Spark plugs start the fire going, and need some TLC
We all know what aircraft spark plugs do: They accept high-voltage pulses from a magneto or electronic ignition unit and produce an electric spark inside the cylinder’s combustion chamber to ignite the air/fuel mixture and initiate a flame front. They do this about 20 times per second under hostile conditions of extreme temperature and pressure.
A spark plug has three coaxial components: a center electrode, a ceramic insulator, and steel barrel. The barrel is threaded on both ends; one end screws into the cylinder head and the other end mates with the ignition lead. The insulator is made from aluminum oxide ceramic to provide good strength, thermal conductivity and dielectric properties. The center electrode comes in two flavors: massive and fine-wire.
Magic decoder ring
My twin Cessna has a dozen URHB32E spark plugs installed in the left engine and a dozen RHB32Es installed in the right engine. These cryptic-looking part numbers tell a lot about the characteristics of my spark plugs, so let’s take a moment to decode them.
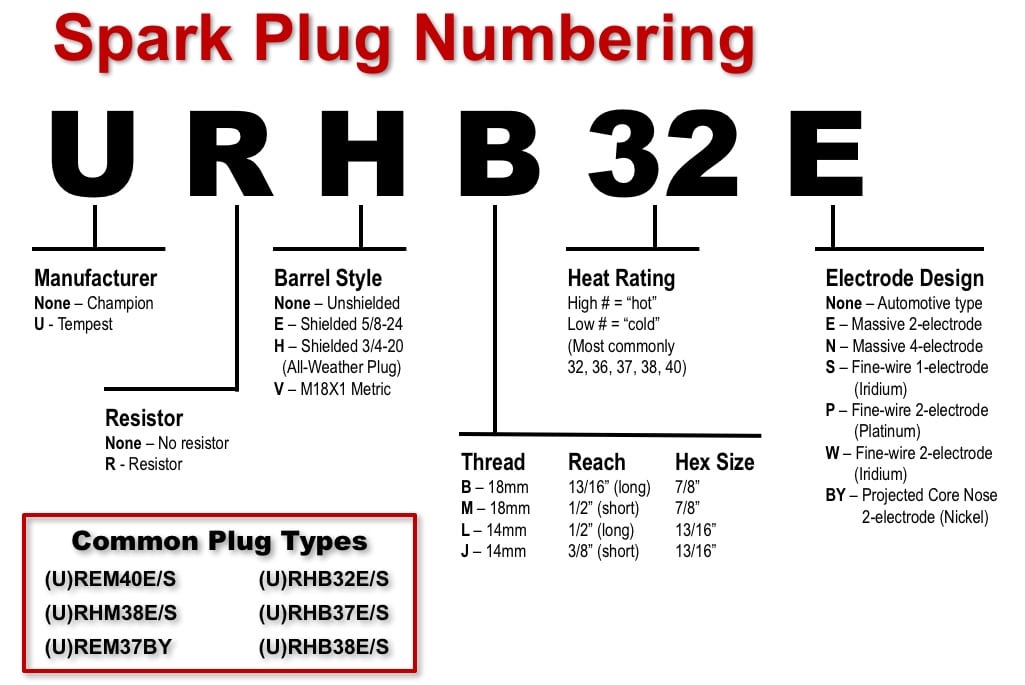
The “U” prefix on my left-engine plugs simply means that they come from Tempest Plus, one of the two U.S. firms that currently manufacture aviation spark plugs. The absence of the “U” prefix on my right-engine plugs denotes that they’re from Champion Aerospace.
The “R” in the part number denotes a resistor plug (as almost all aviation plugs are nowadays). The resistor serves as a current limiter that results in a longer-duration lower-current spark that reduces electrode erosion and prolongs plug life.
The “H” means the plug has 3/4-20 threads to mate with an “all-weather” ignition harness; an “E” would denote 5/8-24 threads. The “B” says the “business end” of the plug that screws into the cylinder head has 13/16-inch-long (“long reach”) threads; an “M” would denote 1/2-inch-long (“short-reach”) threads.
The “32” is the “heat rating” of the plug, a measure of its ability to transfer the heat of combustion from the nose core to the cylinder head. Hotter plugs (36-40) have a long insulator nose that creates a long heat dissipation path; colder plugs (29-32) have a shorter insulator nose and shorter heat dissipation path. The optimum heat rating is one that will cause the nose core to operate somewhere between 1,000°F and 1,300°F—hot enough to minimize plug-fouling deposits but cool enough to prevent preignition.
Finally, the “E” suffix denotes a massive-electrode plug, while an “S” would mean a fine-wire iridium plug. A “BY” suffix denotes a special kind of massive-electrode plug with a projected-core design to reduce fouling.
Common plugs include the short-reach REM40E, RHM38E and REM37BY, the long-reach RHB32E, RHB37E and RHB38E, their fine-wire brethren (with an S-suffix instead of E), and their Tempest equivalents (with a U-prefix). If you don’t know what’s in your engine, you should.
Wear and rotation
Whenever a spark jumps the gap between the spark plug’s center electrode and ground electrode, one of the electrodes loses a trace amount of metal due to ionization. This occurs 75,000 times per hour, and this loss of electrode metal gradually increases the gap and eventually erodes the electrode to the point that the plug becomes unserviceable.
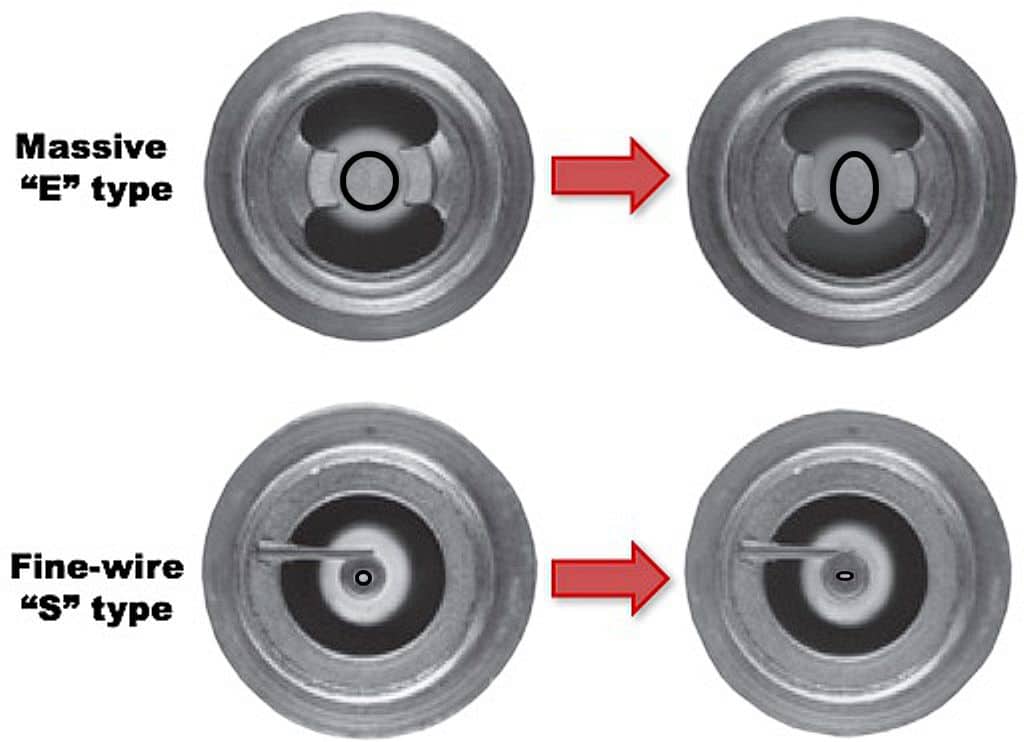
Center electrodes start off with a circular cross-section, and gradually become football-shaped in service due to erosion. When the short dimension reaches one-half the long dimension, it’s time to retire the plug. Similarly, when ground electrodes wear to half their original dimension, the plug should be retired.
Magnetos generate high-voltage pulses of alternating electrical polarity. When a spark plug is fired with a negative pulse, metal is lost from its center electrode; when fired with a positive pulse, metal is lost from the ground electrode(s). In a horizontally-opposed engine with an even number of cylinders, half the plugs in the engine suffer center-electrode erosion while the other half suffer erosion of the ground electrode(s). By periodically rotating the plugs to positions of opposite polarity, electrode wear can be balanced and the plug’s useful life extended.
Preventive maintenance
Spark plugs are traditionally removed for cleaning, gapping and rotation every 100 hours. However, I prefer to do regular in-flight LOP mag checks and perform spark plug maintenance only when these checks reveal less-than-stellar ignition performance; I find this “on-condition” approach results in reduced maintenance.
When it’s time to do preventive maintenance, I remove the plugs and put them in a spark plug tray so I won’t forget which plug came from which position in which cylinder. Then I inspect them for abnormal electrode wear, cracked nose core insulators, oil, carbon and lead deposits, or anything else that doesn’t look right.
If your plugs suffer from persistent fouling, the problem can usually be solved by using aggressively lean mixture settings, particularly during idle, taxi, and other ground operations. If fouling persists, the use of fine-wire (S-suffix) or projected-core (BY-suffix) plugs can help. For lead fouling, try adding Alcor TCP lead-scavenging additive to the fuel.
Next, the plugs are cleaned with a grit blaster (to remove oil and carbon deposits) and lead globules are removed with a vibrator or pick. Then the electrode gaps are measured with a wire-type feeler gauge and adjusted as necessary using a spark plug gapping tool. Most plugs specify a gap of 0.016 to 0.021 inch; I like to keep mine gapped “tight” at 0.016 inch to provide maximum “headroom” for the gap to grow in service before re-gapping is necessary. (Such “tight” gapping also reduces the risk of high-altitude misfire in turbocharged airplanes like mine.)
Installing plugs
Whether you’re reinstalling plugs after cleaning and gapping or installing brand new plugs, it’s crucial to use the right tools and procedures to ensure correct installation. When reinstalling plugs, remove and discard the used copper gaskets and install a new ones with the flat side facing the spark plug flange. (It’s possible to reuse the old, work-hardened copper gaskets if you anneal (soften) them by heating red-hot with a torch, but with new gaskets costing less than 50 cents apiece, I don’t think it’s worth the hassle.)
Carefully apply a small amount of aircraft spark plug thread lubricant/anti-seize (Champion 2812 or Tempest T556) to the second and third threads of the plug barrel. Apply sparingly, being extremely careful not to allow any of the thread lube to drip onto the electrodes or nose core insulator, otherwise the highly conductive lube might short out and ruin the plug.
Install the spark plug into its proper (rotated) location, ensuring plug moves from bottom to top (or vice versa) and from positive to negative polarity (or vice versa). Start the lube-prepared end of the plug into the threaded cylinder head boss using only your fingers. If the plug resists being screwed into the head with finger pressure, you may have cross-threaded it—so remove it and try again. Never force it with a wrench because you could ruin the plug or (even worse) the Heli-Coil insert in the cylinder head. In stubborn cases, you might want to use an aircraft spark plug “thread chaser” tool to clean up the Heli-Coil threads.
Once the plug has been screwed in finger-tight, use a special-purpose deep aircraft socket and a calibrated torque wrench to tighten the spark plug to its final torque. Continental calls for 25-30 foot-pounds (300-360 inch-pounds) of torque, while Lycoming calls for 30-35 foot-pounds (360-420 inch-pounds). Never install aircraft spark plugs using the TFAR (that feels about right) method; always use a torque wrench.
Prepare the ignition lead by wiping its contact spring and “cigarette” insulator with a lint-free rag moistened with MEK or acetone. Insert the cigarette into the spark plug and screw on the cap finger-tight, then use a 7/8-inch wrench to tighten the cap while holding the lead with a 7/16-inch end wrench to prevent it from twisting. It’s extremely important not to overtighten the cap (a rookie mistake), because doing so will make it damn near impossible to remove next time. While most A&Ps use the TFAR method here, I prefer to use a torque wrench to tighten the ignition lead cap to the recommended 10 foot-pounds (120 inch-pounds).
You can do this!
Spark plug maintenance is a task that aircraft owners are permitted to do themselves without A&P supervision. It’s easy to do, not terribly time-consuming, and requires only a few inexpensive tools. It’s also a lovely excuse for you to get an up-close-and-personal look at your engine on a regular basis—think of it as an advanced preflight inspection. I love to see owners get involved with the maintenance of their aircraft and doing your own oil changes and spark plug maintenance is a great way to get involved.
If you choose to do it yourself, there are various rookie mistakes to avoid. I’ve already mentioned several of these: Over-applying thread lube, overtightening ignition lead caps, allowing a lead to twist while tightening the cap, and reusing a work-hardened copper gasket. Don’t do these things.
Another common mistake is dropping a spark plug during removal or installation. Never reuse a spark plug that has been dropped; toss it in the trash. Dropping an aviation spark plug just a few inches onto a hard surface can fracture its fragile nose core insulator. Even an invisible hairline insulator crack can lead to destructive preignition that could trash your engine and ruin your day. Enough said.
Aircraft Spruce and Specialty Co. sells a nice “aircraft spark plug maintenance kit” for $120 that contains almost everything you need to maintain your spark plugs: spark plug tray, spark plug cleaner, feeler gauge, gap setting tool for massive-electrode plugs, aircraft spark plug socket, some copper gaskets and a bottle of thread lubricant/anti-seize. The only additional thing you’ll need is a suitable torque wrench, which you can pick up for about $20 from Harbor Freight. That’s a total investment of $140 that’ll more than pay for itself the very first time you do your own spark plug maintenance instead of paying your shop $100/hour to do it.
You bought a plane to fly it, not stress over maintenance.
At Savvy Aviation, we believe you shouldn’t have to navigate the complexities of aircraft maintenance alone. And you definitely shouldn’t be surprised when your shop’s invoice arrives.
Savvy Aviation isn’t a maintenance shop – we empower you with the knowledge and expert consultation you need to be in control of your own maintenance events – so your shop takes directives (not gives them). Whatever your maintenance needs, Savvy has a perfect plan for you: