Last month, we examined the principles of RCM used by the airlines and military to achieve cost-effective maintenance. Now, let’s explore how RCM can be applied to our small GA aircraft, and especially to our piston aircraft engines.
For three decades, the airlines and military have been using Reliability-Centered Maintenance to slash maintenance cost and improve reliability. Most of these benefits have come from replacing fixed overhaul intervals with on-condition maintenance.
Unfortunately, RCM has not trickled down to the low end of the aviation food chain. Maintenance of piston GA aircraft remains largely time-directed rather than condition-directed. Most GA owners dutifully overhaul their engine at TBO, overhaul their prop every 5 to 7 years, and replace their alternators and vacuum pumps every 500 hours, just as Lycoming, TCM, Hartzell, McCauley, Kelly Aerospace and Parker-Hannifin recommend. Bonanza owners have their wing bolts pulled every 5 years. Cirrus owners replace their batteries every 2 years. And the beat goes on…
Does any of this make sense?
After analyzing reams of operational data from a number of major air carriers, RCM researchers concluded that fixed-interval overhaul or replacement rarely improves safety or reliability, and often makes things worse.
When does TBO make sense?
For fixed TBO to make sense, the component must have a failure pattern that looks like pattern B in Figure 1, where the component can be expected to operate reliability for some predictable useful life, beyond which the probability of failure starts to increase rapidly to unacceptable levels.
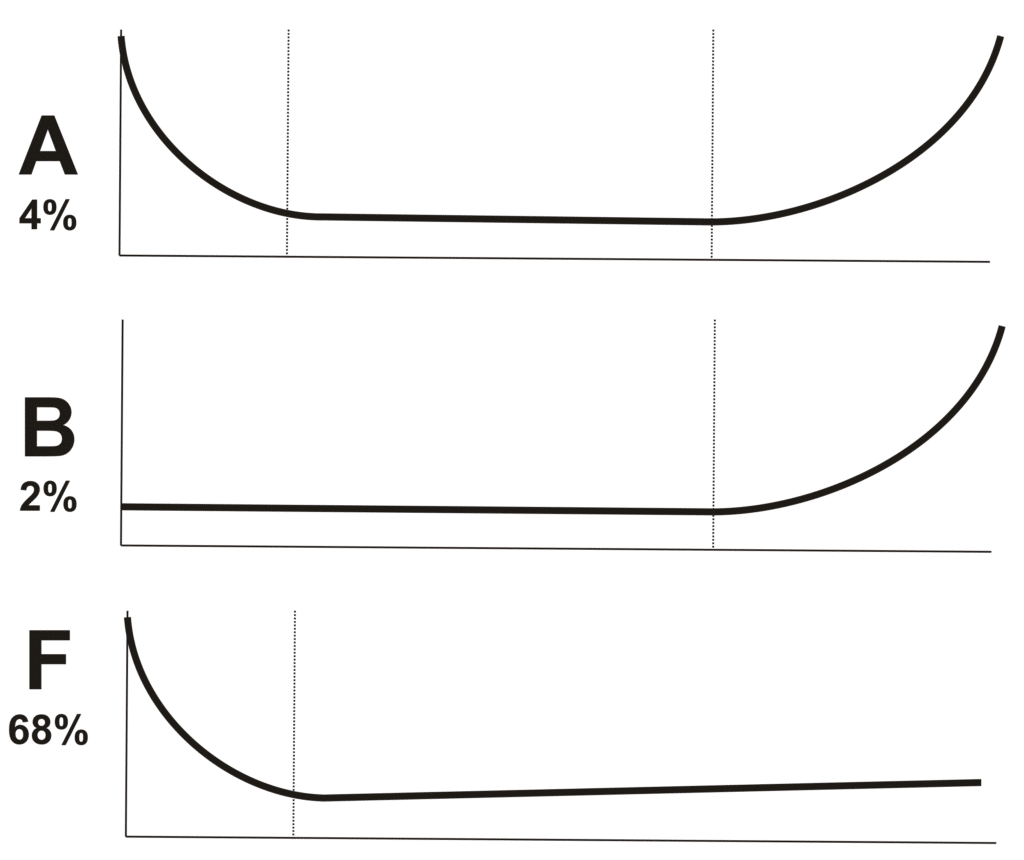
But piston aircraft engines don’t exhibit this kind of failure pattern. We know these engines suffer the highest risk of catastrophic failure not when they pass TBO, but rather when they’re fresh out of the factory or field overhaul shop. Look at the NTSB data for the five-year period 2001 through 2005 (Figure 2).
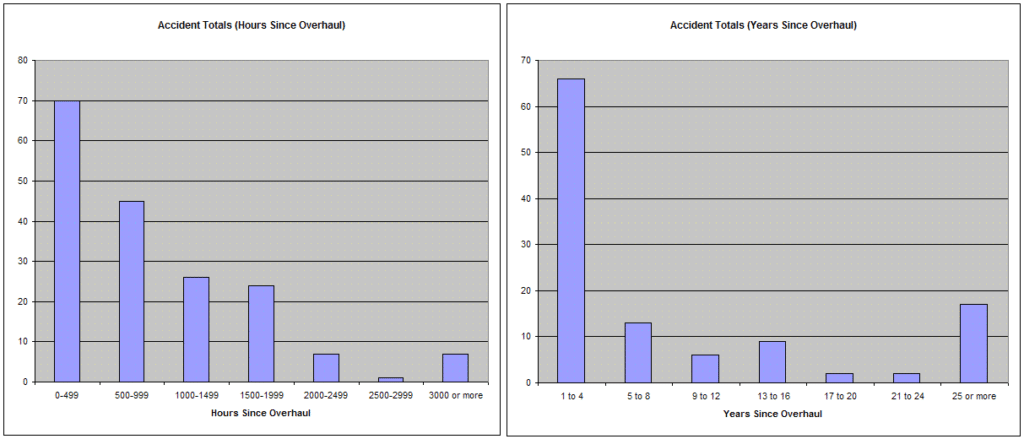
This NTSB data can’t tell us much about the risk of engine failure beyond TBO, because most engines are voluntarily euthanized at TBO. What it does show clearly is that engines fail with disturbing frequency during their first few years and few hundred hours in service after manufacture, rebuild or overhaul. Obviously, our engines have a failure pattern more like A or F in Figure 1, with a high risk of “infant mortality” failure.
Would you be comfortable taking your family up in a piston-powered GA airplane with an engine at 5 hours SMOH? At night? Over rough terrain or water? In IMC? How about at 10 hours SMOH? Or 25 hours SMOH? (These are not easy questions.)
If our engines have a failure pattern like A (“bathtub curve”), then overhauling at a fixed TBO becomes a two-edged sword. On one hand, it keeps us out of the presumptive wear-out zone. On the other hand, it puts us right back inside the infant mortality window where the data shows clearly that engine failure is disturbingly common.
If our piston engines have a failure pattern like F (as turbine engines do), then overhauling at a fixed TBO makes no sense at all, because there’s no obvious wear-out zone. That’s why the airlines and military overhaul turbine engines strictly on-condition. (There’s very little data suggesting that piston engines have an obvious wear-out zone, either.)
Tough Sell
Because we have so little data about piston aircraft engines operated beyond TBO, it can be difficult to persuade mechanics and regulators to adopt on-condition maintenance where fixed TBO has been the norm. We can’t collect engine failure data unless there are engine failures, and aircraft engine failures are considered unacceptable because they can cause injury and death. So the maintenance program for an aircraft engine must be designed without the benefit of data about failures which the program is meant to avoid. RCM researchers call this “The Resnikoff Conundrum.”
(If you’ll permit me a brief detour: The FAA’s decades-long opposition to rescinding “the age 60 rule” for airline pilots is a perfect example of The Resnikoff Conundrum. Experts in aviation medicine long agreed that was absolutely no scientific basis for the FAA’s venerable policy of forcing airline pilots to retire at age of 60. The FAA’s longstanding argument was that it has no safety data showing that allowing airline pilots to continue flying beyond age 60 is safe. Well, duh! It took nearly five decades for the FAA to raise the age limit from 60 to 65…and there’s still an age limit that has no scientific basis. Isn’t it high time that ATPs were retired on-condition?)
We do know that fixed-interval overhaul is counterproductive for turbine engines, because the airlines and military started phasing out such fixed-interval overhauls in favor of on-condition maintenance decades ago (and saved gazillions of dollars by doing so). We have tons of data about high-time turbine engines, and that data makes it crystal clear that fixed-interval overhaul hurts reliability more than it helps—not to mention that it increases maintenance cost and downtime. I firmly believe that the same is true for piston aircraft engines, but sadly I don’t have enough failure data on past-TBO engines to prove it beyond a reasonable doubt.
Is this the right question?
Do we really care whether a piston engine has failure curve A or F? Perhaps not. A piston engine isn’t a single component with a single dominant failure mode and a well-defined failure pattern.
Engine failures occur for lots of reasons. A piston engine is a complex system made up of hundreds of components—crankcase, crankshaft, camshaft, connecting rods, pistons, piston rings, cylinder barrels, cylinder heads, valves, valve guides, rocker arms, pushrods, gears, bearings, through-bolts, magnetos, spark plugs, etc.—each of which has its own unique failure modes and patterns. An engine failure can be caused by the failure of any of these parts, and each part has distinctively different failure characteristics.
To gain insight into how, when, and how often piston engines fail—and how best to prevent those failures—we need to analyze the failure modes and patterns of each of the engine’s critical component parts, rather than try to lump them all into a single failure pattern for the engine as a whole.
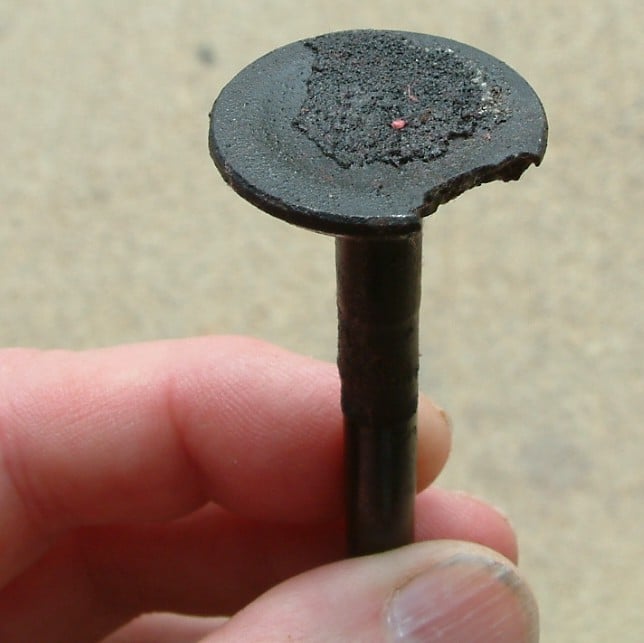
Consider exhaust valves, for example. We know from experience that they often don’t survive to TBO. When they begin to fail, we’re often able to catch the potential failure at before complete functional failure occurs (i.e., a “swallowed valve”) by means of an annual compression test or borescope inspection. If the aircraft is equipped with a digital engine monitor and if the pilot knows how to interpret it, the pilot can detect a potential exhaust valve failure before the valve fails completely. But if the valve fails in-flight, it’s usually a mayday situation.
Does this mean that we should reduce engine TBO to something less than typical exhaust valve life? Should we be overhauling our engines every 500 or 1,000 hours to prevent exhaust valve failures? Of course not!
Why not? Because repairing a leaky exhaust valve can be done without an engine teardown; it only involves pulling the cylinder. We’ve got excellent tools (like borescopes and digital engine monitors) that let us detect potential valve failures before complete failure occurs—provided those tools are used properly and regularly. (And unfortunately, they aren’t in the vast majority of cases because most A&Ps have no training in borescopy, and most owners have no training in engine monitor data interpretation.)
So next month, we will examine the critical components of a piston aircraft engine, how they fail, what the consequences of those failures have on engine operation and safety of flight, and what sort of maintenance actions we can take to deal with those failures effectively and cost-efficiently.
You bought a plane to fly it, not stress over maintenance.
At Savvy Aviation, we believe you shouldn’t have to navigate the complexities of aircraft maintenance alone. And you definitely shouldn’t be surprised when your shop’s invoice arrives.
Savvy Aviation isn’t a maintenance shop – we empower you with the knowledge and expert consultation you need to be in control of your own maintenance events – so your shop takes directives (not gives them). Whatever your maintenance needs, Savvy has a perfect plan for you: