Understanding the underlying causes of engine roughness is the key to eliminating it.
One of the most common squawks reported by pilots and aircraft owners is a rough-running engine. If the roughness can be duplicated during a ground runup, then the mechanic might have a chance to troubleshoot it systematically.
Most of the time, however, the roughness is apparent only in-flight. Since the mechanic can’t reproduce the problem on the ground, he’s usually reduced to using guesswork—throwing parts, labor and money at the problem and hoping to get lucky. We call this process “shotgunning” and it’s something aircraft owners should try to avoid at all costs. The way to avoid it, of course, is never to put your mechanic in a position where he has to guess what’s wrong.
I can’t count the number of times I’ve seen expensive components—especially magnetos and fuel pumps—overhauled or replaced in an attempt to cure engine roughness. Those are usually desperation moves on the part of a mechanic who has run out of ideas. It’s unfortunate, because there’s almost no way a fuel pump problem can cause an engine to run rough, and it’s extremely rare for a magneto issue to cause an engine to run rough.
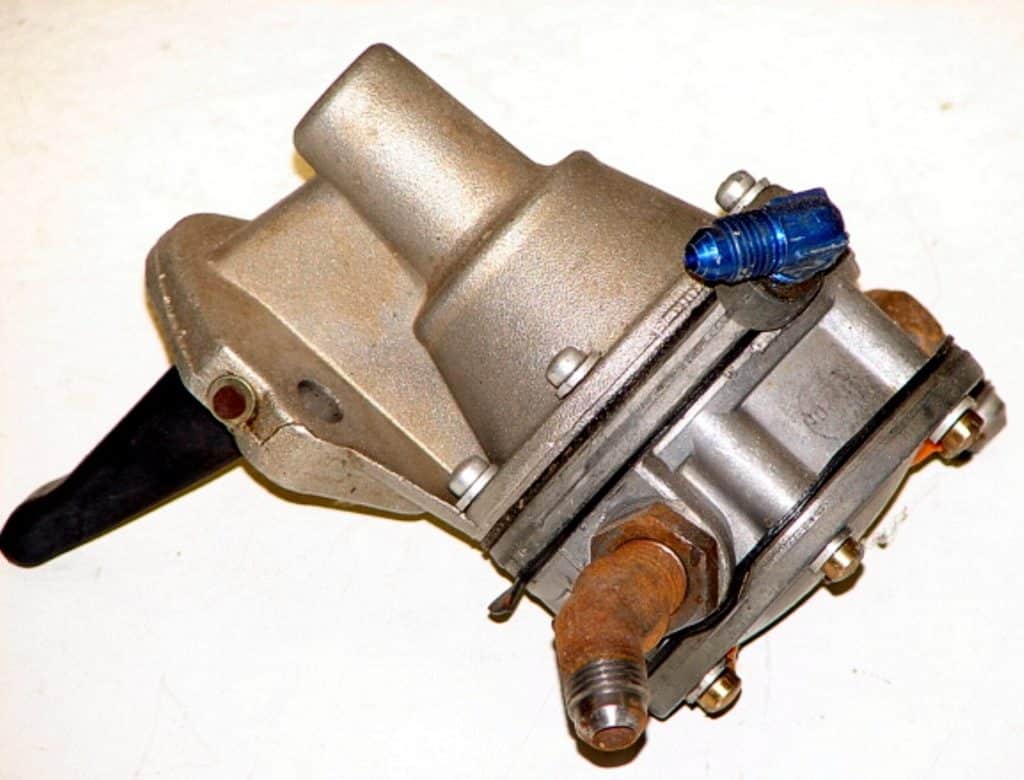
What causes roughness?
It’s important to understand that engine roughness is a very specific symptom that is almost always due to a very specific reason: The cylinders aren’t all producing the same amount of power.
So the underlying cause of roughness has to be something that can affect one cylinder differently than another cylinder.
If you think about it for a moment, there’s no way a fuel pump problem could affect different cylinders differently. If the fuel pump is not producing enough fuel pressure, this could cause the engine to lose power or run too hot, but it would affect all cylinders equally, and therefore would not cause roughness. The same is true of all fuel system components, with the sole exception of fuel nozzles on a fuel-injected engine. (Since a clogged, dirty or otherwise defective fuel nozzle affects only one cylinder, it’s a prime suspect when an injected engine runs rough.)
Similarly, almost all magneto issues affect all cylinders equally, so mag problems are very seldom implicated in engine roughness. If the roughness is related to the ignition system, the culprit is almost always going to be something that would affect only one cylinder. Most often it’s a bad spark plug; sometimes it’s a bad ignition harness lead or contact spring.
Usually the quickest way to diagnose such issues is to dump the aircraft’s digital engine monitor data and analyze it (or have it analyzed). You do have a digital engine monitor installed, don’t you?
Mixture maldistribution
One common complaint is an engine that runs smoothly at rich mixtures but becomes rough at lean mixtures, particularly lean-of-peak (LOP) mixtures. The cause is invariably that different cylinders are running at different air-fuel ratios, a phenomenon called “mixture maldistribution.”
In a perfect world, all cylinders would run at the exact same air-fuel ratio, but in the real world that never happens. There’s always one cylinder that runs leanest, another that runs richest, and the rest are somewhere in between the two outliers. We measure this maldistribution by calculating the difference between the fuel flow where the leanest cylinder reaches peak EGT and the fuel flow where the richest cylinder reaches peak EGT. That difference in fuel flow is called the “GAMI spread” and we want it to be as small as possible—preferably no more than ½ GPH or 3 PPH.

Figure 2 shows what happens if the mixture maldistribution is significant—as it typically is with most carbureted engines and with injected engines that aren’t equipped with position-tuned fuel nozzles. When the engine is being operated on the rich side of peak EGT (ROP), the maldistribution causes very little roughness because the slope of the HP-vs-FF curve is so flat that all the cylinders are producing the same power. However, when the engine is operated LOP, there’s significant roughness because the HP-vs-FF curve is steeply sloped and so the leanest cylinder is producing significantly less power than the richest cylinder. When different cylinders produce different amounts of power, we perceive the result as roughness.
What’s the solution? If the engine is fuel-injected, the fix is an easy one—install position-tuned fuel nozzles to reduce the GAMI spread to as close to zero as possible. A spread of ½ GPH or 3 PPH is quite decent; less is even better.
If the engine is carbureted, we don’t have the option of tweaking fuel nozzles. But it’s usually possible to improve mixture distribution significantly by means of some operational tricks. One thing that usually helps quite a bit is to avoid operating the engine at wide-open throttle. By retarding the throttle from the wide-open position just enough to obtain a slight decrease in manifold pressure (if the prop is constant speed) or a slight decrease in RPM (if the prop is fixed-pitch), the carburetor’s “enrichment circuit” is disabled and turbulence is introduced into the airflow through the carburetor throat by the slightly cocked throttle plate. Another thing that often helps—especially when OATs are cold—is the application of a little partial carburetor heat.
These operational tricks are especially useful with engines like the Continental O-470-series engines used in the Cessna 182 that are notorious for having terrible mixture distribution. Most carbureted Lycomings—especially 4-cylinder Lycomings—have fairly decent mixture distribution right out of the box.
The better the mixture distribution—i.e., the lower the GAMI spread—the leaner the engine can be operated before the onset of objectionable roughness.
Cycle-to-cycle variation
Another source of roughness is cycle-to-cycle variation (CCV). This refers to the fact that each successive combustion event in a particular cylinder is a bit different from the last one. As you can see clearly in Figure 3, these cycle-to-cycle variations increase rather dramatically at lean mixtures.
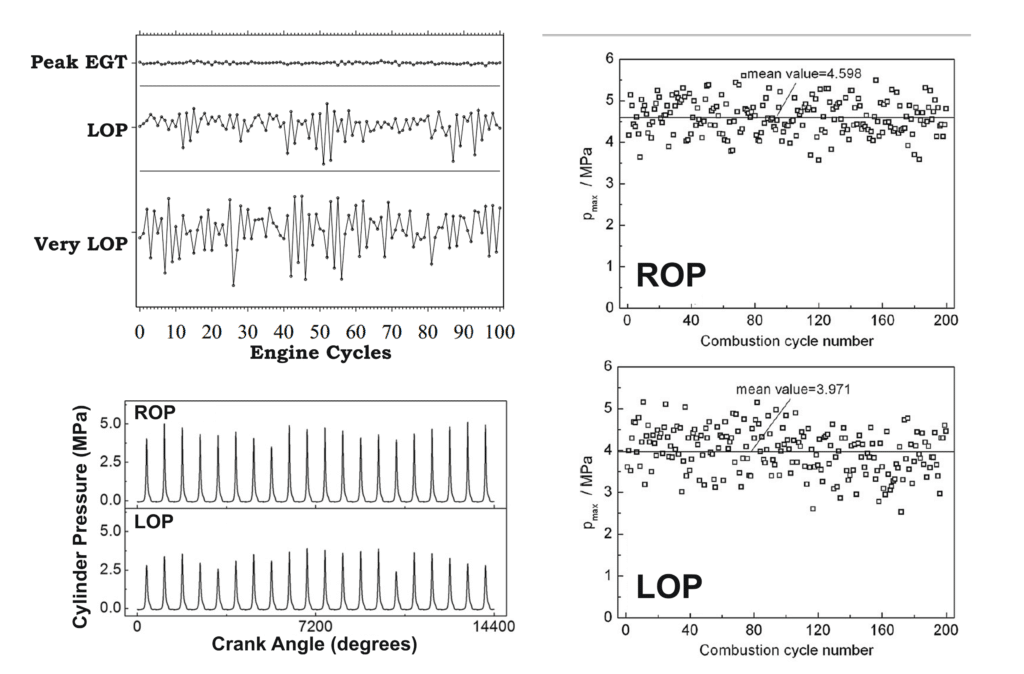
A tremendous amount of research has been done into the cause of CCV, particularly now that there’s so much emphasis on using very lean mixtures in automotive engines to minimize emissions. It turns out that there are a number of different factors that contribute to the CCV phenomenon.
One principal cause of CCV seems to be the rather chaotic fashion in which the spark that jumps across the spark plug electrodes ignites the local air-fuel mixture in immediate vicinity of the spark plug to create an “early flame kernel” that ultimately organizes itself into a flame front. The local gas flow in the vicinity of the spark plug and local non-uniformities in the air-fuel ratio in that vicinity at the moment of ignition contribute to highly variable and unpredictable combustion in first few milliseconds after the ignition event. Figure 4 offers a good illustration of just how chaotic and unpredictable this process is.
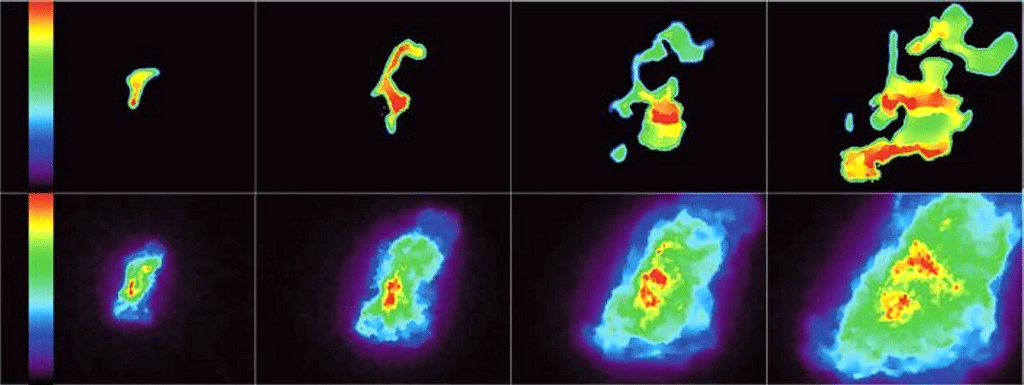
The shape and location of the early flame kernel has a profound effect on the flame front propagation during the remainder of the combustion event. An elongated flame kernel that extends away from the spark plug electrodes will result in faster flame front development that a compact flame kernel that remains close to the spark plug electrodes. The leaner the air-fuel mixture, the greater these variations tend to be.
Another significant contributor to CCV is the fact that it is never possible for the engine to expel 100% of the combustion residue out the exhaust valve at the end of a combustion event. There is always some small amount left in the cylinder when the next cycle begins. If the flame front gets a slow start, combustion will be incomplete and there will be some unburned fuel left over at the start of the next cycle. That can cause the next combustion event to start with a richer-than-normal mixture, resulting in a faster burn time and a lower-than-usual amount of unburned fuel at the end of the event. This “residual fraction effect” can cause alternating increases and decreases in peak combustion chamber pressure on successive cycles, particularly with lean mixtures.
CCV helps explain why engines always run a bit rougher LOP than ROP, even if the GAMI spread is close to zero. For the most part, we just have to live with this phenomenon, and accept the fact that the compelling advantages of LOP operation—cleaner, cooler, and much more efficient operation—is more than sufficient to accept a bit more engine roughness.
One thing that can help a bit is using fine-wire spark plugs, which tend to provide a bit more consistency in early flame kernels. Personally, I use massive-electrode plugs and just tolerate the slight additional roughness during LOP cruise. I just can’t bring myself to spend close to $100 for a fine-wire plug. Then again, I fly a twin that has 24 spark plugs…and I’m a world-class cheapskate. Your mileage may vary.
You bought a plane to fly it, not stress over maintenance.
At Savvy Aviation, we believe you shouldn’t have to navigate the complexities of aircraft maintenance alone. And you definitely shouldn’t be surprised when your shop’s invoice arrives.
Savvy Aviation isn’t a maintenance shop – we empower you with the knowledge and expert consultation you need to be in control of your own maintenance events – so your shop takes directives (not gives them). Whatever your maintenance needs, Savvy has a perfect plan for you: