Troubleshooting is best accomplished by first gathering data and then analyzing it logically.
The owner of a 2005 Cessna T182 was in Key West Florida when he experienced unusual roughness immediately after engine start. The EGT and CHT on the #3 cylinder seemed unusually low at first, but the roughness seemed to clear up before he took off on a local sightseeing flight.
The next morning as the owner attempted to depart Key West for home, the roughness reappeared but this time didn’t go away as the engine warmed up. Leaning seemed to help some, but he did not resolve the problem completely. Once again, cylinder #3 was cold.
Why is the cylinder cold?
The owner took the aircraft to a local mechanic, who ran the engine and concluded that the RSA fuel servo was at fault. He discussed the problem with another technician who agreed with his diagnosis. The mechanic proposed to remove the RSA fuel servo and overnight it out to Precision Airmotive for bench testing and repair. This would leave the aircraft grounded and the owner stranded in Key West for a week. The estimated cost for an overhauled fuel servo was about $2,000.
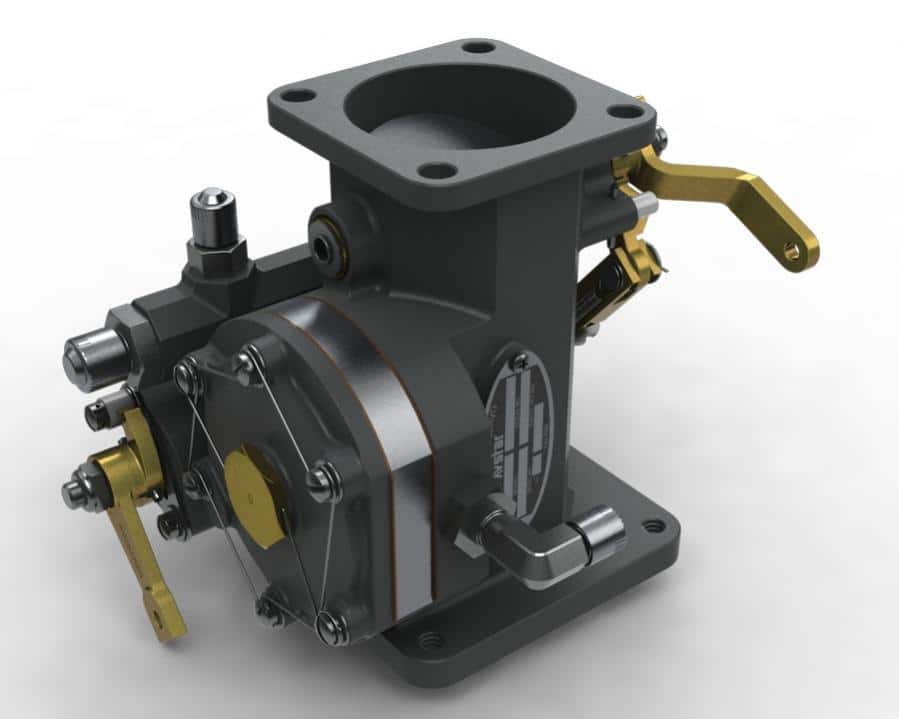
As luck would have it, the Cessna owner was a client of my company, so he phoned his account manager Paul New. Paul is hardly your typical GA mechanic. He is a superb diagnostician and was honored by the FAA in 2007 as National Aviation Maintenance Technician of the Year, an honor I was privileged to receive the following year.
Paul had the owner describe the symptoms in detail, and quickly concluded that this was almost certainly a classic case of Lycoming “morning sickness” caused by a sticky exhaust valve. Paul explained to the owner that the symptoms could not possibly be caused by a faulty RSA fuel servo, since there is no way that a fuel servo problem could affect just one cylinder.
Fortuitously, the G1000 system in the T182 had recently been upgraded to provide data logging, so Paul had the owner insert an SD memory card into the G1000 and do another ground run so that the data could be captured and uploaded to our SavvyAnalysis.com platform. When Paul reviewed the engine data, it was clear that the data was not consistent with a clogged injector or any other fuel system problem. Cylinder #3 was producing meaningful EGT (so it was getting fuel and spark), but was not producing meaningful CHT (so it wasn’t producing power). Those findings were consistent with an exhaust valve that was not fully closing.
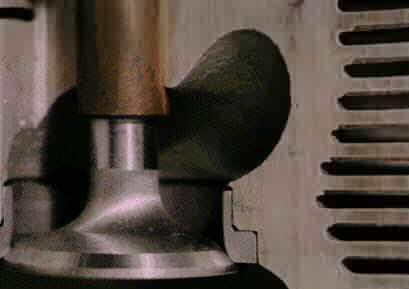
At Paul’s suggestion, the local mechanic removed the spark plugs from cylinder #3 and predictably found them to be oil fouled. After cleaning the plugs, the engine ran a bit better. The engine smoothed out after several more ground runs, reinforcing Paul’s diagnosis of a sticky #3 exhaust valve (which would be worst when cold and would free up as it heated up). At this point, the owner decided to fly his T182 home—which he did without incident—and have his regular mechanic ream the #3 exhaust valve guide. This appears to have resolved the issue once and for all.
Why is the cylinder hot?
Half a world away, a client in Tzfat, Israel, was in a panic. He and his partner had just spent nearly $50,000 to replace the IO-550-N engine in their 2003 Cirrus SR22 with a Continental factory rebuilt engine.
On the first few flights after the engine change, the CHTs were quite a bit higher than what the owners were accustomed to seeing—especially cylinders #2 and #6—but they understood that higher-than-normal CHTs are normal during the initial break-in period. (Continental recommends that CHTs be kept at or below 420ºF during break-in, and we like to see them at or below 400ºF in an aircraft like the Cirrus SR22 with its exceptionally efficient cooling system.)
At 4 hours SMOH, most of the CHTs (including #2) seemed to be coming down, but #6 seemed to be getting worse. Then on a takeoff from a small airport 100 miles away from home base, CHT #6 rose smoothly to 470ºF, while the other five CHTs remained in the 360ºF to 380ºF range. The pilot immediately reduced power and returned to the airport. By the time the airplane touched down, CHT #6 had come back down to about the same as the other cylinders.
The pilot attempted another takeoff, but CHT #6 started to run away again, so he aborted the takeoff and stopped on the remaining runway. According to the pilot, the #6 EGT remained normal throughout, and similar to the EGTs for the other five cylinders.
Based on the pilot’s verbal report, we suspected that the high CHT #6 was some sort of indication problem, because a “real” cylinder problem would have been confirmed by an anomalous EGT. But experience has made me skeptical of such eyewitness accounts, so I told the owner I’d feel a lot more comfortable giving him advice if I could see the actual engine data. The owner arranged to dump the data from his Avidyne MFD and upload it, where I and two of my associates reviewed it.
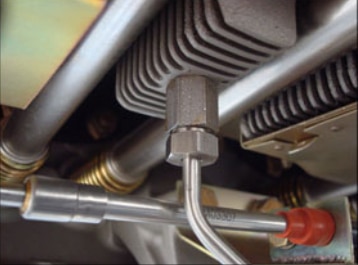
Our review of the data immediately confirmed our suspicions that the #6 CHT indication was bogus. At one point, its value changed more than 40ºF between two adjacent data samples spaced 6 seconds apart. A 40ºF change in CHT in 6 seconds is simply not possible…it defies the laws of physics. I’ve studied literally thousands of flights, and the most rapid CHT change I’ve ever seen—during a destructive pre-ignition event that wound up melting the piston—was about 1.5ºF per second. This one changed 7ºF per second, and that’s simply not plausible. Clearly, the CHT #6 indication was lying, due either to a faulty probe or a bad connection.
We asked whether it was possible to have the #6 and #4 CHT probes swapped to verify that the anomalous CHT indication remained with the bad probe. Unfortunately, there were no services at this airport, and no mechanic available to swap the probes. After reviewing the engine monitor data, we were sufficiently confident in our diagnosis that we recommended that the owner fly the airplane home and have the CHT indication problem debugged there. The flight was uneventful, and the new engine is breaking in just fine.
High CHT after annual
Another client flew his airplane to a top-notch California service center for its annual inspection. The shop repaired a number of discrepancies, and sent out both magnetos for a scheduled 500-hour IRAN (inspect and repair as necessary). Two weeks later, the owner came back to pick up his aircraft. He paid the shop’s invoice, fired up, taxied out, performed a normal engine runup, and took off.
About 90 seconds after takeoff, the airplane’s JPI EDM-700 engine monitor alarmed, and the pilot saw that CHT #2 had reached 395ºF and was still rising. He immediately reduced power and told the tower that he was returning to land. He taxied back to the shop and described the problem to the Director of Maintenance (DOM).
Because both magnetos had been removed and reinstalled, the DOM’s first thought was that the magneto timing was adjusted incorrectly and was too far advanced. He had his lead IA re-check the mag timing (while he watched), and it was spot-on (within 0.2º of spec). The IA checked the #2 fuel nozzle and found it clean and unobstructed. He also checked the spark plugs and they were fine.
More than an hour later, the owner attempted a second takeoff and this time the CHTs were even worse. CHT for cylinders #1, #2 and #3 reached 400ºF, 408ºF and 411ºF, respectively, before the pilot reduced power and came back to land. At this point, he dumped his JPI data, uploaded it, and phoned me. I pulled up the data on my computer while he was still on the phone.
I compared the engine data for the last pre-annual flight to the data for the two aborted post-annual flights. What I found was that at full takeoff power from approximately sea level, both post-annual flights had CHTs about 50ºF higher and EGTs about 50ºF lower than the pre-annual benchmark flight. I explained to the owner that this could mean only one thing: advanced magneto timing. I understood that the shop had just checked the mag timing and found it spot-on, but I also knew that the engine data wasn’t lying, so I urged the owner to have the shop check the mag timing again. I said that the high-CHT/low-EGT condition I was seeing in the data would require that at least one magneto had timing advanced by 3º to 5º.
Two hours later, I spoke with the DOM and the shop. He explained that he re-checked the mag timing, but this time instead of using the shop’s fancy $360 digital inclinometer, he used the old mechanical “flower pot” timing tool that he’d used for more than 30 years before buying the digital unit. The flower pot revealed that the timing of both mags was advanced 3º beyond the proper timing specification. The shop’s $300 digital inclinometer was off by 3º. (I later learned that one of the technicians had accidentally dropped it on the concrete hangar floor, and it was never quite the same after that.)
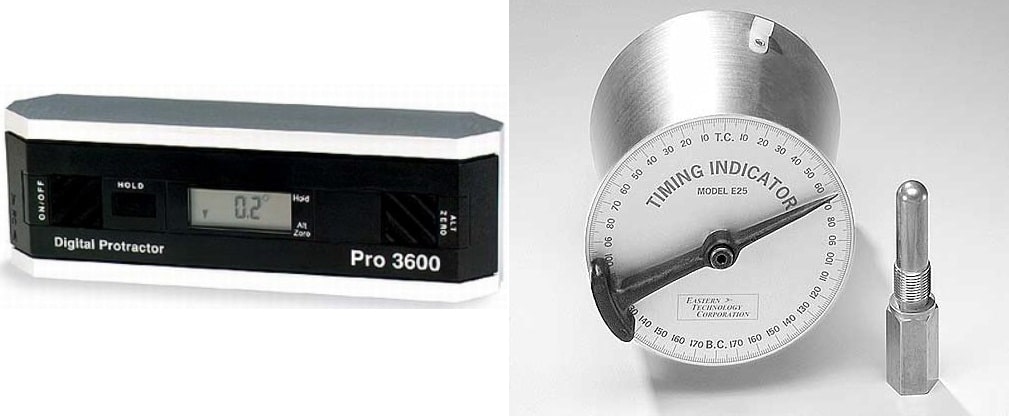
You know the rest of the story. The shop readjusted the mag timing using the old flower-pot method, and the owner flew home with his EGTs and CHTs right where they were supposed to be.
They just keep coming…
Then there’s this email I received recently from an A&P/IA at a shop in New England:
“Mike, I have a Beech F33A customer that recently developed a rough engine problem that occurs at higher power settings. Another shop changed the plugs, did a compression check, a ground run, cleaned the fuel screens and nozzles, etc. The plane reportedly flew fine for one flight, then ran rough and lost power next flight. The pilot reported that #6 flashed on the JPI engine monitor. I checked compressions cold and hot, and all passed. I checked the nozzles and takeoff fuel flow, performed a ground run and mag check, and all seemed okay. Another hard ground run full power brought out the problem with rough running and #6 JPI flashing.
“I checked compression #6 cylinder, 67/80 no leakage through the valves. I could hear some leakage through the rings until they click and seated during the compression check. I removed valves springs on intake and exhaust and found no excessive play in the guides, and all valves moved freely. I performed a third compression check of cylinder #6 with no valve springs installed and got 67/80. All lifters where replaced with new when the engine had a top overhaul about 900 hours ago. Lifters also where not found collapsed when rockers and springs where removed on #6 cyl.
“Do you have any ideas on what could be the problem? I would hate to pull the cylinder for nothing and find I still have the problem. Any help would be greatly appreciated.”
Ouch!
This airplane has a JPI engine monitor. Why didn’t anyone think to dump the data and have it analyzed before starting to perform exploratory surgery on this engine—ppulling spark plugs, fuel nozzles, rocker arms, valve springs, and so forth? To my way of thinking, that’s like having a cough and going directly to a thoracic surgeon without first seeing an internist or radiologist for a physical exam or an X-ray. I emailed the IA and suggested he dump the JPI data and upload it so I could take a look at it. Film at eleven.
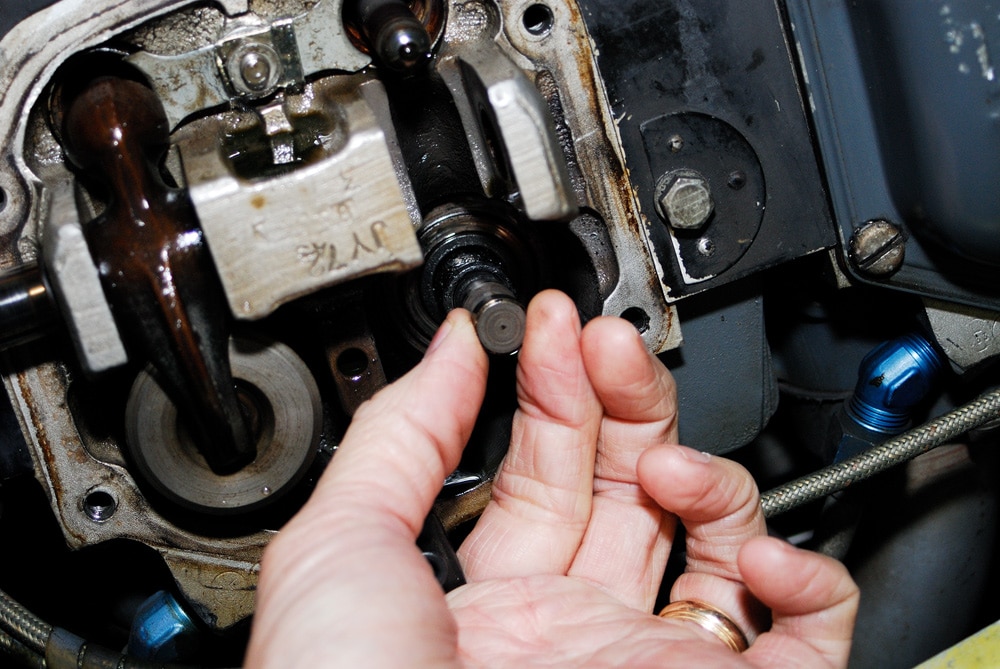
You bought a plane to fly it, not stress over maintenance.
At Savvy Aviation, we believe you shouldn’t have to navigate the complexities of aircraft maintenance alone. And you definitely shouldn’t be surprised when your shop’s invoice arrives.
Savvy Aviation isn’t a maintenance shop – we empower you with the knowledge and expert consultation you need to be in control of your own maintenance events – so your shop takes directives (not gives them). Whatever your maintenance needs, Savvy has a perfect plan for you: