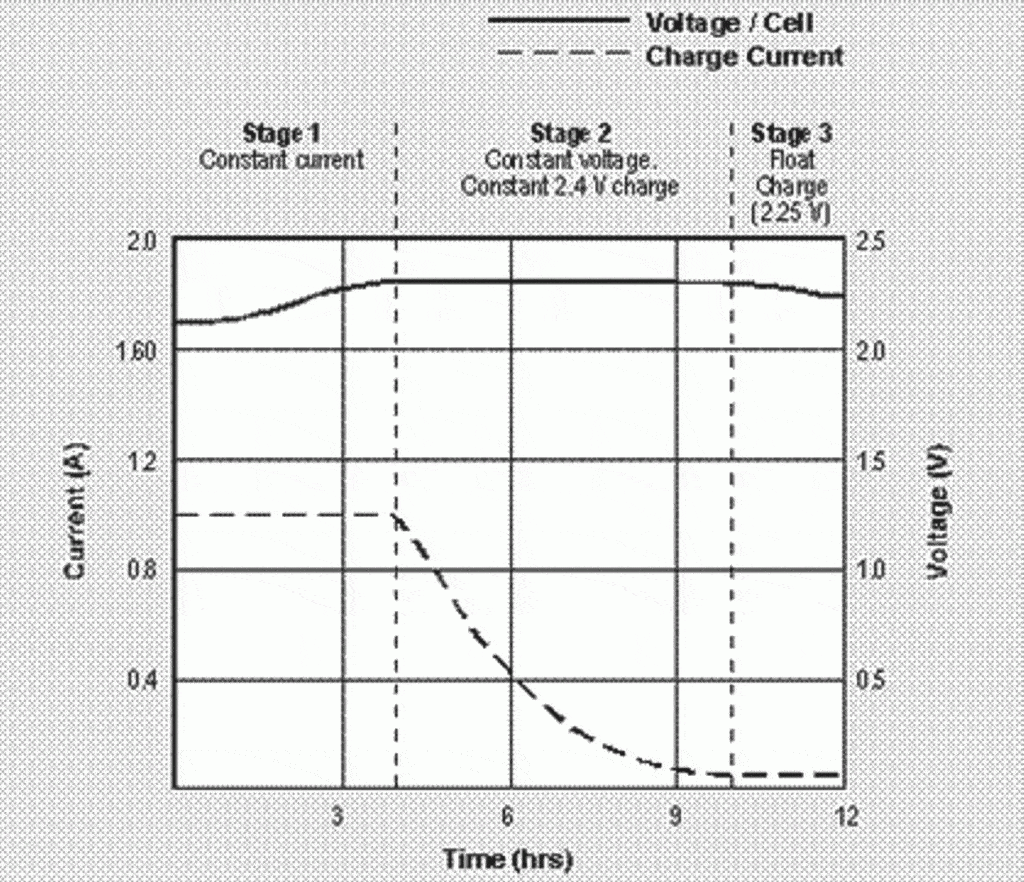
Although this is a fairly complicated procedure, we now have very reasonably priced microprocessor-controlled battery charges that can perform this automatically. Keep in mind, however, that your aircraft’s charging system is strictly a constant-voltage charger, which is why it’s a very bad idea to fly with a deeply discharged battery (e.g., after maintenance or a GPU start). The aircraft’s charging system will charge a deeply discharged battery at an excessive rate (because it is a “dumb” charger without current limiting), and is very likely to damage the battery in the process, sometimes catastrophically.
It’s also important to understand that batteries are exquisitely sensitive to charging voltage. A 12-volt battery requires about 14 volts to attain and maintain a full charge. A 24-volt battery requires about 28 volts. The exact optimal charging voltage depends on battery temperature (see Figure 6). For example, the battery in my Cessna 310 (which runs cool because it’s mounted in the wing) requires a lower bus voltage than the battery in a Cessna 210 (which runs warm because it’s mounted on the firewall inside the engine compartment).

If the aircraft’s voltage regulator is misadjusted by even a few tenths of a volt from the optimum setting, that’s a bad thing. If the bus voltage is too low, then the battery will not charge to its rated capacity, which would be unpleasant in the event of an in-flight charging system failure that forces you to operate solely on battery power. If the bus voltage is too high, the battery will overcharge, overheat, outgas, and possibly lose electrolyte and/or warp or damage its plates; the result is reduced battery lifespan, and occasionally catastrophic failure.
Self-discharge
Lead-acid batteries gradually lose their charge during periods of disuse. If the OAT is warm, the self-discharge may not be so gradual. The self-discharge rate doubles with every 18°F (10°C) increase in temperature.
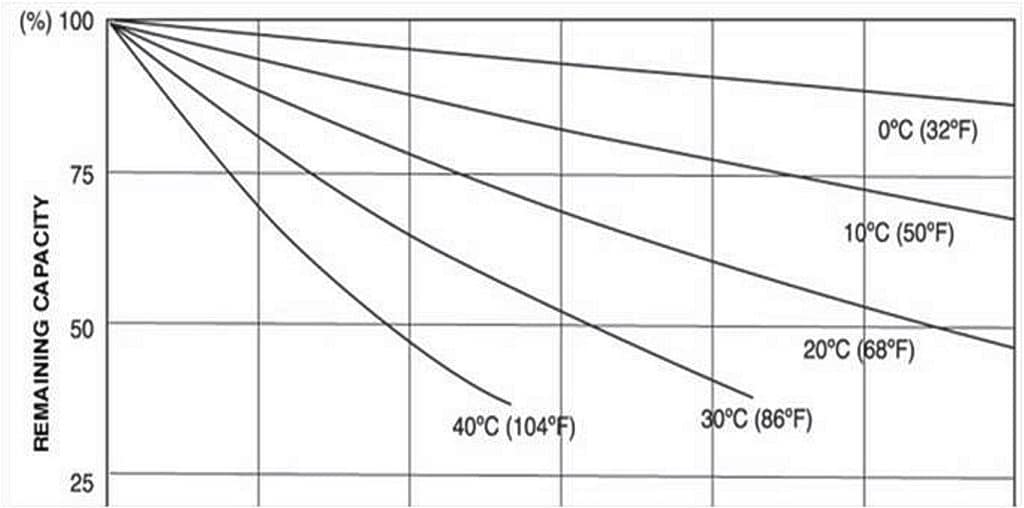
A flooded-cell battery will typically lose 25% of its charge:
- Every 30 days at 77°F
- Every 15 days at 95°F
- Every 7 days at 113°F
An AGM battery will self-discharge more slowly, roughly one-third the rate of a flooded-cell battery. This can be a big advantage for aircraft that are based in hot climates, such as the desert southwest. If you’re based in a hot climate and don’t fly every few days, it probably makes a lot of sense to keep your aircraft battery on a trickle charger between flights.
Sulfation
In last month’s article, we saw that lead sulfate (PbSO4) is deposited on the plates of a lead-acid battery as it discharges. The lead sulfate forms in a powdery “amorphous” state that easily recombines with the electrolyte when the battery is recharged. However, if the battery is allowed to remain discharged for any significant period of time, the lead sulfate will gradually transform into a crystalline state that no longer dissolves. This process is known as “sulfation” and causes battery capacity to decline over time.
Sulfation occurs when the battery is discharged and allowed to remain in that state. It also occurs quite rapidly if the electrolyte level is allowed to decline to the point that the top of the plates are exposed. Thus, the better job you do of keeping the battery fully charged at all times and the electrolyte at the proper level (for flooded-cell batteries), the longer the battery will last. Let it discharge or let the top of the plates get exposed and the lifespan of the battery will be severely compromised.
A process known as “pulse conditioning” may help prevent or reverse sulfation. The process involves charging the battery with voltage pulses intended to break up the crystalline lead sulfate. The effectiveness of pulse conditioning is somewhat controversial. The companies that make pulse-conditioning chargers claim it’s the greatest thing since sliced bread, while the battery manufacturers tend to remain skeptical. I cannot vouch personally for the effectiveness of pulse conditioning, although I’m pretty sure it couldn’t hurt.
Capacity testing
Both Teledyne-Gill and Concorde have issued Instructions for Continued Airworthiness (ICA) calling for regular capacity testing of their batteries. A capacity test consists of fully charging the battery, then applying a specific load and measuring how long it takes for the battery to discharge. Gill calls for doing an initial capacity test after one year and then every six months thereafter. Concorde calls for doing an initial test after two years and then every year thereafter. In the real world, these capacity tests are sometimes done at annual inspection (and sometimes not), but it’s almost unheard of for them to be done more often. Gill calls for the battery to be replaced when its capacity declines to less than 80% of specifications; Concorde’s replacement threshold is 85%.
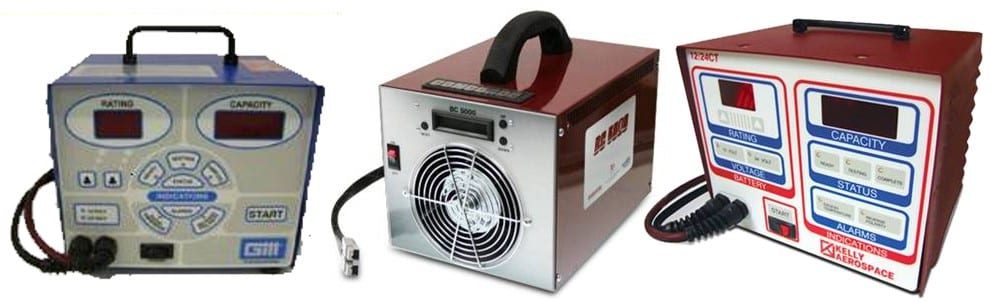
The best way to perform a capacity test is by using an aircraft capacity tester (see Figure 8). Unfortunately, they aren’t particularly cheap—$900 to $1,300 depending on model. Consequently, many maintenance shops don’t own one and so many aircraft batteries never get capacity checked.
It is possible to do a rough “do-it-yourself” capacity check without using a capacity tester. This is done by charging the battery fully, then turning on enough electrical equipment to drain the battery at a rate in amps equal to the battery’s rated one-hour discharge rate in ampere-hours. (E.g., a discharge rate of 12 amps for a battery rated at 12 ampere-hours.) Measure how much time it takes to fully discharge the battery to 10 or 20 volts (for a 12 or 24 volt battery, respectively). A new battery should take 60 minutes to discharge. An older battery will take less. If the battery fully discharges in 48 minutes, then the battery capacity has declined to 80% and it’s time to replace it.
Be sure to charge the battery immediately following any capacity check. Leaving them discharged is a sure way to hasten their demise.
Battery chargers
Nowadays there are some very sophisticated yet inexpensive battery chargers available for aircraft use. In my opinion, every aircraft owner should own one.
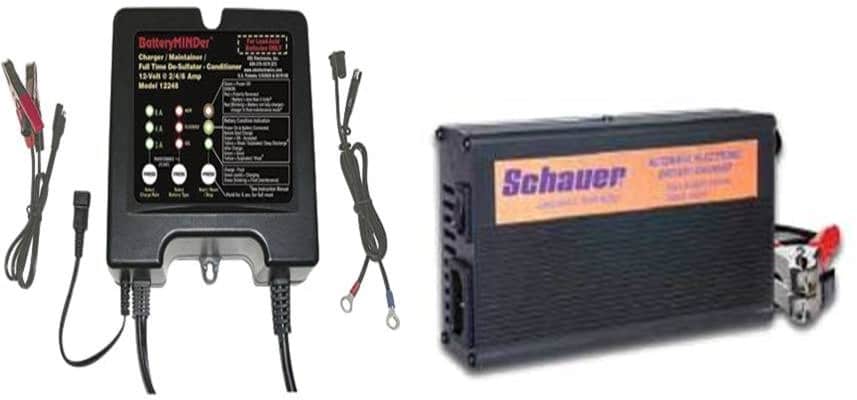
One of the very best is the BatteryMINDer from VDC Electronics. Model 12248-AA-S1 is an 8-amp charger for 12-volt aircraft batteries, and model 24041-AA-S2 is a 4-amp charger for 24-volt aircraft batteries. Both models provide automatic three-phase charging and pulse conditioning. They are fully automatic—set it and forget it—and will not harm the battery even if left on 24/7. (To the contrary, leaving the charger on 24/7 is the best thing you can do for maximum battery longevity during periods of disuse.) Both models are priced under $200.
If $200 is above your budget, Schauer makes two automatic chargers designed for aircraft batteries. The model JAC1212 is a 12-amp 12-volt charger, and the JAC0524 is a 5-amp 24-volt charger. Both offer fully automatic three-phase charging, but neither does pulse conditioning. Both are bargain-priced under $80.