The best maintenance shops often warrant the closest owner oversight.
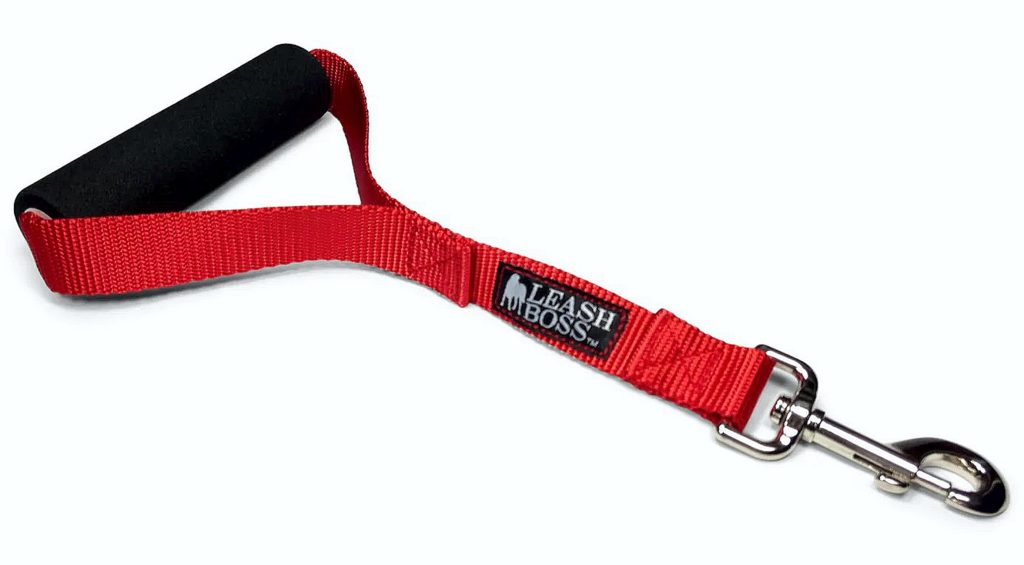
I’m frequently asked by aircraft owners to recommend good maintenance shops in a particular area, and my company maintains a large database of maintenance resources to facilitate such referrals. Our team of more than 20 A&P/IA account managers keep close track of their experiences working with hundreds of shops, and we do our best to steer our clients to the ones with which we’ve had the best outcomes and—perhaps more importantly—away from those that were not so good.
Often I find myself telling a client, “this is an outstanding shop that does thorough inspections and excellent work, but be prepared for a big bill unless you keep them on a short leash.” I do not mean this as a criticism of the shop. It simply reflects the reality that the best shops tend to do very thorough inspections and uncompromisingly meticulous repairs, and generally tend to have a perfectionist approach to maintenance. These are exactly the attributes we want the shop to have, but the result can be serious sticker shock unless the owner actively throttles the shop back by explicitly directing them to perform only the work desired nothing more.
Case in Point
Consider the annual inspection we managed awhile back for the owner of a 2006 Cirrus SR22. The shop involved was a Cirrus Authorized Service Center we’d worked with before and liked a lot. Per our normal practice, we instructed the shop to do the inspection but to perform no repairs and to order no parts until it had written up its detailed discrepancy list and repair recommendations and cost estimates and provided it to us to review with the owner.
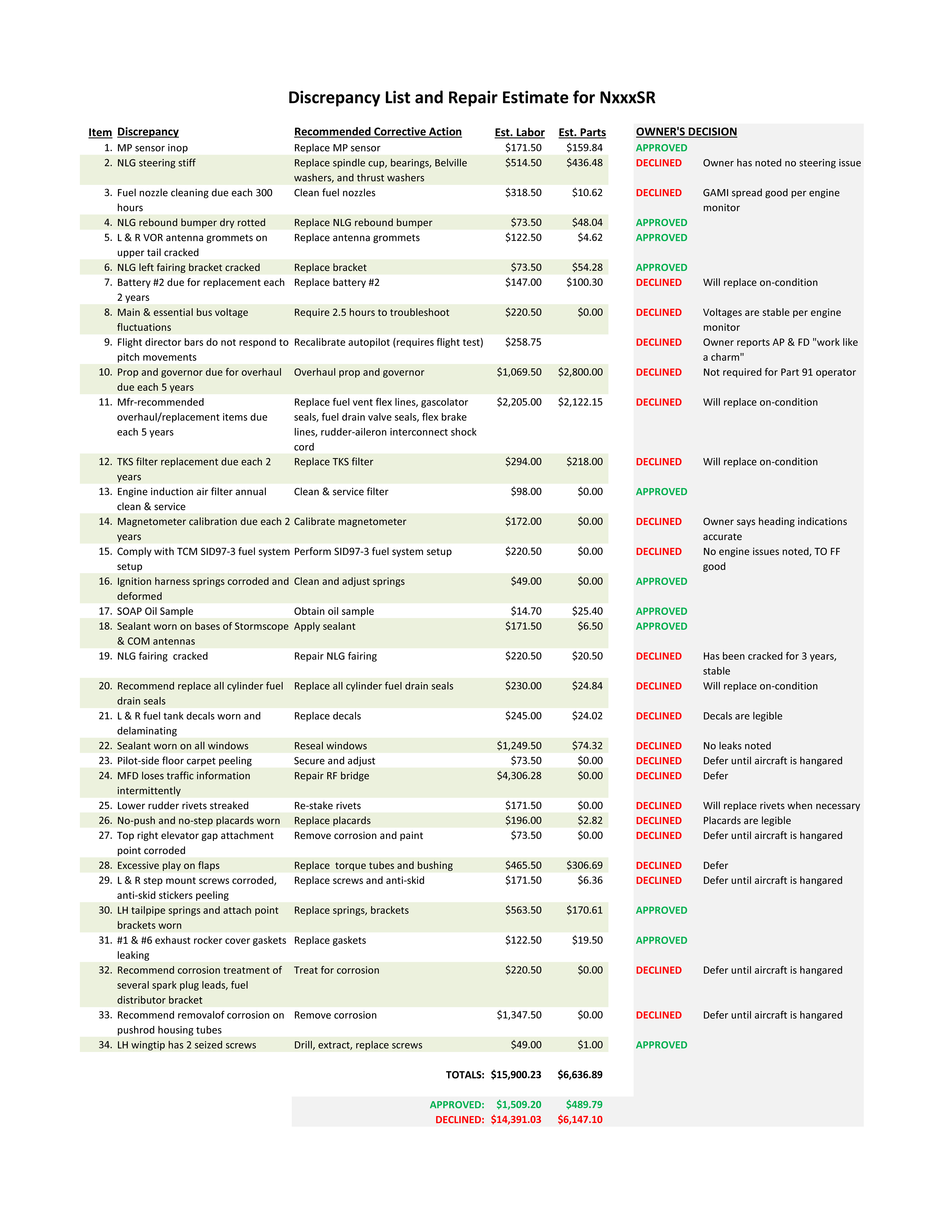
The shop completed its inspection and provided a 34-item discrepancy list (see facing page), with recommended corrective actions for each discrepancy plus estimated cost of labor and parts for each one. The cost estimates totaled roughly $22,500—and this would have been on top of the $2,500 flat-rate charge for the inspection. Had the owner not intervened, the shop would have presented him with an invoice for 25 grand. Happily, that did not happen.
Why Are We Doing THis?
We went over the shop’s discrepancy list and repair estimates with the owner line by line, offering him suggestions as to which items really ought to be repaired and which could be prudently declined or deferred. Generally, we encouraged the owner to approve those items that clearly needed to be done and/or that were inexpensive to do, and to decline or defer work that was not demonstrably necessary (particularly if it was costly).
For instance, the shop wrote up a substantial number of costly maintenance items not because any actual discrepancy was found, but rather because the items were “due” according to the maintenance manual. The word “due” is one of the most expensive words in the world of aircraft maintenance. Part 91 (non-commercial) operators are never required to perform maintenance just because the manufacturer says it’s due (unless it’s something mandated by an Airworthiness Directive or Airworthiness Limitation). We almost always recommend that such work be performed strictly on-condition rather than on the fixed timetable provided by the manufacturer. If something is working fine but the book says it’s “due” for replacement or overhaul, we usually suggest telling the shop “no thanks.”
The Cirrus Service Center cited the propeller and governor were “due” for five-year overhaul costing nearly $4,000. Additional five-year replacement items—fuel vent lines, gascolator seals, fuel drain valve seals, brake lines, rudder-aileron interconnect shock cord—would add another $4,300 to the tab. Other “due” items included two-year replacement of the #2 battery, cleaning of fuel injection nozzles each 300 hours, annual fuel injection system adjustment, and two-year magnetometer calibration. The owner wisely chose to decline all these items.
The shop also wrote up a number of discrepancies on items that the owner swore were working just fine. The shop claimed the nose steering was stiff, but the owner said the plane had no steering issues. The shop claimed that voltage was fluctuating on the main and essential electrical buses, but the voltages looked stable when we reviewed recent engine monitor data. The shop said “flight director bars do not respond to pitch movements” but the owner said the flight director and autopilot had been “working like a charm.” The owner declined all these items, too.
Then there were several legitimate discrepancies that did not rise to the level of airworthiness concerns and that the owner chose to defer. The shop reported the nose gear fairing was cracked and proposed to repair it, but the owner said it had been cracked for the past three years and the crack was stable and not growing. The shop wrote up a number of corrosion-related discrepancies, but the owner decided to defer dealing with them until he was able to secure a hangar for the airplane. Those struck us as being reasonable judgment calls for the owner to make.
Short Leash
By the time we finished going over the discrepancy list with the owner, he’d decided to approve 11 of the 34 repairs recommended by the shop, and to decline or defer the remaining 23 items. The estimated cost to repair those 11 items came to about $2,000, while the estimated cost of the 23 declined items would have been north of $20,000. A short leash indeed!
Some readers might jump to the conclusion that this shop was overpriced and/or trying to take advantage of the owner, but I would strongly disagree. We love working with shops like this one that do thorough inspections and provide detailed discrepancy lists and repair estimates. As a Cirrus Authorized Service Center, the shop was obligated to write up all the “due” items in accordance with manufacturer’s guidance, and to perform all those manufacturer-recommended tasks unless the owner instructed them not to. To its credit, the shop did not complain when we advised them that the owner had approved 11 items and declined 23 others. They did the work the owner wanted done, refrained from doing the work that he didn’t, and presented an invoice with no surprises. That’s exactly the way things are supposed to work.
Is this a typical case? Well, yes and no. In my experience, when dealing with shops like this one whose annual inspections are thorough, it is common for one-half to two-thirds of the listed discrepancies to be items that can be prudently declined or deferred at the owner’s option. On the other hand, it’s a bit unusual for the declined items to represent 90% of the total estimated cost—that happened here because an extraordinary number of costly five-year items “came due” all at once.
At annual inspection time, it’s your shop’s job to find and document every discrepancy they can, and to write up every maintenance task the manual calls for. Then it’s your job to go over the list and decide which items to approve and which to decline. To keep your IA smiling, avoid saying “no” to anything that’s a genuine airworthiness issue or that’s required by regulation (such as complying with an Airworthiness Directive or Airworthiness Limitation).
You bought a plane to fly it, not stress over maintenance.
At Savvy Aviation, we believe you shouldn’t have to navigate the complexities of aircraft maintenance alone. And you definitely shouldn’t be surprised when your shop’s invoice arrives.
Savvy Aviation isn’t a maintenance shop – we empower you with the knowledge and expert consultation you need to be in control of your own maintenance events – so your shop takes directives (not gives them). Whatever your maintenance needs, Savvy has a perfect plan for you: