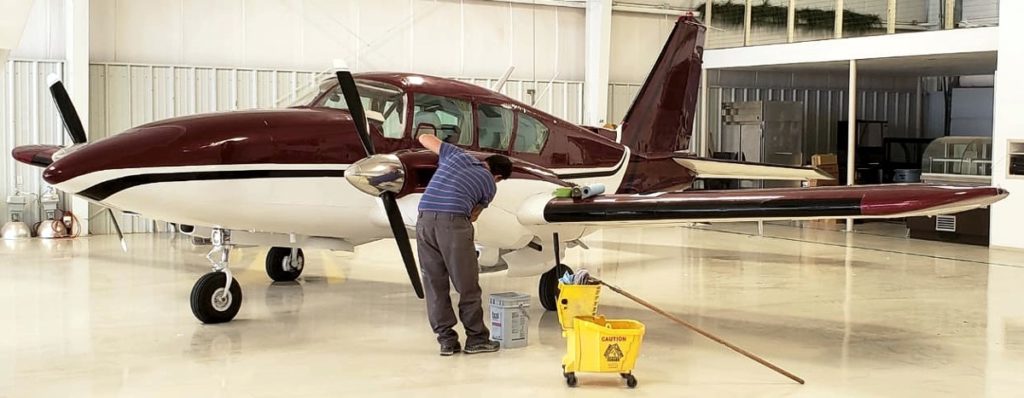
Jack is an Albuquerque-based pilot looking to purchase his first airplane. Despite his being a first-time buyer, he had his heart set on buying a piston twin. (Apparently he didn’t read Mike’s 1997 AVweb article Do You Really Want a Twin? which makes a pretty compelling case for NOT buying one.)
Jack’s research took him to Controller where he found two promising-looking candidates offered for sale by owner:
- A 1980 Cessna Turbo 310R in Georgia listed at $265,000
- A 1975 Piper Aztec E in New Mexico listed at $190,000
Jack contacted Savvy for a free preliminary logbook review of both twins. When he tried to obtain scanned maintenance logbooks, he learned that the 1980 Cessna twin had no logbooks prior to 1998. The seller claimed that his “ex-wife tossed them in the fireplace during the divorce.”
Understandably squeamish about buying a quarter-million-dollar twin with 18 years worth of missing logbooks, Jack decided to focus on the 1975 Aztec. Savvy’s Tony Barrell A&P/IA looked through the Aztec’s logbooks and, while he identified a few areas of possible concern, Tony said he didn’t see any huge red flags or show-stoppers that would preclude this aircraft from being a viable purchase candidate. Tony advised Jack that his next move would be to make an offer on the Aztec. If the seller accepted the offer, then Jack’s next step would be to arrange for an independent prebuy.
While Tony was looking over the Aztec’s logbooks and not finding anything particularly unusual there, Jack was busy scouring the Internet for information about this particular airplane.
“I found that the airplane’s tail number has been changed,” Jack told Tony. “The NTSB database indicates that an aircraft with the original tail number (and the same serial number) was in an accident in early 1979. According to the NTSB, a young pilot mismanaged the fuel system, causing both engines to quit from fuel starvation. The pilot made a forced off-airport landing, resulting in a gear collapse and substantial damage to the airplane.”
There was no mention of any of this in the Aztec’s maintenance records. There were entries made four months before the accident and five months after it, but no mention of any major airframe repairs.
“Wouldn’t such repairs need to be logged,” Jack asked Tony. “Wouldn’t an FAA Form 337 need to be there?”
“Yes, the repairs should have been logged and probably a Form 337 should have been filed, too,” said Tony, “but if the repairs weren’t logged then I imagine there’s no Form 337, either.”
“For $10, you can order a CDROM online from the FAA containing all the records that the FAA has for this aircraft, including any Form 337s that were filed,” Tony added.
Jack ordered the CDROM, which arrived two days later.
“I’m planning to go physically look at the Aztec in order to make a decision whether to spend the money to do a prebuy,” Jack told Tony. “What should I look for?”
Tony offered Jack a few suggestions:
- Look for corrosion in the airframe and landing gear
- If the engine cowlings can be removed, look for corrosion there, too
- Do a very thorough preflight as if you were going to fly the plane
- Check freedom of controls
- Sump the tanks into a jar
- If possible, start the engines and do a mag check and a brief full-power runup
If able to actually fly the airplane:
- Keep a close watch on temperatures and pressures
- Check the rigging by doing hands-off level flight
- Check all avionics including the autopilot
- Maybe do a few approaches and/or touch-and-go’s
“Hope that helps,” Tony added, “but if you need to talk about this by phone, let me know and give me a number to call.”
There was no reply. After a week with no word from Jack, Tony assumed he’d dropped the idea of buying the Aztec.
But, after 10 days of complete silence, Jack unexpectedly resurfaced and advised Tony that he’d found the missing Form 337s, hadn’t been able to see or fly the aircraft due to bad weather, and decided to proceed with a Savvy-managed prebuy on the Aztec anyway. In fact, he’d already put $5,000 in “earnest money” in escrow and obtained the seller’s consent to have the airplane flown to a prebuy shop of his choice within two hours flying time from the Aztec’s present location.
Scheduling the Prebuy
Responsibility for managing the prebuy on the Aztec fell to another member of Savvy’s team, Steve Vander Valk A&P/IA. Steve has been maintaining aircraft for almost 40 years, and was chosen for this job because of his extensive experience maintaining Piper twins.
Jack and Steve had a phone call during which Steve explained the prebuy process and discussed the pros and cons of the Aztec. Jack felt the Aztec was the perfect fit for his intended mission profile. Steve and Jack also discussed possible options for where the prebuy examination could be performed. Jack had a strong preference for doing it in Albuquerque (where he lives) so that he could look at the aircraft and perhaps even fly it.
Steve reached out to Chris Torres at Bode Aviation at Albuquerque’s Double Eagle Airport (KAEG). He sent Chris a prebuy checklist for the PA-23 Aztec and asked if Bode could squeeze Jack’s prebuy into its shop schedule and, if so, what it would cost. Chris said the shop could schedule it to start in about one week.
Jack sent Steve a bunch of photos of the Aztec he’d received from the seller.
“Nice looking Aztec,” remarked Steve after looking at the pictures. “Can the seller deliver the aircraft to Bode next week?”
“The seller wants to know if we could do it any earlier,” Jack said. “I told him he could fly the plane to KAEG this week, but that Bode can’t promise to start looking at it until next week.”
“Sellers ALWAYS want this done as fast as possible,” Steve told Jack, “but we can’t let them drive the process. I can almost guess the seller’s next push will be to ask why the prebuy can’t be completed in one day.” Steve had been involved in managing or performing hundreds of prebuys and knew the drill.
Arranging a Test Flight
Steve reached out to Chris at Bode Aviation once again: “Do you have a pilot on staff that can do a test flight before the prebuy starts? If so, what would be the charge for this? If not, can one of you techs go up with the pilot who delivers the plane?”
“We don’t have a pilot on staff who is checked out and current in an Aztec,” Chris answered. “Our best option would be to send the IA that will be in charge of the prebuy examination on a flight with the pilot who delivers the airplane. Our IA is a pilot and has many hours in Pipers, but he isn’t technically checked out in one.”
“That would work for us,” said Steve.
Jack checked with the seller, who said it would work for him as well.
Two-Phase Checklist
“I notice the prebuy checklist you sent is divided into two phases,” Chris observed. “Are we to proceed with the items on Phase 1 and then report our findings to determine if we are to continue with the Phase 2 items? Or do we plan on complying with both Phase 1 and Phase 2 no matter what?”
Savvy always performs prebuys in two phases. Phase 1 focuses on the powerplant(s) and a detailed review of the maintenance records. Phase 2 covers everything else: airframe, wheels and brakes, electrical, hydraulic, avionics, etc. We do it this way because in our experience, the Phase 1 items are the most likely to turn up deal-breakers, and we don’t want our clients wasting money on Phase 2 of the prebuy unless we’re sure that Phase 1 looks okay.
“Please complete Phase 1 and report your findings, then await our approval before proceeding with Phase 2,” Steve instructed Chris.
“Okay, sounds good,” said Chris. “I am going to estimate 8 hours of labor for each phase, so at our shop rate of $100/hour it should cost approximately $1,600 if we do both phases.”
That sounded eminently reasonable to Steve, and was approved by Jack.
Phase 1 Findings
The airplane arrived at KAEG on schedule. The IA was standing by to go up on a test flight with the delivery pilot. But the test flight didn’t happen because the pilot could not get the right engine restarted after multiple attempts. So they gave up on the test flight and put the plane in the shop.
The next day, Chris reported that the Phase 1 checklist had been completed, and send the following list of significant findings:
- Nose landing gear steering stops broken
- Both engines need fuel setups:
- Right engine set too rich, very hard to start, won’t idle
- Left engine idle set too high (1000 RPM)
- Left prop lever hitting radio knob, won’t travel full forward
- All engine controls excessively stiff (replace or pressure lube)
- EGT gauges:
- Left inaccurate
- Right inoperative
- CHT gauges:
- Left inoperative
- Right inaccurate
- Pilot seat will not slide back
- Both propellers leaking from blade roots (right worse than left)
- Right engine #1 pushrod tube oil leak
- Both engine case halves, accessory cases and oil sumps have been patched with epoxy, proseal and RTV to stop oil leaks
- Right engine case half bolt leaking
- Both cowling nose bowls burned from contact with exhaust pipes
- Right engine has significant metal in the oil filter
- Right engine exhaust heat exchanger muffler corroded
- Right engine alternator through bolts corroded
- All engine mount isolators sagging and dry-rotted
- Right engine has one odd-size harness lead and spark plug
- Boroscope examination of cylinders reveals no defects
- Right engine airbox cover cracked
- Compressions test results:
- Left engine: 1-79, 2-78, 3-71, 4-70, 5-75, 6-78
- Right engine: 1-77, 2-75, 3-75, 4-75, 5-79, 6-65
- Times (hours):
- Airframe total time 6521.8
- Time since overhaul:
- Left engine 756.1
- Right engine 1208.9
- Left prop 494.5
- Right prop 824.0
- Biennial certifications (91.411 & 91.413) three days ago
Chris also forward a collection of digital photos that were taken of some of these discrepancies These didn’t look too encouraging:
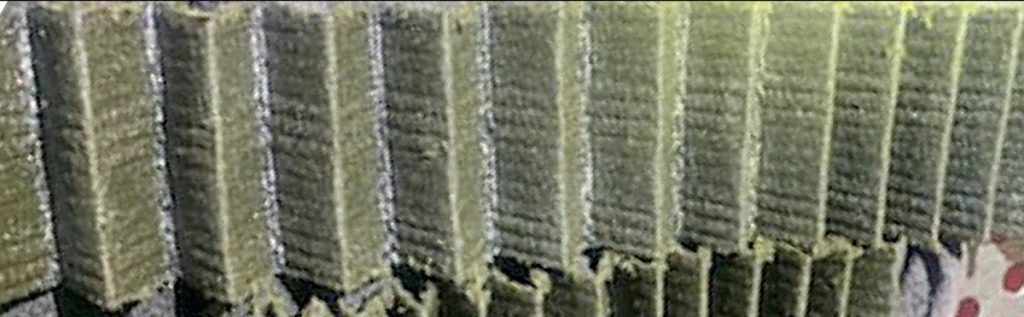
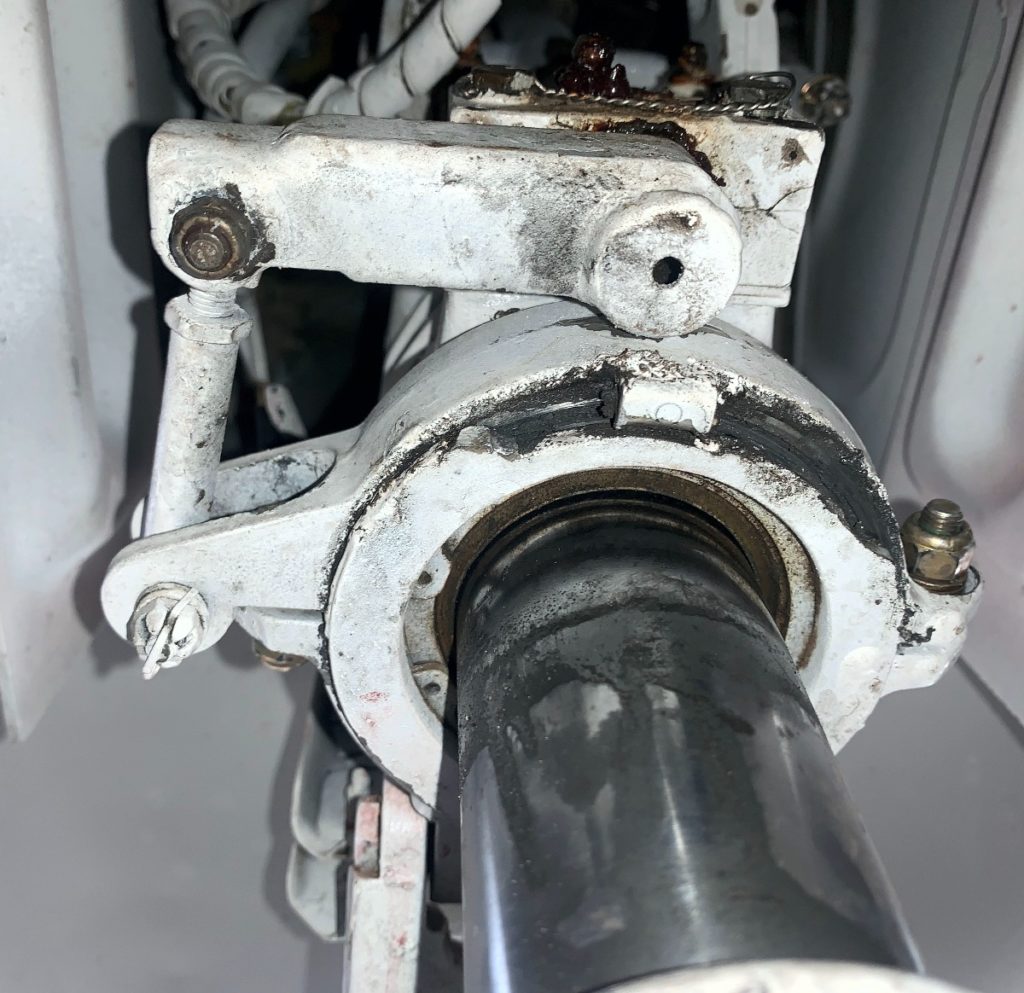
“Do you have estimates on the costs for repairs?” Steve asked Chris. “You can exclude the engine overhaul costs.”
“How accurate of an estimate for repairs would you like?” replied Chris. “We can give you a ballpark or a more precise estimate. A ballpark estimate can be done without much research. A more precise estimate can take a few hours to locate part numbers, parts, and get pricing on those parts.”
“A ballpark will be fine,” Jack said.
Within an hour, Chris came back with ballpark estimates for each identified squawk, totaling about $9,000 in parts and labor (not including the possible need to overhaul the right engine due to the metal in the oil filter). Replacing the damaged nose gear trunion would cost an additional $3,500 in parts, while repairing the existing one would cost less but take more than a month.
Instead of pulling the plug at that point, Jack decided to approve having the shop go ahead with Phase 2 of the checklist.
Pulling the Plug
A few days later, Jack says to Steve, “I was out at Bode yesterday and we have reached a point where I am pulling the plug on this prebuy. They found a significant number of rivet heads that had been sanded down, presenting structural safety-of-flight issues. I’m told that the only way we could know if those rivets are okay would be to strip the paint off the aircraft. Bode also found that the airplane has the wrong-size main gear tires (600×6 instead of 700×8). At this point, my inclination is to walk away from this airplane and find another purchase candidate.”
“That’s a good decision,” Steve said. “Pretty paint and interior, but underneath that paint is a mechanical disaster that keeps looking worse the deeper you dig. I’m sorry this one didn’t work out.”
“I am confirming that we are STOPPING the prebuy exam on the Aztec,” Jack instructed Chris. “Please put the aircraft back together and let me know when the owner can come and pick it up. Thank you.”
“Copy that,” said Chris. “We’re in the process of restoring the aircraft.”
“Thanks for the great service,” Steve told Chris. “It was a pleasure working with you and your team! Once you are completed closing the plane up please post the invoice here so Jack can get you paid.”
Unhappy Seller
“The seller is very unhappy and I can see the potential for drama,” Jack told Steve later that day. “His most recent text message to me says, ‘You played us, Jack, and I don’t appreciate that when you knew we had other prospective buyers.’ I don’t understand exactly what I would have to gain by ‘playing him’ but the potential for drama seems palpable.”
“What the seller is saying makes no sense at all,” replied Steve. “You made an offer to buy the airplane contingent upon a prebuy examination, and the seller accepted those terms. The condition of the airplane was not as it was represented to be, so you appropriately walked away from the deal. Unless the seller has another buyer who agrees to buy the airplane without doing an independent prebuy, it seems very likely that these other buyers (if they even exist) will walk away, too, once they learn the true condition of the airplane.”
Although Jack’s Aztec prebuy didn’t have a happy ending, it would have had a much unhappier ending had Jack decided to buy this airplane. Its pretty paint and interior concealed a hot mess that would unquestionably have turned into a bottomless money pit. This underscores the critical importance of having an independent prebuy examination performed by a knowledgeable and trustworthy shop that has no prior relationship with the aircraft, the seller, or (if applicable) the seller’s broker. Steve steered Jack to an outstanding shop located in his hometown that did an outstanding job on the prebuy at a very reasonable cost.
Working with Savvy, Jack will find a better purchase candidate that will be safe, reliable, and won’t wind up sending him to the poorhouse. In fact, Jack has already asked Savvy to perform a preliminary logbook review of another Aztec. Jack may have lost this first battle, but we’ll make sure he winds up winning the war, and that will be a happy ending indeed.
If you’re thinking about buying an aircraft, perhaps you should be talking to Savvy. You can start off by requesting a no-cost preliminary logbook review and see where that leads.
You bought a plane to fly it, not stress over maintenance.
At Savvy Aviation, we believe you shouldn’t have to navigate the complexities of aircraft maintenance alone. And you definitely shouldn’t be surprised when your shop’s invoice arrives.
Savvy Aviation isn’t a maintenance shop – we empower you with the knowledge and expert consultation you need to be in control of your own maintenance events – so your shop takes directives (not gives them). Whatever your maintenance needs, Savvy has a perfect plan for you: