More about what aircraft owners should know about piston aircraft engine oil.
Last month, we began our discussion of piston aircraft engine oil by discussing the types and properties of the various kinds of engine oil available, and I offered some thoughts about which oils I prefer and why. This month, I’ll continue the discussion by addressing oil additives, oil consumption, oil level, oil-change intervals, oil filter inspection and oil analysis.
Aftermarket additives
For as long as I can remember, there have been pitchmen promoting “miracle in a can” oil additives that claim to eliminate friction and wear, increase fuel economy, improve your landings, raise your IQ, and rescue your marriage.
The granddaddy of these is Marvel Mystery Oil. Folks have been pouring this red, sweet-smelling stuff into aircraft engines for more than 80 years. It was developed in 1923 by Burt Pierce, the inventor of the Marvel carburetor, and was intended as a fuel additive to clean carburetor jets. Why folks started using as an oil additive escapes me. The name “mystery oil” came from the fact that Burt Pierce refused to divulge its formula.
So far as I can tell, MMO doesn’t do any harm if used in moderation, but it doesn’t seem to do much good, either. Its formula is no longer a mystery since the Feds required the current manufacturer, Turtle Wax Inc., to publish the ingredients on a material safety data sheet. Turns out MMO has some interesting ingredients, including pig fat, perfume, and red food coloring in a base of petroleum distillate solvent. In case you were wondering, I don’t use MMO in my engines.
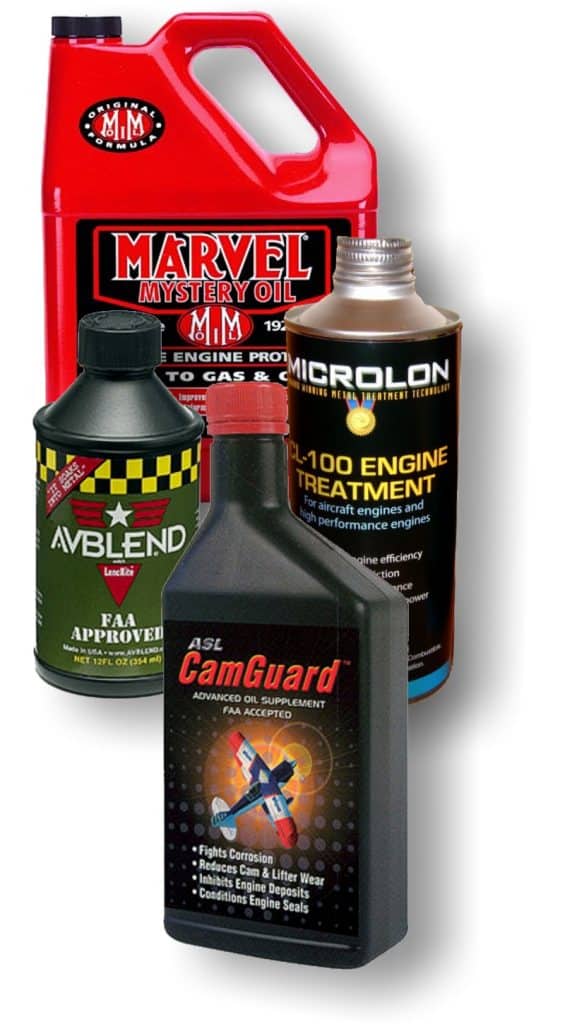
Some aftermarket oil additives—notably Microlon and Slick 50—contain a slippery resin called PTFE, which is made and marketed by DuPont under the tradename Teflon. The Microlon and Slick 50 folks claim that the stuff bonds with metal surfaces in your engine and virtually eliminates friction. This turns out to be pure bunk. Manufacturers of non-stick cookware will tell you just how difficult it is to get Teflon to bond to anything. Users of non-stick cookware will tell you just how easy it is to ruin the Teflon coating because it’s so fragile. NASA did a study of Teflon oil additives awhile back, and concluded that not only are they ineffective as a friction reducer, but they can actually damage an engine by clogging oil filters and tiny oil passages in hydraulic lifters. DuPont specifically warns against using Teflon in internal combustion engines. Nevertheless, the promoters of Microlon somehow convinced the FAA to approve its use in aircraft engines. My advice is to just say no.
AVBLEND has been around for two decades, and is a repackaged automobile oil additive called Lenkite that has been around for even longer. Back in the 90s, my friend Howard Fenton of Engine Oil Analysis in Tulsa ran a test of AVBLEND involving several piston twins that used AVBLEND in one engine and not in the other. When we looked at the oil analysis results for these airplanes, we could not tell which engine had the AVBLEND and which didn’t. Like MMO, AVBLEND appears to do no harm, but we can’t find any evidence of benefit either.
Given this dismal history of miracles-in-a-can, when another one called ASL CamGuard hit the market about five years ago, I was understandably skeptical. But in July 2007, I ran into CamGuard developer Ed Kollin at EAA AirVenture, got into a lengthy conversation with him, and discovered that he wasn’t your typical snake oil salesman. Turns out that Ed is a very sharp and experienced lubrication chemist who ran Exxon’s engine lab for many years, was heavily involved in the development of Exxon Elite, and seems to know more about aircraft oil and additives than anyone I’ve ever met.
After talking to Ed at length, I decided to run a test of CamGuard in my own airplane. I used it quietly for 18 months before telling anyone. Studying my oil analysis results, I found that the big spikes in iron (caused by rust) that I had always seen whenever the aircraft was idle for a month or more were completely eliminated. That got my attention. I also found a modest across the board reduction in other wear metals on the order of 10 to 20 percent. I examined the oil analysis history of several other airplanes using CamGuard, and saw much the same thing.
I’ve been using CamGuard in my engines for three years now, and I’m convinced the stuff works. We’re now using CamGuard in hundreds of airplanes managed by my company, all of which are on oil analysis, and we almost always see a clear reduction in iron and improvement in other wear metals once we start using CamGuard.
For most of the airplanes we manage, we recommend Aeroshell W100 with a pint of CamGuard added at each oil change. That’s what I use in my own airplane, and my two engines are at nearly 200% of TBO and still going strong. For wintertime operations in cold climates, I recommend Phillips X/C 20W-50 multigrade with a pint of CamGuard.
Oil consumption
Take any group of aircraft owners, add a pitcher or two of beer, and it’s not long before they’re comparing notes on who’s airspeed is the highest and whose oil consumption is the lowest. The subject of airspeed is beyond the scope of this article. But I’m here to tell you that low oil consumption is highly overrated.
Lots of factors affect oil consumption. Six cylinder engines use more oil than four-cylinder engines. Big-displacement engines use more oil than smaller-displacement engines. TCM engines typically use more oil than Lycomings of similar horsepower. Chrome-plated cylinders use more oil than steel cylinders. Nickel-carbide cylinders use less oil than steel. Airplanes that fly a lot of short trips use more oil than ones that fly fewer long trips. And so forth.
Anything from a quart in 20 hours to a quart in 4 hours is in the normal range. I’ve seen engines that burned a quart in 4 hours throughout their entire life and made it past TBO without any problem. I’ve also seen engines that used hardly any oil and then wound up needing a top overhaul after 500 hours.
TCM doesn’t consider oil consumption to be a cause for concern until it exceeds a quart in three hours, and says that it isn’t an airworthiness issue until it exceeds about a quart per hour. Now, I don’t think any of us would allow our engines to get to the point of burning a quart per hour, simply because it’s so darned embarrassing to run out of oil before you run out of fuel.
I do get concerned about any sudden increase in oil consumption. If an engine has been using a quart in 12 hours for most of its life and suddenly starts using a quart in 6 hours, that means something has changed, and to me that’s a red flag. Until we figure out WHAT changed, we can’t be sure whether it’s serious or benign.
I also get concerned if the oil starts to turn dark and opaque quickly after an oil change—say, within 10 hours or so. That indicates excessive blow by, and we’ll want to do some testing and troubleshooting to determine why this is happening and which cylinder is the culprit.
Many owners install aftermarket air-oil separators to reduce oil consumption and keep the belly clean. I don’t like air-oil separators, because they return all sorts of ugly, nasty stuff to the crankcase that would otherwise be expelled out the breather. I think engine guru John Schwaner of Sacramento Sky Ranch says it best on his website: “Air/Oil separators are like hooking a line up to your anus and piping it back into your mouth. Excuse the crude analogy, but who wants the water, acids and other combustion residuals pumped back into one’s engine?”
Dipstick level
Oil consumption can be exacerbated by filling the sump to the top mark on the dipstick. Many engines don’t like that, and will promptly toss a quart or two overboard until the oil level decreases to a level that the engine likes better. When an engine does that, it’s trying to tell you something.
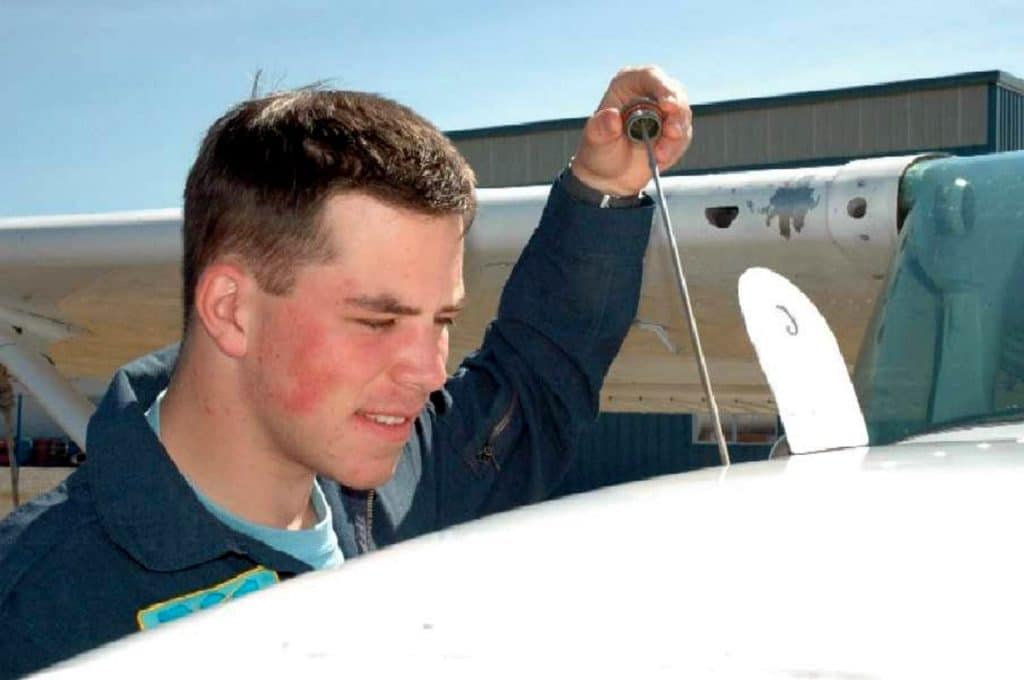
There’s no reason to fill the oil to the brim. Before an aircraft engine can be certified, the FAA requires the manufacturer to demonstrate that the engine runs just fine in all normal flight attitudes with the oil sump filled to just one-half capacity.
Actually, most engines can function with even less oil than that. If you’re curious how much less, just consult the engine’s type certificate data sheet, available on the FAA website.
For example, the TCM IO-550-N engine in a Cirrus SR22 has an 8-quart sump, but will run fine down to 3½ quarts. Most Lycoming O-320s also have an 8-quart sump but need only 2 quarts.
As a rule of thumb, we recommend operating most engines at about 2/3 of the maximum sump capacity. That means running 8-quart engines at about 5 or 6 quarts, and 12-quart engines at about 8 quarts. If your engine uses a lot of oil, you might want to add one more quart to those figures for a little extra cushion.
Oil-change interval
Because piston aircraft engines get the engine oil so filthy, regular oil and filter changes are an absolute must. Never go more than 50 hours or 4 months between changes, whichever comes first. (If you fly less than 150 hours a year, the 4 months will probably come first.) Some experts (like CamGuard’s Ed Kollin) recommend changing the oil every 25-30 hours or 3 months. If you have an older plane that has only an oil screen rather than a full-flow filter, you should not exceed 25 hours between oil changes.
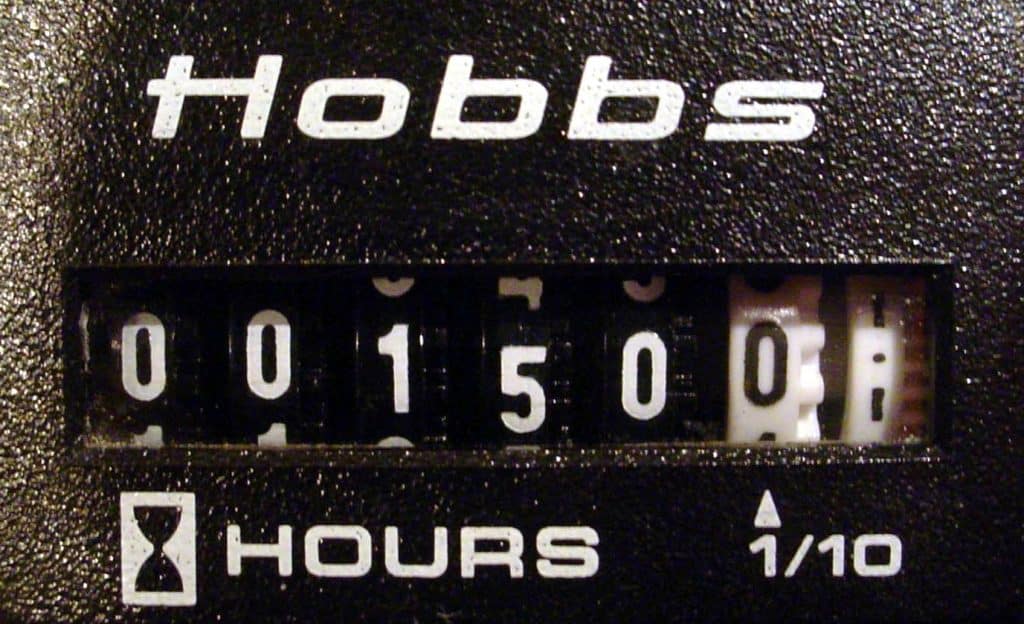
If appreciable metal is found in the oil filter, or if the oil analysis report comes back with any red flags, we will normally put the engine on a reduced oil-change interval until the source of the metal is identified or the problem resolves itself.
If you’re approaching an oil change and you know the airplane will go unflown for several weeks, it’s best to change the oil before the downtime rather than afterwards. Dirty oil tends to be corrosive, and you really don’t want your expensive crankshaft and camshaft bathed that stuff for any longer than necessary.
Oil filter inspection
Every time we change the oil, we also replace the oil filter, cut open the old filter, and carefully inspect the filter media for the presence of metal. Tossing an oil filter in the trash uncut is a capital offense.
We don’t get too excited about a few flecks of metal in the filter, particularly if it’s non-ferrous metal such as aluminum or copper or bronze.
If there’s a significant amount of metal in the filter, we need to investigate to determine what kind of metal it is, and where in the engine it’s coming from. For example, metal whiskers (as opposed to flakes or particles) that are ferrous (attracted by a magnet) are typically associated with a failing lifter or cam lobe.
Of course, the source of the metal isn’t always so obvious. If we’re still not sure of where the metal is coming from after examining it with a magnifying glass and checking it with a magnet, the next step is to send it out to a lab for analysis under a scanning electron microscope. This isn’t nearly as scary as it sounds. It typically costs less than a hundred bucks and the results come back within a few days. (I recommend Aviation Laboratories in Louisiana for such analysis; www.avlab.com.) The SEM report will identify the exact quantity, shape, and type of metal, and usually the exact alloy. This is often sufficient to determine where in the engine the metal is coming from.
Oil analysis
In addition to oil filter inspection, we also take an oil sample at every oil change and send it out for spectrographic oil analysis. This is not a substitute for filter inspection, but a complement. Inspecting the filter allows us to detect metal that is big enough to be caught by the filter and visible to the naked eye. Oil analysis allows us to detect microscopic metal particles that are small enough to pass through the filter and would be too small to see anyway. If we want to be confident that we will catch all abnormal wear events, we need to do both.
Oil analysis is superb at detecting very slow wear events that never throw off metal particles big enough to see. It’s also very good at providing early warning of accelerating wear events that would eventually show up in the filter or some other way, but not until significant damage is done.
I use and recommend Blackstone Laboratories in Ft. Wayne, Indiana (www.blackstone-labs.com) for oil analysis. There are lots of labs that do this work, but I think Blackstone is the best in the business. I’ve used Blackstone for years, and my company uses them for all of our managed-maintenance clients.
Here is an excerpt of an oil analysis report from Blackstone on the right engine of my Cessna 310. (I fly a twin, so of course I get two reports at each oil change.) The report for my left engine was unremarkable, but the one for the right engine was a bit more interesting.
The column on the left is the most recent sample, taken on August 2nd, 2010. The engine was then at 2,608 hours since major overhaul (more than 1,200 hours beyond TCM’s recommended TBO of 1,400 hours for this engine). Aluminum, chromium and iron all look great—those would be from pistons, rings, and cylinder barrels, respectively. Copper is fine as well—that would be from bearings or thrust washers. Lead is low, indicating that the engine does not have excessive blow-by. Silicon is also low, so the air filter is doing its job nicely. So far, so good.
The one red flag on this report is nickel, which is more than twice what it has been historically. The only source of nickel in my engines is exhaust valve guides, so there must be a valve guide that is experiencing accelerated wear. The elevated nickel has been present for at least two years, but is gradually increasing. Sooner or later, there will be a burned exhaust valve in my future and I’m going to have to pull a jug.
I did a compression test and borescoped all the cylinders, so I know that none of the exhaust valves are leaking or showing any abnormal heat signatures…yet. But the oil analysis is telling me that an exhaust valve problem is inevitable, so I’ll be watching closely. Of course, the oil analysis can’t tell me which cylinder is having the problem, but that’s something I’ll know in the fullness of time by means of continued borescope inspections and keeping a close eye on my digital engine monitor. Eventually, a distressed exhaust valve will become evident, and the corresponding cylinder will need to come off for repair.