An FAA review of 10 years of NTSB data tries to quantify the risk.
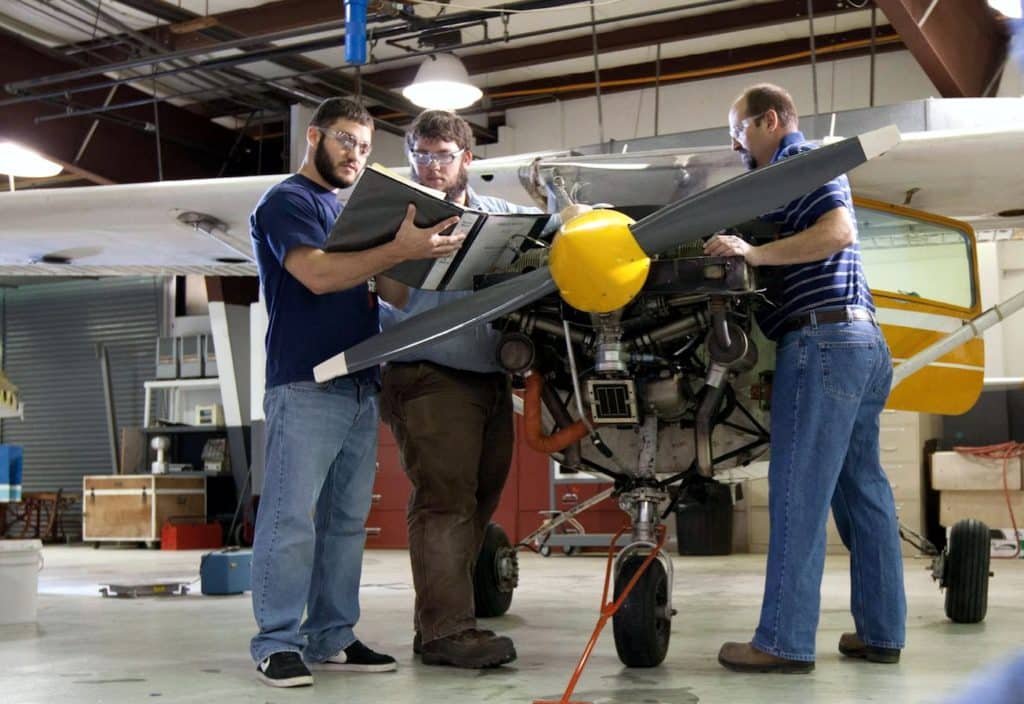
I’ve been known preach about the virtues of maintenance minimalism—a.k.a. “if it ain’t broke, don’t fix it”—and the risk of maintenance-induced failures—a.k.a. “MIFs.” But just how risky is maintenance? How often to MIFs occur? How serious are the consequences when they do?
When asked these questions, I usually lick my finger, hold it up in the breeze, and say that roughly three-quarters of GA accidents are pilot-caused and one-quarter are machine-caused. Licking again, I say that of the machine-caused ones, roughly half are mechanic-caused (i.e., MIFs). That would put the fraction of GA accidents caused by MIFs at around one-eighth give or take a few spitballs.
While cleaning out my office recently and rummaging through stacks of old papers (most of which I threw in the trash), I ran into an old FAA study that might shed a little more light on this subject, and help quantify the risk of maintenance more accurately than my aforementioned spit balling. Published in December 2002, the FAA study titled General Aviation Maintenance-Related Accidents: A Review of Ten Years of NTSB Data analyzed NTSB accident investigation reports involving GA accidents between 1988 and 1997 that had at least one maintenance-related issue listed as the probable cause or a contributing factor.
Maintenance-Related Accidents
The NTSB reported on 20,884 GA accidents during that 10-year period, and 1,474 (7.1%) of those reported at least one maintenance-related error as a primary cause or factor in the accident and 18% of these accidents were fatal. They were responsible for 504 fatalities, an average of over 50 fatalities per year. Some 86% of the accidents involved airplanes, 12% involved helicopters, and the remaining 2% involved gliders, balloons, gyroplanes, blimps and ultralights.
What kind of maintenance caused or contributed to these accidents? Well, the NTSB categorizes maintenance activities using the following strange taxonomy:
- Adjustment
- Airworthiness Directives
- Alignment
- Annual Inspection
- Design Change
- Installation
- Lubrication
- Maintenance
- Maintenance Inspection
- Major Alteration
- Major Overhaul
- Major repair
- Modification
- Overhaul
- Rebuild
- Replacement
- Service Bulletins/Letters
- Servicing
This coding system seems a bit inscrutable. The “Maintenance” category seems a bit overbroad and ambiguous—what’s included in that? What’s the difference between “Design Change” and “Major Alteration”? Why is “Servicing” included, since that’s a term normally used for such non-maintenance activities as fueling and adding oil. The FAA analysts who wrote the study seemed baffled, too.
Significantly, the NTSB cited “Installation” as the most frequent of these maintenance categories, accounting for 20% of the 1,474 maintenance-related accidents. Another 22% involved the two “inspection” categories, “Maintenance Inspection” (14%) and “Annual Inspection” (8%). The ambiguous catch-all “Maintenance” category came in at 15%. All the other categories came in at 5% or less.
Installation problems were not only the most frequently cited maintenance issue, they also resulted in the most severe consequences. Accidents involving installation errors accounted for 100 fatalities and 210 injuries, with 59% of the installation-related accidents resulting in injuries, fatalities, or both.
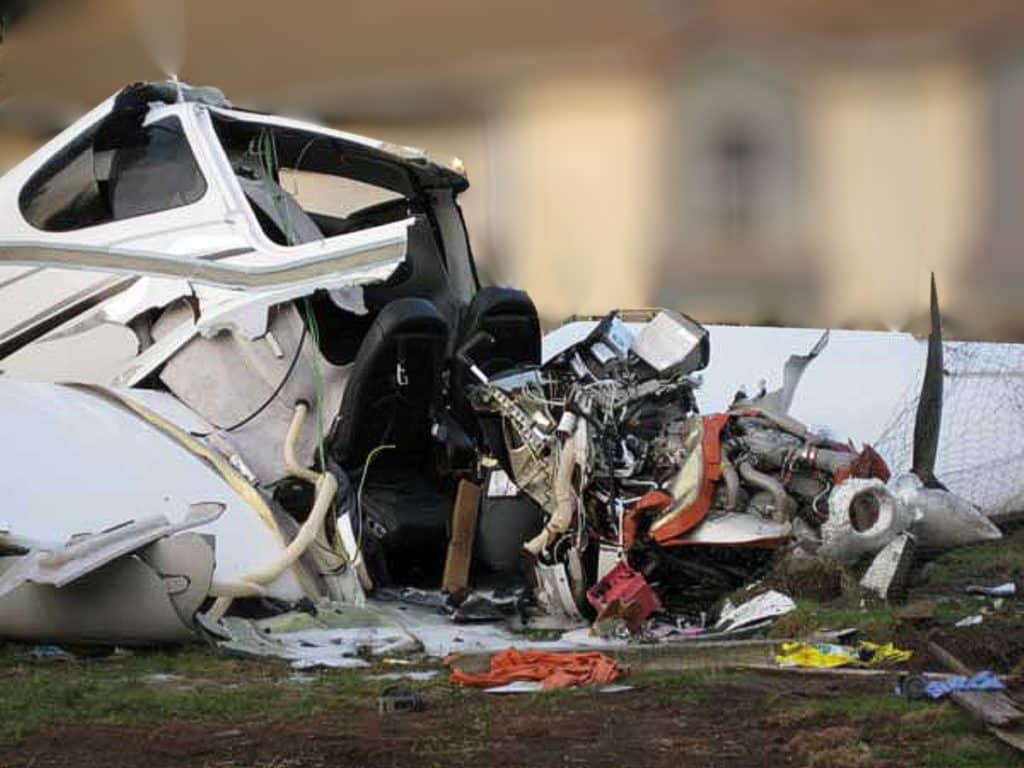
Installation Errors
Because installation errors were so deadly, the FAA analysts drilled down further. They found that the majority of installation errors involved the powerplant (56%), followed by flight controls (13%), landing gear (10%), rotorcraft rotors (10%), and electrical (5%).
The type of errors included incorrect attachment (29%), incorrect connection (22%), omission (22%), wrong part installed (17%), and reversed installation (10%). Almost all (91%) of the installation errors were made by certified A&P mechanics, with only 9% by uncertified personnel. The vast majority (86%) resulted in emergency landings—two-thirds of which involved injuries, fatalities, or both—with only 14% ending up returning to the departure airport or continuing to the destination.
While more than half the installation-error accidents involved the powerplant, installation errors involving flight controls or the electrical system were the most likely to result in injury or death. The highest percentage of injury/fatality accidents by system were electrical system (73%), flight controls (69%), powerplant (62%), and rotor system (52%).
It’s Probably Worse
The FAA study ended with a “Discussion” section in which the analysts pointed out that the percentage of GA accidents they attributed to maintenance (7.1%) is far lower than other well-respected studies that have found the rate to be close to 20%. The study authors attributed this discrepancy to the NTSB’s methodology of codifying accident causes and contributing factors in a way that the analysts believed often failed to assign a maintenance-related code to accidents that were actually maintenance-related. “As a result, there are probably many more maintenance-related accident reports in the NTSB Database that were not included in this study because they were not designated with a maintenance code,” the study concluded.
The authors pointed out that while helicopters comprise only 3% of the GA fleet, they were involved in 12.4% of the maintenance-related accidents. This reflects the maintenance-intensive nature of rotorcraft. However, the study suggests that the kinds of maintenance errors being made on helicopters is not very different from the kinds of errors that afflict airplanes.
The single most frequent kind of maintenance-related accident cause is installation errors involving the powerplant. I’ve written quite a lot about my aversion to doing cylinder work on piston engines unless it’s absolutely unavoidable because there are so many ways that installation of a cylinder can be screwed up even by experienced A&Ps. I’ve often expressed the opinion that most A&Ps do not have the appropriate level of fear when it comes to installing cylinders, often provoking howls of protest from my A&P readers.
The authors of the FAA study seem to agree with me that mechanics need better guidance on risk management. “It seems reasonable to develop guidance to aid maintainers on the inherent risks of maintaining various general aviation aircraft,” the study concludes. “These guidelines could be empirically developed, informed by accident and incident event data. Thus, a comprehensive database of maintenance error data becomes crucial.”
Will A&Ps Confess their sins?
That’s a lot easier said than done, however. Our current GA maintenance culture seems spring-loaded to conceal its errors rather than fess up to them. “Nearly every mechanical failure is investigated and archived so that the failure rate of a specific type of component can be analyzed and precisely tracked,” the report says. “However, the same investigative and analytical resources are not applied to cases of human error in the maintenance shop.”
What would it take to accomplish this? “A major obstacle to 100% error reporting in maintenance is the punitive work environment so pervasive industry-wide,” the report goes on. “Many aviation maintenance technicians (AMTs) may hesitate to report their own errors for fear of reprisal from management or government. Therefore, any maintenance-error reporting system will likely require some level of immunity to disciplinary action to be successful.”
While the Aviation Safety Reporting System (ASRS) theoretically offers mechanics immunity from FAA sanction for unintentional errors, it doesn’t protect them from employer sanctions. It appears that ASRS is rarely used by mechanics: The ASRS database reveals 172,000 reports by flight crewmembers, 24,000 by air traffic controllers, but only 6,000 by maintenance technicians.
You bought a plane to fly it, not stress over maintenance.
At Savvy Aviation, we believe you shouldn’t have to navigate the complexities of aircraft maintenance alone. And you definitely shouldn’t be surprised when your shop’s invoice arrives.
Savvy Aviation isn’t a maintenance shop – we empower you with the knowledge and expert consultation you need to be in control of your own maintenance events – so your shop takes directives (not gives them). Whatever your maintenance needs, Savvy has a perfect plan for you: