When it comes to maintenance problems, the FAA might be able help you but only in very limited ways.
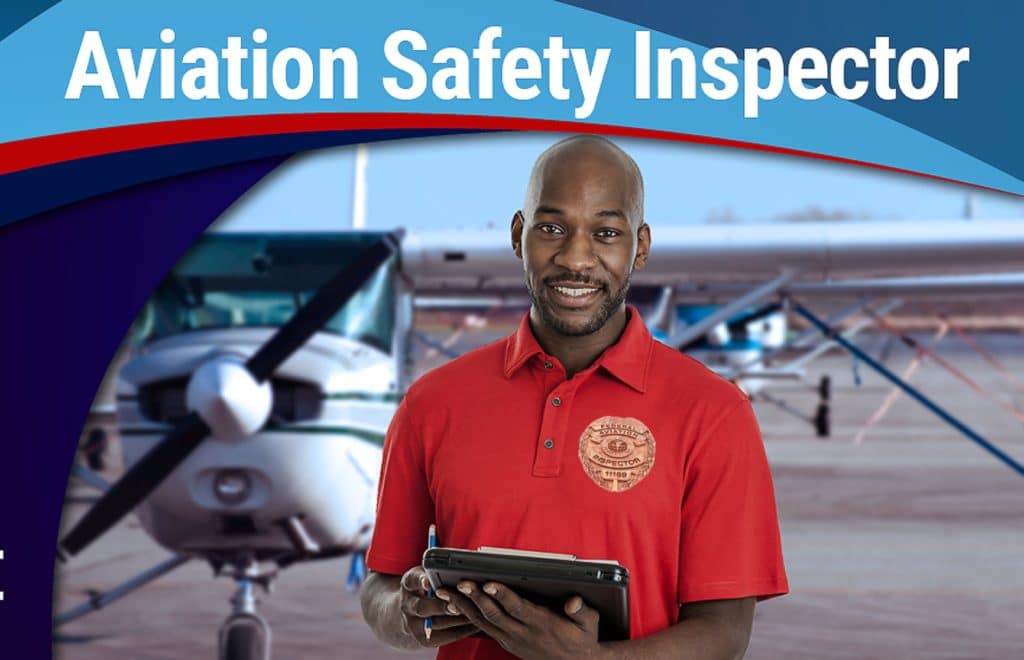
My April column, titled “Booted Out of Annual,” related a true story of a Bonanza owner who put his plane in the shop for its annual inspection, got into a disagreement with the shop’s manager, and wound up having his plane thrown out of the shop in pieces. The beleaguered owner ultimately contacted the local FSDO (against my advice) for the purpose of filing a complaint against the shop. An Airworthiness Safety Inspector (ASI) there appeared to take pity on him and helped him out of this predicament.
Shortly after this column appeared in print, I received a long, thoughtful email from a gentleman I’ll call “Fred” who was retired from the FAA after two decades working at both a FSDO and an FAA Regional Office. (I thought “Fred the Fed” had a nice ring to it.) Fred was very concerned that my April column might give AOPA PILOT readers a wrong impression about when it is and isn’t appropriate for an owner to ask the FSDO for help, and what FAA personnel are and aren’t allowed to do. Fred and I exchanged several lengthy emails on the subject, and I thought a lot of what he told me was too good not to share. So, I will quote some of Fred’s words of wisdom interspersed with a few of my own thoughts.
“Mike, I have to point out some things concerning your account of the ‘compassionate fed’,” Fred began. He first addressed the fact that the ASI came to look at the Bonanza equipped with a flashlight and mirror.
Feds Can’t Do Maintenance
“My problem is that your story infers (to a national AOPA audience) that it is appropriate for an FAA maintenance inspector to inspect a private aircraft at the request of its owner and then make a determination of what further maintenance would allow it to be eligible for a ferry permit,” Fred said. “This could be construed as an FAA employee acting on behalf of an owner and arguably performing a maintenance function (inspection) which is outside of the scope of their responsibilities as an FAA employee. The inspection functions you described should have been accomplished by a qualified technician who should have presented the FAA with an application for a special flight permit. The FAA inspector’s job is to review and decide whether or not to approve it.”
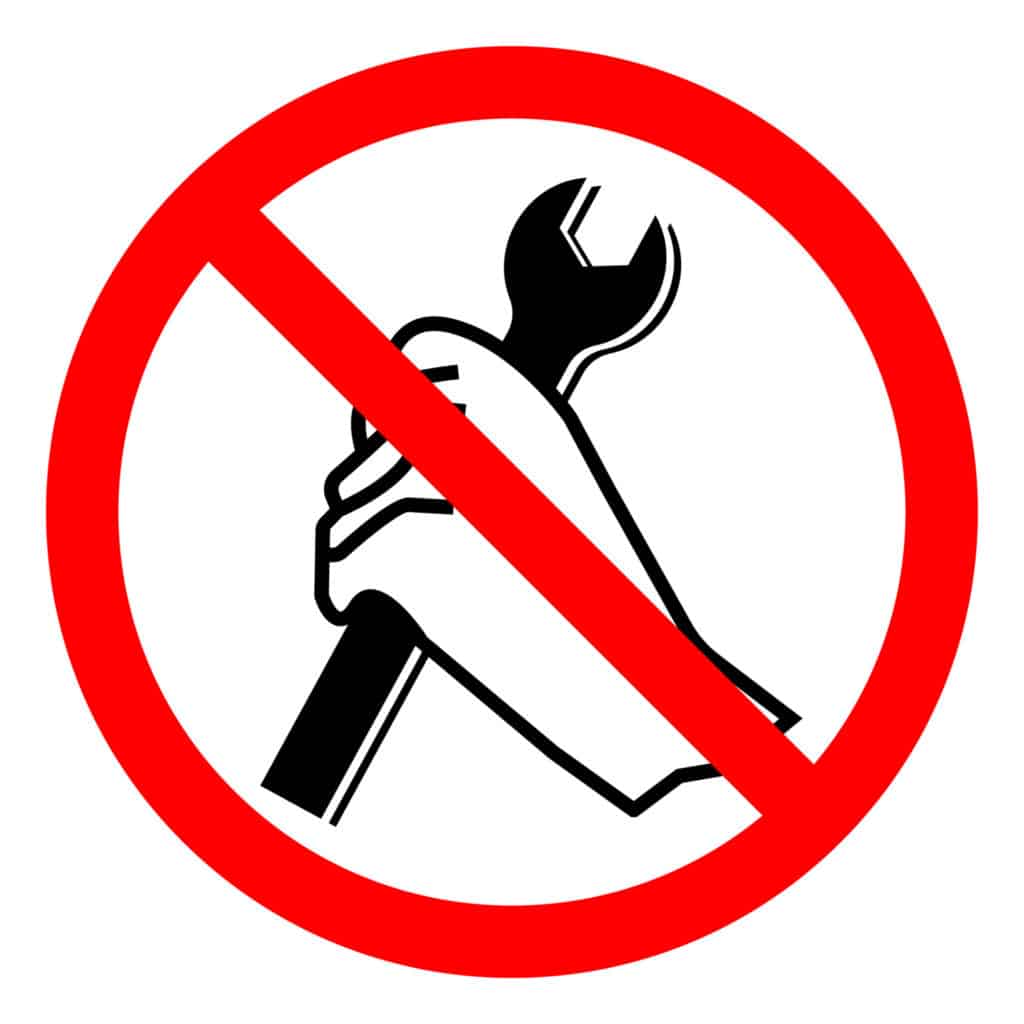
Indeed, the normal protocol for obtaining a special flight permit (“ferry permit”) is for the owner to engage an A&P mechanic to inspect the aircraft, make a determination that it is in condition to make the proposed ferry flight safely, and make and sign a logbook entry stating as much. It is quite unusual for an FAA inspector to make this determination, although the inspector does have the discretion to examine the aircraft if he feels that is necessary to make a decision whether or not to approve the ferry permit.
It certainly would be improper for an FAA inspector to do this at the behest of the aircraft owner. I don’t think the Bonanza owner asked the ASI to come look at his airplane. The owner’s purpose in contacting the FSDO was to file a complaint against the shop.
“In follow up to a complaint or any investigation, an inspector can physically inspect an aircraft and its records, but only on behalf of the government and then only to determine its status in regards to compliance,” Fred continued. “It may be proper for the FAA to investigate a situation where one party claims a condition is un airworthy while the other disagrees. But the investigation must be fair and completely impartial. An inspector cannot perform ‘favors’ for private parties. They are not authorized to perform actual maintenance as a part of their regulatory duties. In fact they can lose their job for doing so.”
The situation with the Bonanza owner hinged on the airworthiness of the camshaft. The owner believed it was airworthy. The A&P/IA who performed the annual inspection agreed. My staff viewed high-resolution photos of the cam and also agreed. However, the manager of the shop (who is not an A&P) was convinced for whatever reason that the engine needed to be torn down. When the owner wasn’t willing to do that, the manager threw the airplane out of his shop—in pieces.
Given the sharp difference of opinion between the shop manager and the A&P/IA who worked for him, it doesn’t strike me as unreasonable or inappropriate for the FAA inspector to take a looksee for himself before deciding whether or not to approve a ferry permit. The shop that threw the Bonanza out was the only shop on the field. Prior to contacting the FAA, the owner made multiple attempts to persuade A&Ps from nearby airports to help him secure a ferry permit, but none of them were willing to get crosswise with the vindictive shop manager whose reputation obviously preceded him. The FAA inspector clearly did not believe that he was committing maintenance on the Bonanza by looking at it, since he didn’t make or sign any logbook entries.
Feds Can’t Touch Business Disputes
“The situation you described concerning the maintenance shop appears to be a business dispute and not a regulatory or safety-related problem,” Fred said. “The FAA does not referee or resolve business disputes. There is no FAA regulation that requires a shop or a technician to complete an annual inspection, nor to reassemble an aircraft.”
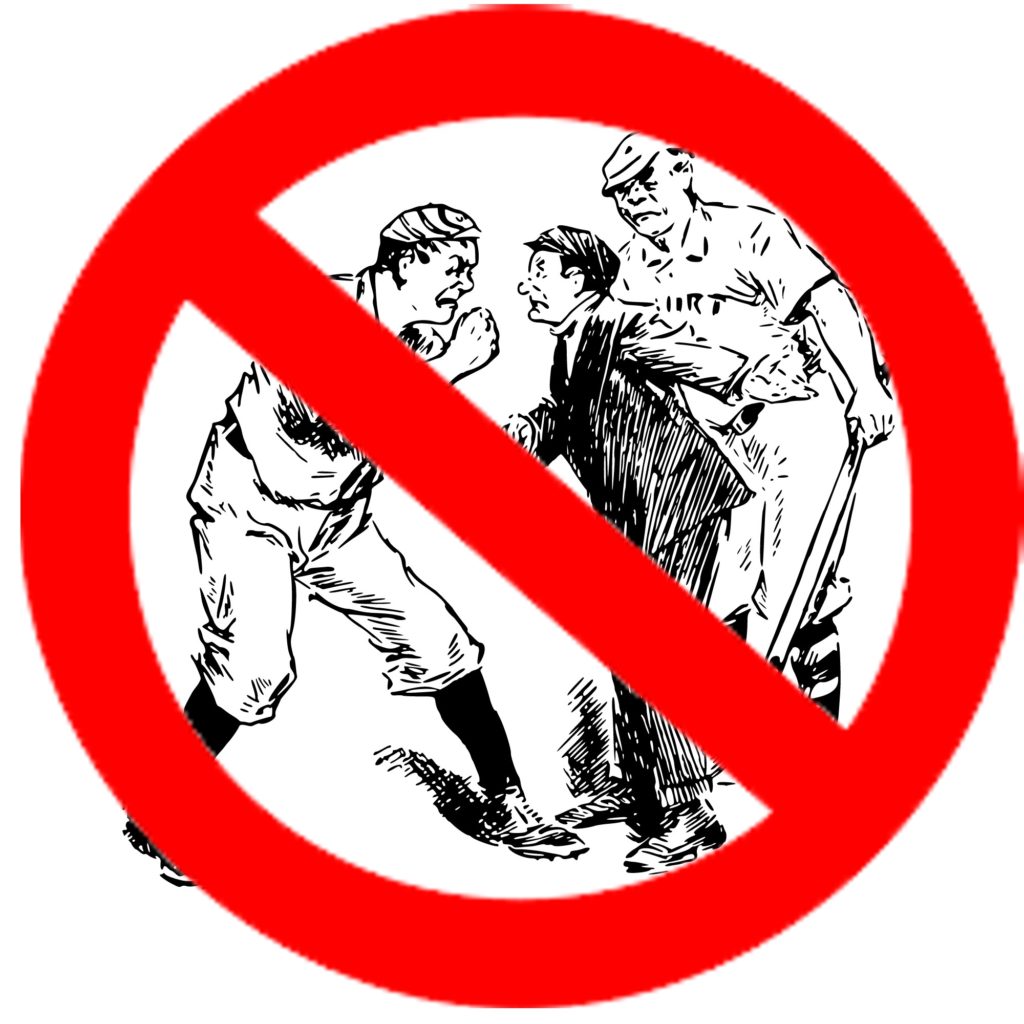
It is very common in my experience for aircraft owners to complain to the FAA about mistreatment by a maintenance shop that is essentially a business dispute, not a regulatory violation or threat to safety. I always try to discourage owners from doing this, but they don’t always take my advice. FSDO inspectors typically won’t touch such things with a ten-foot pole, and rightly so.
In the case of the Bonanza, the shop manager had the authority to terminate the inspection prematurely and eject the airplane from his shop. In doing so, his actions may have damaged the aircraft owner, but that’s a civil matter for the owner, shop, and their respective lawyers to resolve. Even if the owner was damaged by the actions of the shop manager, the damages would probably not rise to the level where litigation would provide a viable remedy (unless the owner took the shop to small claims court). In any case, this is definitely not something that the FAA will adjudicate.
“Sometimes, the FSDO supervisor might allow an inspector to get involved in a situation like this to attempt a peaceful resolution, but never to use the authority of the government to resolve a business dispute,” Fred added. This would be a rare situation indeed. Personally I’ve never seen it happen.
“What the shop did might have been a breech of contract or work agreements , but it’s not an FAA matter,” Fred said. “In this case there was no allegation the shop or its employees were in non-compliance with any FAA regulation.”
Feds Might Not Have Jurisdiction
“The shop was not reported to be a repair station and the manager is not required to hold a mechanic certificate,” Fred observed. “Only the person performing the actual maintenance or inspection is accountable to the FAA. Assuming that prior maintenance and record keeping was accomplished properly, if the shop or its owner decides to end an inspection or stop work, that decision is beyond the scope of FAA responsibility, period.”
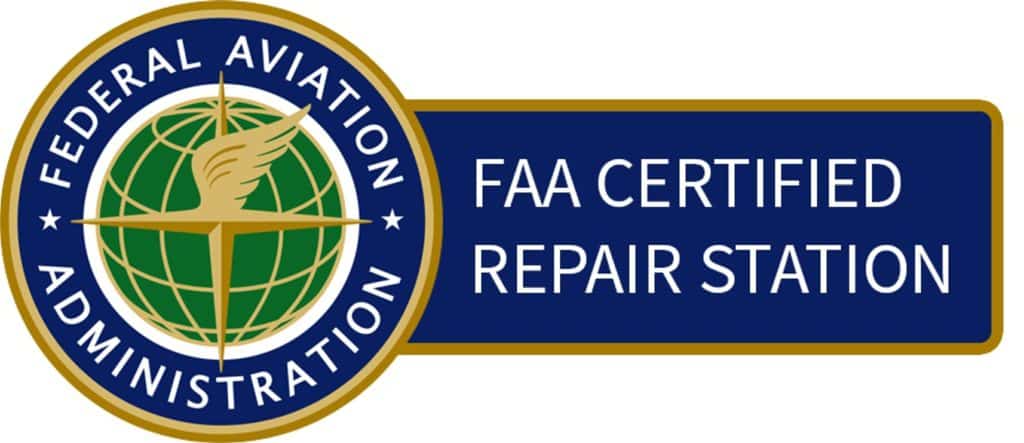
Fred raised an issue that I hadn’t previously considered: Only certificate holders are within the scope of FAA jurisdiction. In this case, the shop manager (the bad guy) didn’t hold an FAA certificate and the shop didn’t, either. The only people that could get in trouble with the FAA were the A&P/IA (a good guy) and the aircraft owner. The uncertificated manager and the uncertificated shop were both pretty much off limits to the FAA.
It’s important for aircraft owners to understand that there are two kinds of maintenance shops: Part 145 Repair Stations and shops that aren’t repair stations. Most small GA shops are not repair stations; big shops and those that work on turbines are more commonly repair stations. A Part 145 Repair Station holds an FAA certificate and receives a much greater degree of FAA oversight. By contrast, a non-repair station is just a collection of certificated mechanics flying in close formation—the shop itself is not accountable to the FAA, only the mechanics who work there are accountable as individuals.
Feds Avoid Taking Risks
“Another problem for the government involves liability if an employee makes a decision when working outside of or even close to the reasonable limits of their authority—and then something bad happens,” Fred told me. “That costs the taxpayers! The government has almost unlimited pockets when it comes to liability and gets sued often.”
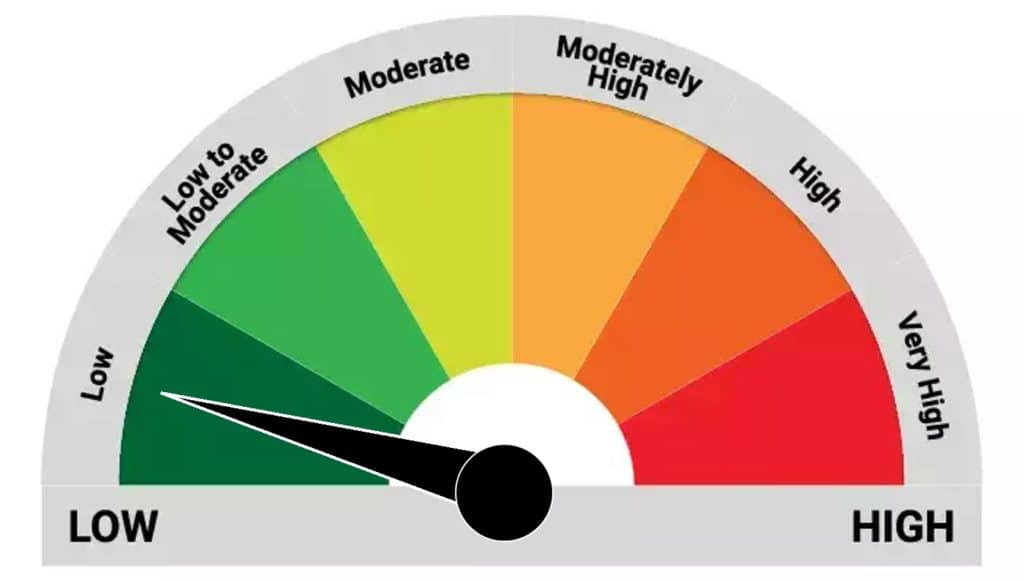
I’ve long noticed that government employees seem to be more risk averse than those in private industry. Fred’s observation certainly helps explain why
“The ASI who became involved with the Bonanza probably did go out on a limb,” I confessed to Fred. “He may well have put his job at risk to help obtsin a good outcome for the aircraft owner. That makes him a hero in my book.”
“I agree with your assessment,” Fred told me. (He no longer works for the FAA, so I guess he’s allowed to say that.)
You bought a plane to fly it, not stress over maintenance.
At Savvy Aviation, we believe you shouldn’t have to navigate the complexities of aircraft maintenance alone. And you definitely shouldn’t be surprised when your shop’s invoice arrives.
Savvy Aviation isn’t a maintenance shop – we empower you with the knowledge and expert consultation you need to be in control of your own maintenance events – so your shop takes directives (not gives them). Whatever your maintenance needs, Savvy has a perfect plan for you: