It has been a lot like watching paint dry
I recently completed work on my second book, a 500-page monster titled Mike Busch on Engines (available on Amazon). It was a yearlong effort that involved reviewing hundreds of my past articles about piston aircraft engines, deciding which were still relevant, organizing them into a coherent series of sections and chapters, and bringing it all up-to-date. In the process, I couldn’t help but reflect on what has changed in the 50 years since I bought my first airplane…and what has stayed the same.
For the most part, the engines themselves haven’t changed much. The Continental TSIO-550-K that powers the new-production Cirrus SR22T is not much different from the Continental TSIO-520-BBs that power my 1979 Cessna Turbo 310, and those are both close second cousins to the Continental O-470-R that powered my first airplane, a 1968 Cessna 182 Skylane. The Lycoming IO-360-M1A that powers the new-production Diamond DA40 XLS is nearly indistinguishable from the Lycoming IO-360-A1B6 in the 1971 Cessna 177RG Cardinal owned by my editor Colleen Keller.
The Continental O-470, TSIO-520 and TSIO-550 type certificates were issued in 1952, 1956, and 1980 respectively. The Lycoming IO-360 was certified in 1960 as a fuel-injected variant of the carbureted O-360 certified in 1955. It’s hard not to wonder why these Jurassic engines are still being manufactured and installed in new-production aircraft, instead of basking proudly in some aviation museum next to the Curtis OX-5, Le Rhône rotary, Warner-Scarab, and Wright Whirlwind.
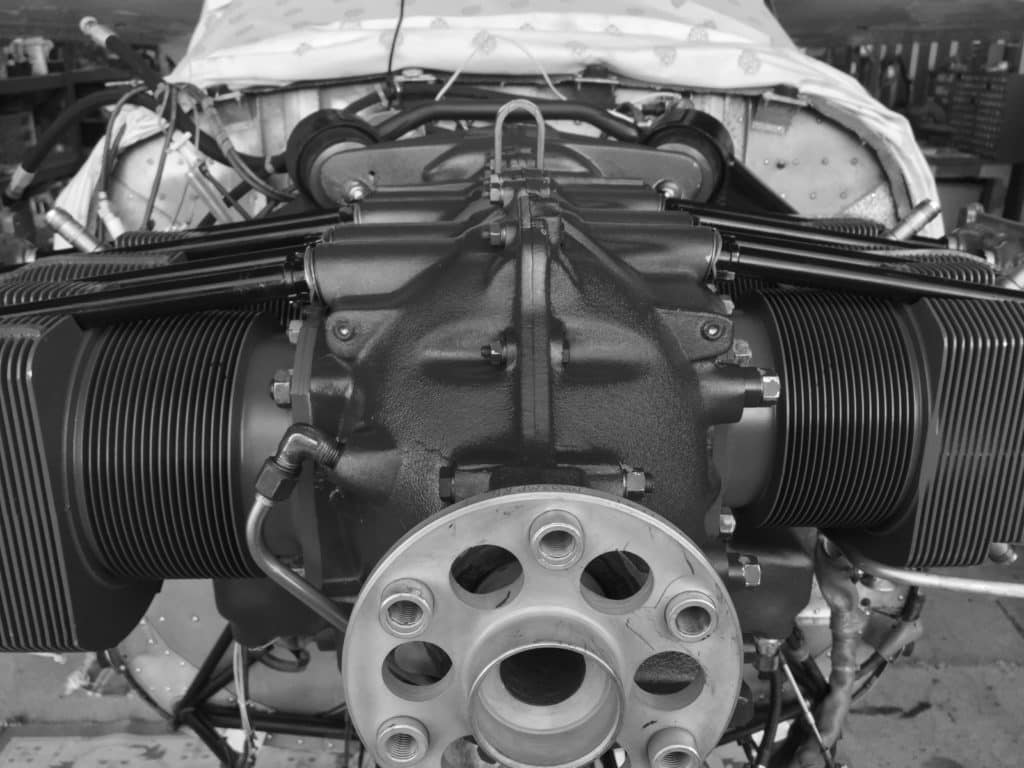
The reason, of course, is that the cost and effort involved in certifying a new aircraft engine design is so daunting that only companies with seriously deep pockets can consider it. Even among those deep-pocket companies, the track record for innovation is dismal.
Does anyone remember the Continental 6-285 “Tiara” engine that was certified in 1969? It was a novel, highly innovative, clean-sheet piston engine design that cost Continental millions to develop and certify, but it turned out to be a disastrous commercial flop that wound up powering a handful of Piper Pawnee ag-planes and then quietly faded into obscurity. Then in 1986, the company spent hundreds of thousands to certify a liquid-cooled TSIOL-520 “Voyager” engine that was also a resounding commercial failure.
In the mid-1990s, Lycoming certified an IO-580 engine at the request of Cessna, who were looking for a more modern engine for their “restart” Cessna 206 Skywagon. However, Cessna encountered so many cylinder problems with this engine that—rather than delay production—they decided to go with the tried-and-true IO-540 engine (certified in 1960) instead. A handful of IO-580s found their way onto some aerobatic aircraft, after which the engine was relegated to the scrap heap of history.
Retarded ignition
What amazes me even more is that our engines still use fixed-timed magneto ignition systems. This technology was introduced in automotive engines in 1897 by Robert Bosch (this was before cars had an electrical system) and gained popularity in aviation during the 1920s and 1930s (before airplanes had them). The four big Continental/Bendix S-1200 mags on my Cessna 310 are nearly identical to the ones produced by the Bendix/Scintilla factory in 1935.
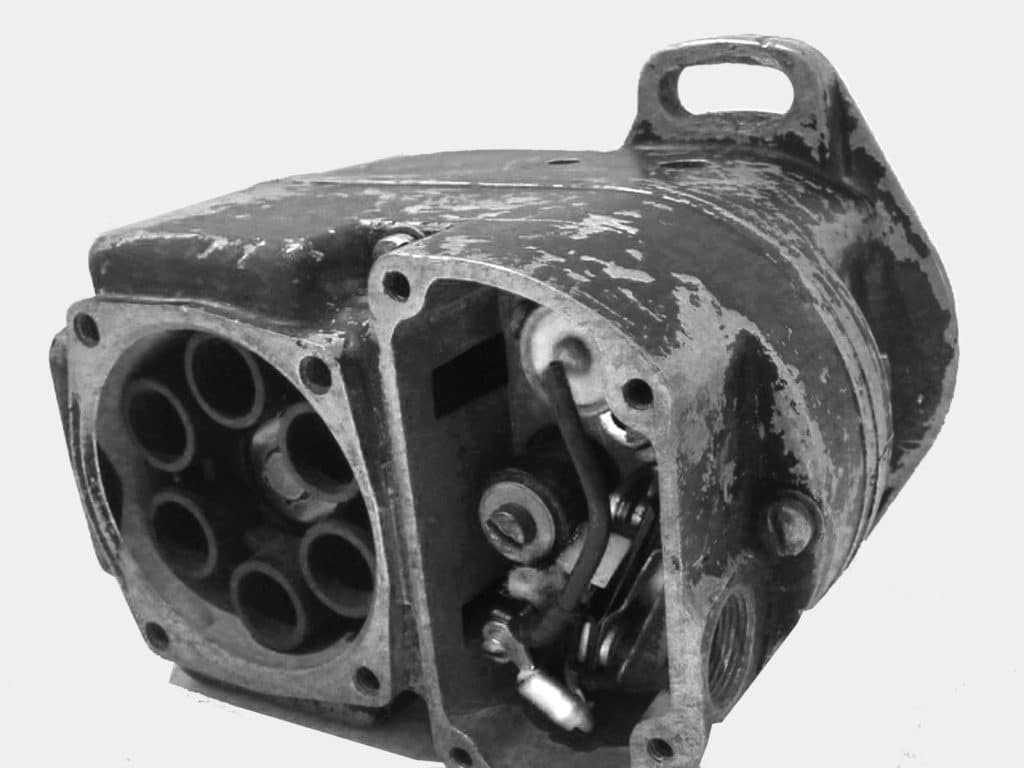
The first electronic ignition system (EIS) was developed by Delco-Remy in 1948 and was offered by Pontiac in 1963. Fully solid-state EIS with microprocessor-controlled variable timing became the norm in automobiles during the 1990s. Aviation EIS from E-MAG and Light Speed Engineering have been de rigueur on kitplanes and LSAs for the past decade. Yet almost all of today’s certified new-production all-electric GA airplanes with their fully redundant electrical systems are still being delivered with old-fashioned fixed-timed “tractor mags” on their engines. Why?
Electroair began working with the FAA in early 2009 to obtain STC approval of its EIS. It took the company more than two years of work before the FAA approved the EIS on four-cylinder Continental and Lycoming engines in mid-2011, and nearly three more years to gain approval for six-cylinder engines in early 2014. Even after this five-year effort, the FAA would only approve replacing one magneto with the Electroair EIS; the other “tractor mag” must be retained even though it’s demonstrably far less reliable. Lots of dual Electroair installations are flying in homebuilts with great success, but for certified aircraft the FAA remains a significant obstacle to innovation.
The promise of full-authority digital engine control (FADEC) systems for piston aircraft engines—the subject of heavy investment by both Continental Lycoming in the late 1990s—has gone almost nowhere. Lycoming’s EPIC system, developed in partnership with Unison, never made it into production. Continental acquired the FADEC system developed by Aerosance and succeeded in getting it certified for both Continental and Lycoming engines, but only a tiny handful of these “PowerLink” systems have been delivered (most of them on Liberty XL2 trainers) and by any measure the program has been an abject commercial failure. (Do you detect a pattern here?)
Outside the box
A notable exception involves an obscure Austrian subsidiary of a Canadian company mostly known for its two-stroke snowmobile, motorbike and ATV engines that quietly redefined the small (under 150hp) four-stroke piston aircraft engine. Few noticed until 2004 when the FAA approved the LSA rule, and sexy factory-built Special Light Sport Aircraft started showing up at Oshkosh, Lakeland and Sebring. Almost all were powered by Rotax 912-series engines.
The Rotax 912 story began in 1989, when the first 80 hp engines were shipped to customers in Europe for use on ultralights and motorgliders. Rotax already dominated those markets with its two-stroke engines derived from their snowmobile engines. But almost nobody outside the ultralight community took notice, especially since the 912 had a ridiculously short 600-hour TBO. Yet Rotax pressed forward, and in 1994 obtained FAA certification of the 80 hp engine. A 115 hp turbocharged version (the 914), a 100 hp ultralight version (the 912ULS), and a certified 100 hp version (912S) followed in quick succession. TBO was increased to 1,000 hours, then 1,200 hours, then 1,500 hours. These engines started selling like hotcakes abroad, but never gained much traction in the U.S. until the FAA adopted the LSA rule in 2004 and factory-built S-LSAs became all the rage.
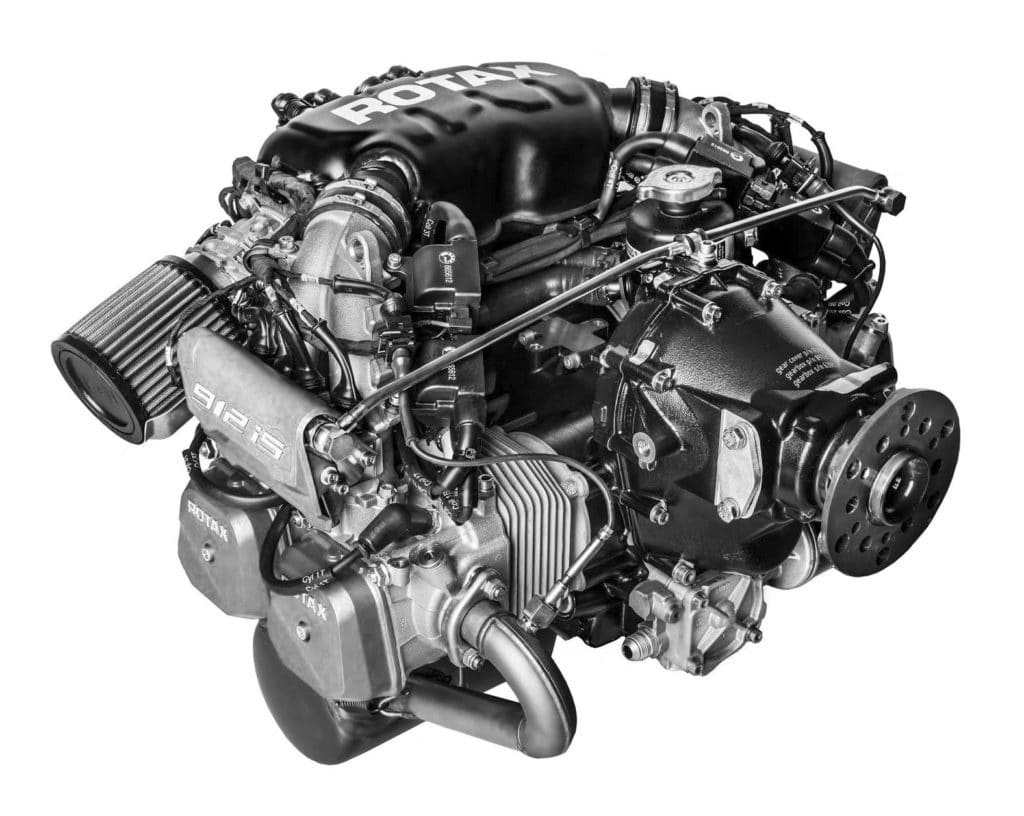
Designers of S-LSAs overwhelmingly chose the Rotax 912 because it was substantially lighter, more compact and more efficient than traditional 100 hp engines like the Continental O-200 and the Lycoming O-235. The Rotax design is lightyears ahead of these competitors. It uses much smaller cylinders turning much higher revs, something made possible by an integral reduction gearbox. The cylinder heads are liquid cooled, the ignition system is electronic, and the engine is designed to run on unleaded mogas instead of 100LL. What’s not to like?
By 2009, the TBO of both the 912 and 914 engines was increased to 2,000 hours, and I’m told they usually look pristine inside when torn down at that point. In 2012, the fuel-injected FADEC-controlled 912iS started shipping. By 2014, Rotax had shipped 50,000 of these engines. As I write this, the latest version of this engine is the 135 hp turbocharged 915iS. (I sure wish Rotax would come up with a 300 hp engine!)
Squeezebangs
There are other new engine designs emerging. To me, the most exciting are compression ignition (diesel) engines designed to run on Jet A.
Cessna made a huge splash in 2013 when it announced a new version of the venerable Cessna 182—dubbed the Skylane JT-A—with a French-built SMA turbodiesel engine. Both Cessna and SMA made major investments in the development and certification of this aircraft, but just as first customer deliveries were scheduled to begin Cessna suddenly pulled the plug on the Skylane JT-A. Cessna never fully explained the reason behind its decision, although we do know that one of their flight test aircraft suffered an in-flight turbocharger failure and made a successful off-airport landing. Whatever the reason for the program cancellation, I found it to be a huge disappointment; the Skylane JT-A would have been a big step forward in putting diesel-powered GA airplanes on the map.
In Germany, Thielert Aircraft Engines GmbH developed a “Centurion” line of aircraft engines that borrowed heavily from automotive diesels from Mercedes-Benz. Despite being certified, the engines proved to have serious issues with reduction gearbox longevity. Then Thielert became insolvent, and China’s AVIC acquired the rights to these engines. They were resurrected via AVIC’s German subsidiary Technify Motors GmbH, who apparently resolved the gearbox issues. The engines are now being marketed through Continental Motors Group (also owned by AVIC).
The Continental/Technify 135 hp CD-135 and 155 hp CD-155 four-cylinder turbodiesel engines are STC’d for the Cessna 172 Skyhawk, the Diamond DA40 Star and DA42 Twin Star, and the Piper PA28-161 Warrior and PA-28-181 Archer. In 2014, Piper started shipping the new-production Archer DX powered by a CD-155 diesel, and in April 2018 the company announced it would produce a twin-engine Seminole DX powered by a pair of 170 hp CD-170 diesels.
Then Cessna did it again: In May 2018, the company announced it had decided to scrap the 172 Skyhawk JT-A powered by the Continental CD-155—another disappointing setback for mass-market diesel GA.
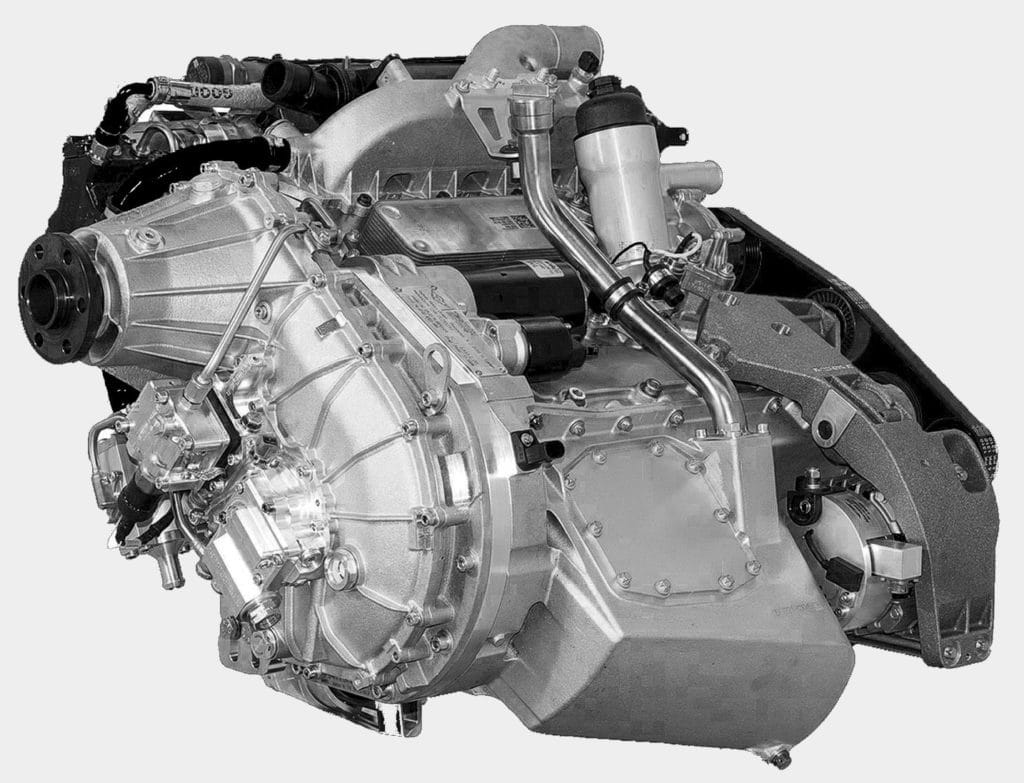
Diamond Aircraft Industries was an early adopter of the Thielert diesels in its DA42 Twin Star. When Thielert went belly up, Diamond suspended production of the DA42 for about a year, and owners of these now-unsupported engines were in a world of hurt. Diamond restarted DA42 production in 2009 using a 168 hp AE 300 diesel engine built by its own Austro Engine subsidiary in Austria.
Meanwhile, two small Wisconsin startup firms—DeltaHawk Engines, Inc. and Engineered Propulsion Systems, Inc.—are working hard to achieve FAA certification of two very different clean-sheet diesel aircraft engines. The DeltaHawk DH180 is a lightweight compact 180 hp two-stroke turbodiesel, while the EPS Graflight V-8 is a 350 hp brute aimed at high-performance singles and twins.
It’s still too early to tell whether any of these aviation diesels will reach critical mass sufficient to be commercially successful. I’ve got my fingers and toes crossed for the early adopters of these engines, because I see diesels as the best hope for the future of piston GA.
Lean and healthy
Although most of us are still flying behind engines designed in the 1950s with ignition systems designed in the 1930s, the way we operate these powerplants has changed for the better. Most of the credit for this goes to my colleague George Braly, who for the past 20 years has presided as Archbishop of the Church of Lean-of-Peak. While George has been busy preaching the gospel of LOP, I’ve been on my own crusade to bring the benefits of reliability-centered maintenance (RCM) to the piston GA community. Both George and I have faced uphill battles, but we’re finally seeing real progress in how pilots and aircraft owners are operating and maintaining their piston powerplants. More about LOP and RCM in future columns.
You bought a plane to fly it, not stress over maintenance.
At Savvy Aviation, we believe you shouldn’t have to navigate the complexities of aircraft maintenance alone. And you definitely shouldn’t be surprised when your shop’s invoice arrives.
Savvy Aviation isn’t a maintenance shop – we empower you with the knowledge and expert consultation you need to be in control of your own maintenance events – so your shop takes directives (not gives them). Whatever your maintenance needs, Savvy has a perfect plan for you: