The best way to diagnose an engine problem is usually in the air.
“My engine started running rough about halfway home yesterday,” my client reported, “so I dropped it off at the service center. Could you please work with my mechanic to troubleshoot this problem?”
Arggghhh!!!
So many aircraft owners have a knee-jerk reaction to put their airplane in the shop whenever problems arise. Apparently they assume that diagnosing the problem is the job of a mechanic. That’s like having a bellyache and making an appointment to see a surgeon. Like surgeons, aircraft mechanics are primarily in the business of fixing things that aren’t working properly. But before you go to a surgeon or a mechanic, you need to figure out what’s wrong. You need a diagnosis.
Every diagnosis starts with data. If you’re feeling unwell, the initial data would probably come from a Q and A session with your primary care-physician resulting in a detailed account of your symptoms. Additional tests such as blood work, electrocardiogram, imaging studies, needle biopsy, etc., might be used to gather additional data to refine and confirm the diagnosis.
Similarly, if your aircraft engine seems unwell, the initial data would typically come from your detailed account of its symptoms (“squawk”) and a dump of digital engine monitor data. Additional tests such as oil and oil filter analysis, compression test, borescope inspection, etc., might be used to gather additional data to refine and confirm the diagnosis.
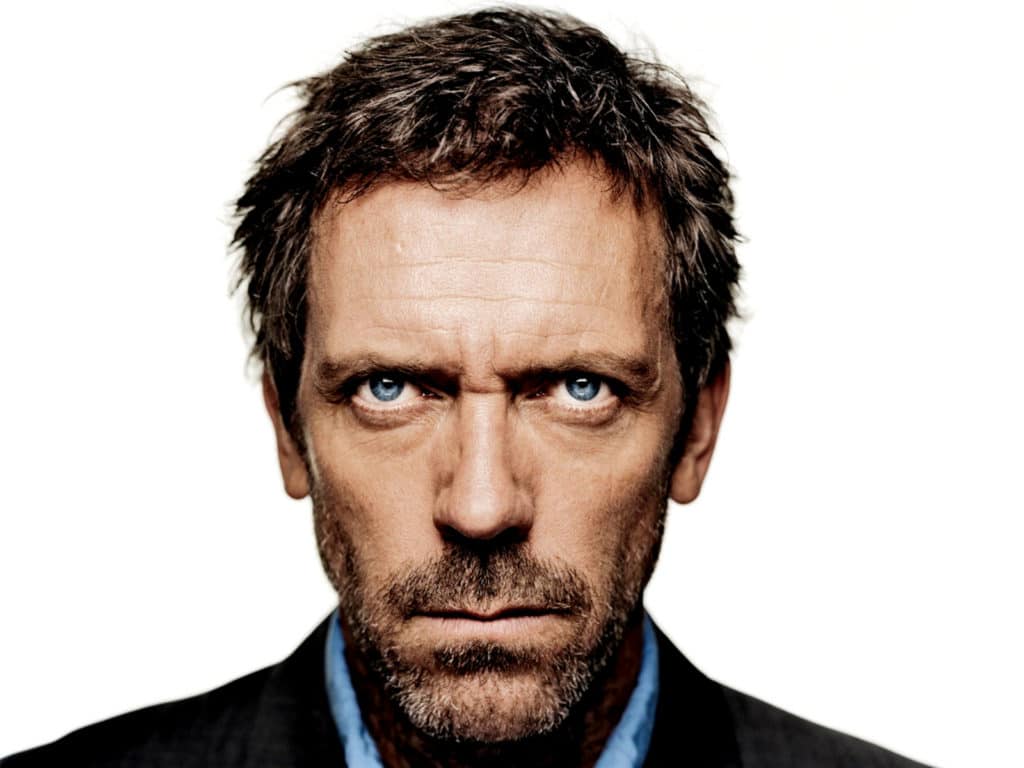
If the mechanic’s role is that of a surgeon, the aircraft owner’s role is that of primary-care physician. It is up to you to document your engine’s symptoms and to obtain the engine monitor data. Chances are that you’ll also need to analyze that data—or to send it to someone who knows how to analyze it—since very few mechanics have any training or experience in engine monitor data analysis. (This is something that hopefully will change gradually as mechanic training is dragged kicking and screaming into the 21st century.)
The Owner as Test Pilot
The initial data required to diagnose most engine problems has to be gathered while the airplane is airborne. Only the grossest and most obvious problems—like an oil leak or a dead magneto—can be diagnosed in the maintenance hangar or during ground runs. Therefore, the responsibility for gathering that data will most likely fall upon you, not your mechanic. Like it or not, you’re a test pilot.
Typically when one of my clients reports an engine problem, the first thing I ask him or her to do is to fly the airplane and conduct one or more flight-test profiles, then dump the engine monitor data for me to analyze. Eventually, I hope to get the owner trained to conduct the flight-test profiles without me having to ask, eliminating the need for a separate test flight.
The most useful of these flight-test profiles include:
- Ignition stress test
- Mixture distribution test
- Induction leak test
Let’s look at each of these tests in detail.
Ignition stress test
Also known as the “in-flight LOP mag check,” the ignition stress test is the best way to evaluate the performance of your engine’s ignition system. Every student pilot is taught to perform a mag check during the pre-flight engine run-up, but many pilots have never shut off a magneto in flight and are uncomfortable with the idea. That’s a shame, because the in-flight ignition stress test is far more exacting and revealing of any ignition system problems than the usual run-up. The typical pre-flight mag check can detect only the grossest ignition system defects, while the in-flight stress test will reveal much more subtle ignition issues.
The best ignition system test you can perform is an in-flight mag check with the engine leaned aggressively lean of peak EGT (LOP). If your engine is not capable of operating smoothly when LOP, then do the test as the leanest mixture at which the engine does run smoothly. We want the mixture to be as lean as possible because the leaner the air-fuel mixture, the more difficult it is to ignite. Therefore, if your ignition system performance is marginal, it will show up during a lean (preferably LOP) in-flight test long before it becomes apparent in any other phase of operation.
If your engine monitor has a user-programmable sampling rate, it’s best to set it to the highest rate possible. For example, JPI EDM-series monitors have a default sampling interval of 6 seconds, but can be programmed to use a 2-second interval. When you’re done with the flight-test profiles, you can reset the sampling rate to the default value. (NOTE: This applies to all of the flight-test profiles discussed in this article.)
The ignition stress test should be performed in normal cruise configuration with the mixture set as lean as possible consistent with smooth engine operation (preferably LOP). Place your engine monitor in “normalize mode” which sets all the EGT bars to mid-scale and increases the sensitivity of the bar-graph display. Now go through the usual mag check procedure: BOTH-LEFT-BOTH-RIGHT-BOTH for singles, or shutting off one mag toggle switch at a time (left to right) for twins.
Do not rush this procedure. Perform it very slowly, making sure that you run the engine on each individual magneto for at least 10 engine monitor sample intervals before moving on to the next phase. If the monitor samples every 6 seconds, run on each individual magneto for a minimum of one minute; if the monitor samples ever 2 seconds, run on each mag for at least 20 seconds. Return to two-mag operation for a similar length of time between single-mag runs.
If your ignition system is healthy, when you switch to single-magneto operation you should see all EGT bars rise by 50°F to 100°F. They may not all rise the same amount; in fact, it’s perfectly normal to see even-numbered cylinders rise more than odd-numbered ones (or vice-versa). What’s important is that all EGT bars rise, and that all remain fairly stable at their elevated values. You will feel a small but perceptible loss of power during single-mag operation, but the engine should continue to run smoothly without uncomfortable roughness. (The engine will always run slightly less smooth on one magneto than on two, but roughness sufficient to get your non-pilot passengers to ask “what’s wrong with the engine” is definitely too much!)
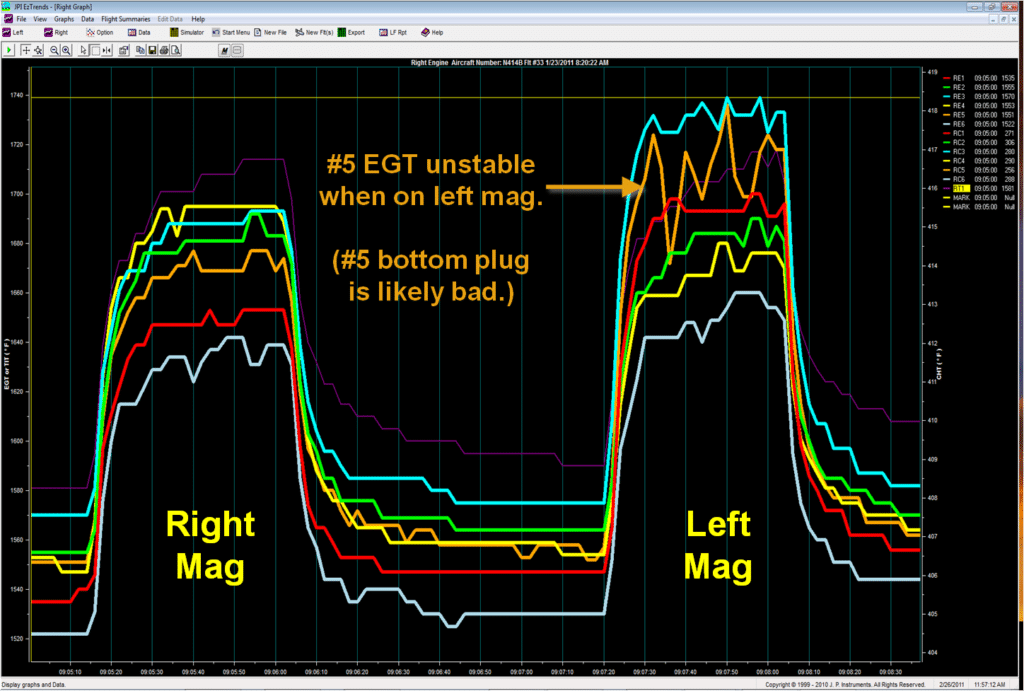
Once on the ground, dump the engine monitor data and analyze it. You will be able to see the test results much more clearly by graphing the engine monitor data than by looking at the instrument during the test flight. Figure 2 shows a good example of an ignition stress test—note how #5 EGT goes unstable when the engine is running on the left mag only, indicating that the bottom spark plug in cylinder #5 has a problem. Also notice that all EGTs rise more during left-mag operation than during right-mag operation, suggesting that the two mags are timed differently.
I recommend performing the ignition stress test on a regular basis—I do it on most every flight, generally at the end of the cruise phase just before starting my descent. It should always be performed any time any sort of engine anomaly is suspected.
Mixture distribution test
Also known as the “GAMI lean test,” the mixture distribution test determines how much mixture variation exists among the cylinders of your engine. It can detect dirty or wrong-sized fuel injector nozzles, intake valve problems, induction leaks, and other engine anomalies that can cause uneven mixtures among cylinders.
The test is usually performed at about 65% cruise power at an altitude of 6,000 to 10,000 feet. For normally-aspirated engines, it’s best to perform the test at a high enough altitude that the throttle can be wide-open (or close).
If your engine monitor captures fuel flow, then you can perform the test and analyze the data later. If it doesn’t capture fuel flow, then you’ll need to write down fuel flow readings during the test procedure. (The following description assumes that the monitor does not capture fuel flow and that the data has to be recorded manually.)
Starting with a full-rich mixture, write down the fuel flow and the EGT of each cylinder. Now lean very, very slowly (a vernier mixture control really helps) until the first cylinder reaches peak EGT, and note peak EGT value for that cylinder and the exact fuel flow (to the nearest 0.1 GPH or 1 PPH) at which that peak EGTwas achieved . Continue leaning very, very slowly until each cylinder reaches peak EGT, and again write down the peak EGT value for each cylinder and the fuel flow at which each peak was achieved.
It’s usually best to repeat this procedure several times to ensure reliable results.
Once the data has been gathered, you can derive two valuable pieces of information. The first is the difference between full-rich EGT and peak EGT for each cylinder (referred to as the “lean range” for that cylinder), and the second is the difference in fuel flow between the first cylinder and the last cylinder to reach peak EGT (referred to as the “GAMI spread”).
For most engines, the lean range of each cylinder—the EGT rise from full-rich to peak—should be around 250°F to 300°F. If any cylinder has a substantially lower lean range than the others, it may be operating too lean at takeoff power and might be vulnerable to overheating or detonation. (Suspect a clogged injector nozzle or an induction leak.)
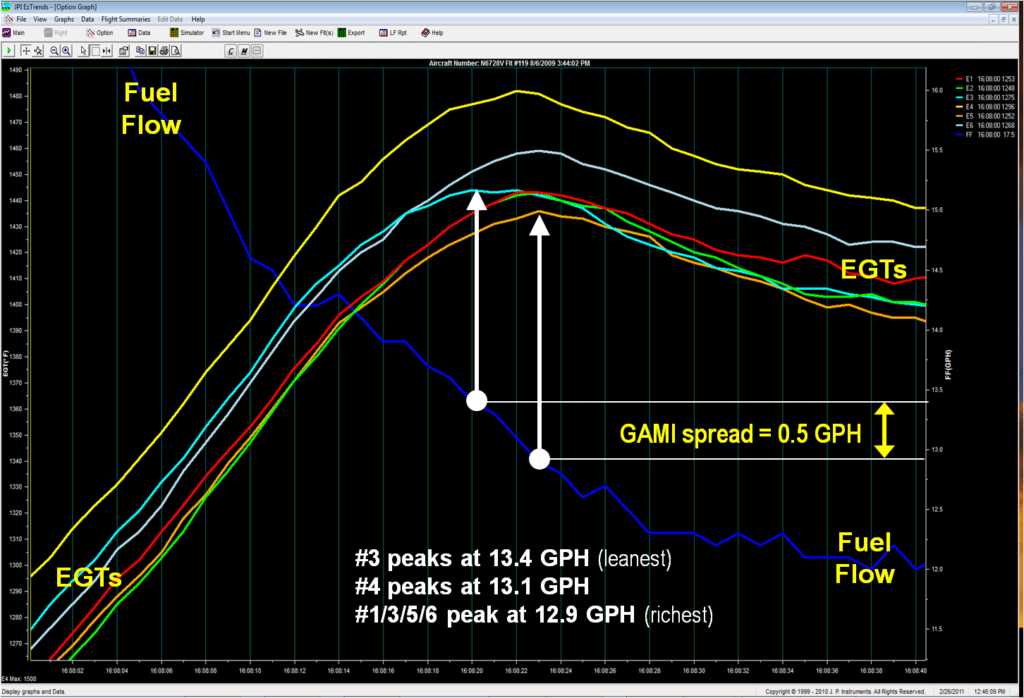
The “GAMI spread” is a measure of uneven mixture distribution. The smaller the spread, the better. A fuel-injected engine with properly tuned fuel nozzles will exhibit a GAMI spread in the vicinity of 0.5 GPH. Using stock non-tuned nozzles, injected Lycoming and crossflow Continental engines typically have a spread around 1.0 GPH, and injected bottom-induction Continentals often have a spread of 1.5 GPH or more. Some carbureted engines (e.g., Continental O-470-series) can have spreads in the 2–3 GPH range. Experience indicates that if your engine has a GAMI spread above 1.0 GPH, it probably won’t be able to run smoothly at LOP mixtures.
Figure 3 shows a mixture distribution test that reveals a GAMI spread of 0.5 GPH, which is quite good. Note that this engine monitor is configured to capture fuel flow information, making the analysis very easy and eliminating the need to record the fuel flow information manually.
I recommend performing this test every 12 months or 100 hours, whichever comes first, and also any time any sort of engine anomaly is suspected.
Induction leak test
This in-flight test is an effective method for detecting leaks in the engine’s induction system. It is best accomplished in level cruise flight at about 5,000 feet MSL. It consists of a pair of tests: the high-MP test and the low-MP test.
For the high-MP test, start with a relatively high power setting—wide-open throttle for normally aspirated engines, or MP equal to outside ambient pressure for turbocharged engines—and full-rich mixture. Write down the EGT for each cylinder.
For the low-MP test, reduce MP by about 10 inches and again write down the EGT for each cylinder.
Disregard the absolute EGT values. Instead, calculate the change in EGT (“delta”) for each cylinder between the high-MP and low-MP tests. Ideally, the amount of EGT change should be roughly the same for all cylinders. If one cylinder (or two adjacent cylinders) exhibit(s) significantly less change than the others, suspect an induction system leak affecting that cylinder (or those adjacent cylinders).
Here’s the principle behind this test: During the high-MP test, the induction manifold pressure is very close to outside ambient pressure, so any induction leak will have little or no effect on engine operation. During the low-MP test, the manifold pressure is significantly lower than outside ambient (by about 10 inches), so any induction leak will cause the affected cylinder (or cylinders) to run substantially leaner than the others, resulting in a smaller drop in EGT than the others.
I recommend performing this test any time a MP or mixture distribution anomaly is suspected.
Now put on your test-pilot cap and go fly some of these flight-test profiles!
You bought a plane to fly it, not stress over maintenance.
At Savvy Aviation, we believe you shouldn’t have to navigate the complexities of aircraft maintenance alone. And you definitely shouldn’t be surprised when your shop’s invoice arrives.
Savvy Aviation isn’t a maintenance shop – we empower you with the knowledge and expert consultation you need to be in control of your own maintenance events – so your shop takes directives (not gives them). Whatever your maintenance needs, Savvy has a perfect plan for you: