The rules about flying with inoperative equipment are complicated, and have changed a lot. Here’s the latest.
Is your airplane squawk-free? I know mine isn’t.
At any given point in time, you’ll find a yellow Post-it Note on the instrument panel of my 1979 Cessna T310R listing all known squawks. Any time I notice a discrepancy, I jot it down so I won’t forget to deal with it next time I’m wrenching on the airplane. At the moment, there are six items on my Post-it Note list:
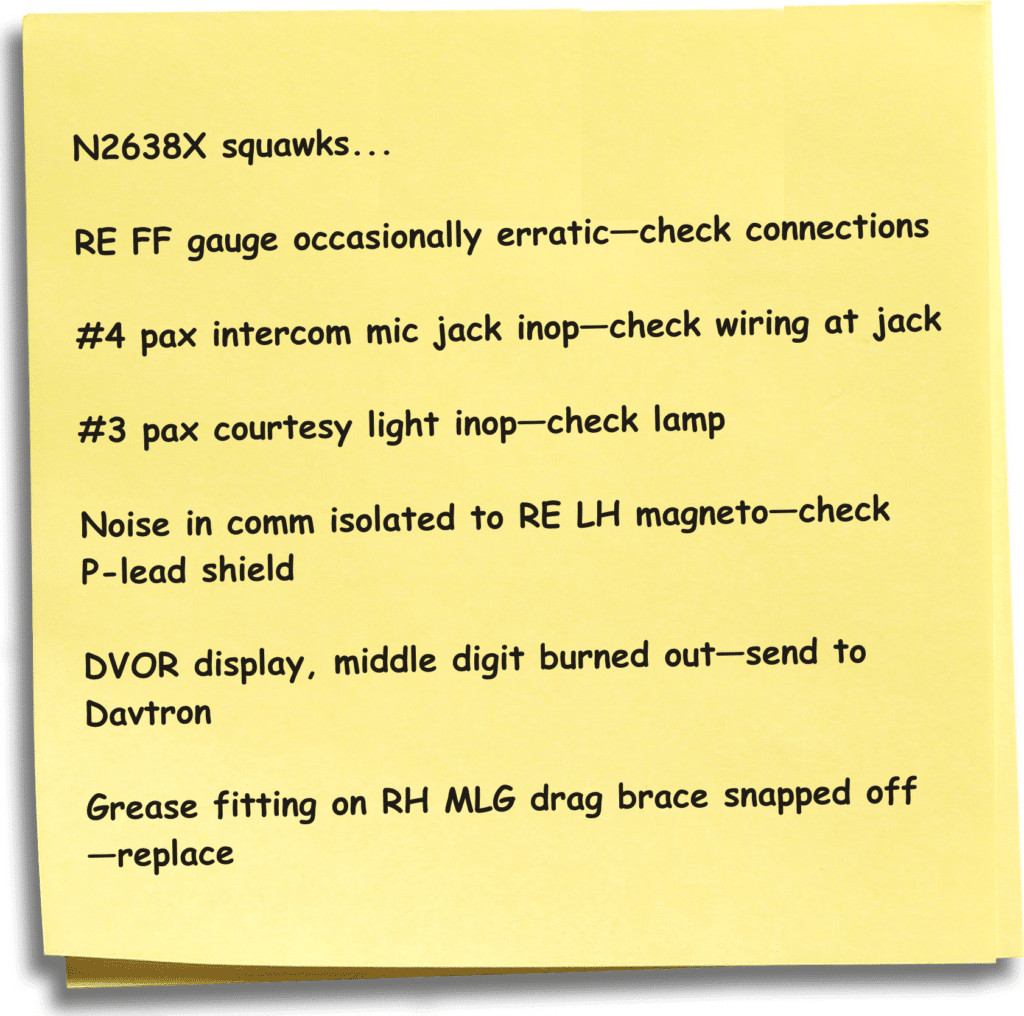
Figure 1—Inoperative items recorded on a Post-it Note.
Six known discrepancies is a lot—perhaps an all-time record for me. It reflects that fact that I’ve been busy at work and haven’t had the time to work on my airplane for a while. I should be ashamed of myself.
All these items need to be fixed, but none of them strike me as being particularly serious—certainly not ones that rise to the level of being “airworthiness items.” From time to time, however, my Post-it Note has contained more serious items such as “left vacuum pump inop” or “right alternator inop.” Those were obviously more urgent discrepancies and needed to be dealt with sooner rather than later.
Too broken to fly?
How serious does a problem need to be before it becomes an airworthiness issue and renders the aircraft “too broken to fly”?
As pilot-in-command, you have a clear regulatory responsibility to make an airworthiness determination before every flight, and indeed to reevaluate that determination continuously throughout every flight:
§ 91.7 Civil aircraft airworthiness.
(a) No person may operate a civil aircraft unless it is in an airworthy condition.
(b) The pilot in command of a civil aircraft is responsible for determining whether that aircraft is in condition for safe flight. The pilot in command shall discontinue the flight when unairworthy mechanical, electrical, or structural conditions occur.
But how are you supposed to do this? Is it legal to fly with a failed vacuum pump? A burned out nav light? A failed GPS or comm radio? An inoperative stall warning sensor? A flaky fuel flow gauge? A sticky airspeed indicator? A bad mic jack in the #4 passenger seat? How do you determine which squawks render the aircraft unflyable and which don’t?
One way is to ask your mechanic. A&Ps, and particularly IAs, have gone through extensive training in how to make such airworthiness determinations. Often, however, discrepancies are discovered outside of regularly business hours—often on weekends and holidays—when consulting a mechanic may be difficult or impossible. Also, most pilots are understandably reluctant to bother their mechanics with anything short of discrepancies that are obviously serious.
The other way is to consult the FARs.
Inoperative equipment
The rule concerning flight with inoperative equipment—§91.213—is long, complex, and not particularly easy to parse unless you have a law degree. This rule has been revised many times—it was rewritten extensively in 1989 and then revised in 2003 and again in 2004—but it’s something that every pilot and aircraft owner needs to understand. Let’s start by looking at the rule’s overall structure:
§ 91.213 Inoperative instruments and equipment.
(a) Except as provided in paragraph (d) of this section, no person may take off an aircraft with inoperative instruments or equipment installed unless the following conditions are met:
(1) An approved Minimum Equipment List exists for that aircraft.
(2) The aircraft has within it a letter of authorization, issued by the FAA Flight Standards district office having jurisdiction over the area in which the operator is located, authorizing operation of the aircraft under the Minimum Equipment List. …
[…a bunch of stuff about MELs appears here…]
(d) Except for operations conducted in accordance with paragraph (a) … of this section, a person may takeoff an aircraft in operations conducted under this part with inoperative instruments and equipment without an approved Minimum Equipment List provided—
(1) The flight operation is conducted in a—
(i) Rotorcraft, non-turbine-powered airplane, glider, lighter-than-air aircraft, powered parachute, or weight-shift-control aircraft, for which a master minimum equipment list has not been developed; or
(ii) Small rotorcraft, nonturbine-powered small airplane, glider, or lighter-than-air aircraft for which a Master Minimum Equipment List has been developed; and
(2) The inoperative instruments and equipment are not—(yadda, yadda, yadda…)
(3) The inoperative instruments and equipment are—(yadda, yadda, yadda…)
(4) A determination is made (yadda, yadda, yadda…)
(e) Notwithstanding any other provision of this section, an aircraft with inoperable instruments or equipment may be operated under a special flight permit …
Looking at this rule from 20,000 feet, it divides aircraft into three classifications:
- Aircraft that have an approved Minimum Equipment List (MEL) that define which instruments and equipment are permitted to be inoperative. [NOTE: Virtually every turbine-powered airplane and every large airplanes over 12,500 pounds maximum gross takeoff weight (MGTOW) has an approved MEL.]
- Aircraft that do not have an approved MEL, for which the rule provides a long, complex set of default guidance. [NOTE: The vast majority of small piston airplanes fall into this category.]
- Aircraft operating on a ferry permit—usually for the purpose of being flown to a location where repairs can be made. [NOTE: The ferry permit provides special exemption by the local FSDO from the airworthiness requirements of §91.7.]
Since most of us fly small, piston-powered airplanes without an FAA-approved MEL, that will be our focus for the balance of this article.
Rules for non-MEL aircraft
For non-MEL aircraft, §91.213(d)(2) tells you when you may not fly with inoperative equipment:
(2) The inoperative instruments and equipment are not—
(i) Part of the VFR-day type certification instruments and equipment prescribed in the applicable airworthiness regulations under which the aircraft was type certificated;
(ii) Indicated as required on the aircraft’s equipment list, or on the Kinds of Operations Equipment List for the kind of flight operation being conducted;
(iii) Required by §91.205 or any other rule of this part for the specific kind of flight operation being conducted; or
(iv) Required to be operational by an airworthiness directive; and
This means that before flying with an item of inoperative equipment, you have to ask four questions and get four “no” answers:
- Is the item something required for day VFR operation under the rules under which the aircraft was originally certified? (CAR 3 for most legacy aircraft, FAR Part 23 for newer designs like the Cirrus, Corvallis and Diamond.) The best way to make this determination is to look at the aircraft’s Type Certificate Data Sheet (TCDS), which can be found online at http://rgl.faa.gov (click on the “Type Certificate Data Sheets” link).
- Is the item indicated as “required” on the aircraft’s Equipment List, or on the Kinds of Operations Equipment List (KOEL) for the kind of operation being conducted? In general, legacy aircraft have an Equipment List in the POH that classifies each item of installed equipment as required, standard or optional. Anything listed as “required equipment” is a no-go item.
Part 23 aircraft usually have a POH containing a KOEL describing what equipment must be operational for various kinds of operations (e.g., day VFR, night VFR, IFR). - Is the item required by §91.205 or another applicable Part 91 rule? Recall that §91.205 is the regulation that states what minimum instruments and equipment are required for day VFR, night VFR, and IFR operations. Other applicable rules might include §91.207 (ELT), §91.209 (aircraft lighting), and §91.211 (supplemental oxygen).
- Is the item required to be operational by Airworthiness Directive? (It would be unusual for this to be the case.)
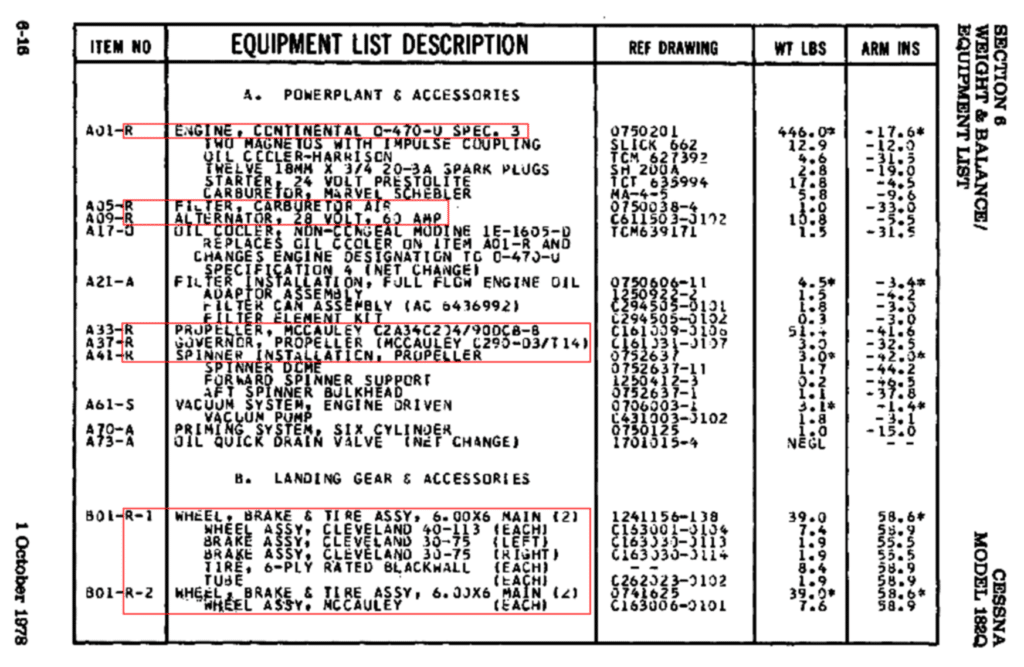
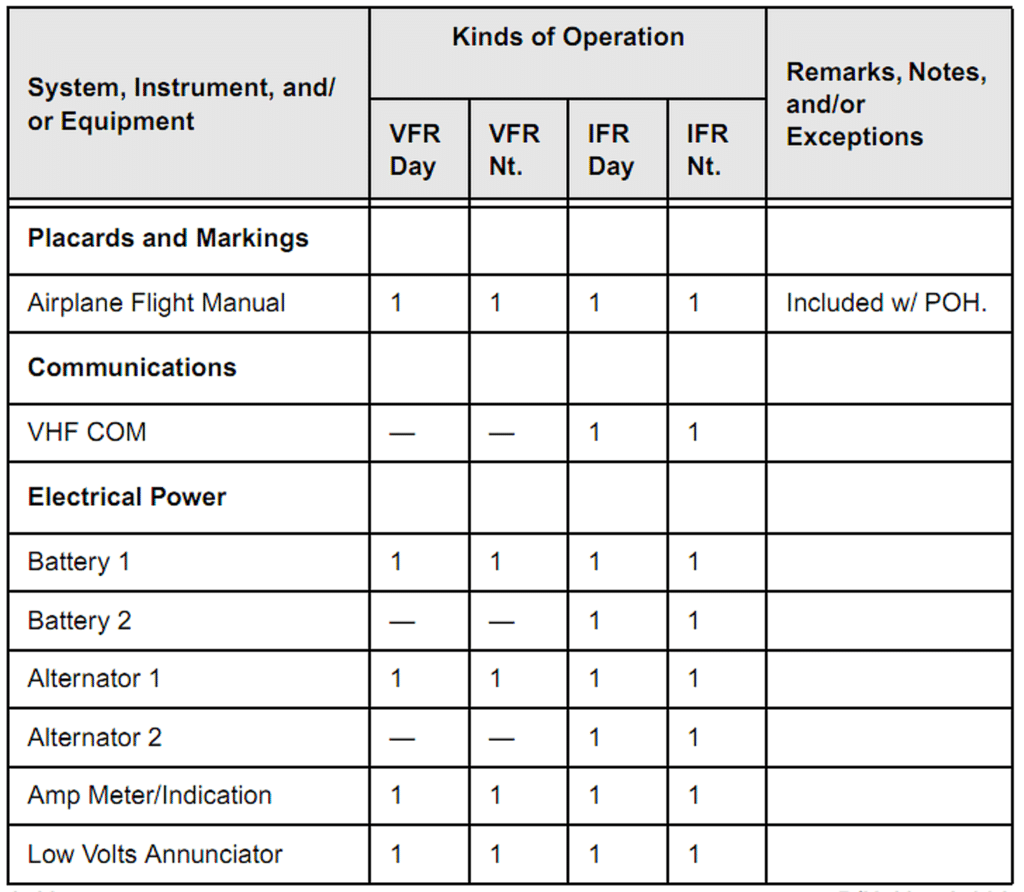
If the answer to any of these four questions is “yes” then the aircraft may not be flown until the inoperative item is repaired (unless you have a ferry permit). If the answer to all four questions is “no” then the aircraft can be flown provided that the inoperative item is either removed or deactivated, and the item or its cockpit control placarded “inoperative”:
(3) The inoperative instruments and equipment are—
(i) Removed from the aircraft, the cockpit control placarded, and the maintenance recorded in accordance with §43.9 of this chapter; or
(ii) Deactivated and placarded “Inoperative.” If deactivation of the inoperative instrument or equipment involves maintenance, it must be accomplished and recorded in accordance with part 43 of this chapter; and
IMPORTANT: This is one of the reasons I always make a record of all inoperative equipment on that yellow Post-it Note that I mentioned earlier. Not only does it remind me what needs to be fixed, but it also arguably fulfills the placard requirement of §91.213(d)(3)(ii) provided the Post-it Note is on the instrument panel in plain sight of the pilot. (A squawk sheet in the glove box does not fulfill the placard requirement.)
We’re not quite finished yet. In addition to the objective requirement for “four no’s” and the requirement to remove or deactivate the equipment and placard it “inoperative,” the rule also requires that either you or your mechanic make a subjective determination that the inoperative equipment does not constitute a safety hazard:
(4) A determination is made by a pilot, who is certificated and appropriately rated under part 61 of this chapter, or by a person, who is certificated and appropriately rated to perform maintenance on the aircraft, that the inoperative instrument or equipment does not constitute a hazard to the aircraft.
This determination does not have to be documented anywhere. But if you go flying with inoperative equipment and get in trouble as a result, then you (and perhaps your mechanic, if you consulted him) may have a bunch of explaining to do.
While it is possible for the owner of a small piston-powered aircraft to obtain a MEL, it’s a hassle to do so and is seldom warranted. For most of us, §91.213(d) provides an adequate means of dealing with inoperative equipment, and deciding whether or not our airplane is too broken to fly.
You bought a plane to fly it, not stress over maintenance.
At Savvy Aviation, we believe you shouldn’t have to navigate the complexities of aircraft maintenance alone. And you definitely shouldn’t be surprised when your shop’s invoice arrives.
Savvy Aviation isn’t a maintenance shop – we empower you with the knowledge and expert consultation you need to be in control of your own maintenance events – so your shop takes directives (not gives them). Whatever your maintenance needs, Savvy has a perfect plan for you: