We’re seeing an epidemic of Champion spark plug problems. Champion insists its plugs are fine and the problems are self-inflicted. The truth may be a bit more complicated.
By Mike Busch
Premature failures of Champion-brand aviation spark plugs first showed up on my radar screen several years ago. My company manages the maintenance of nearly 400 piston-powered airplanes, the lion’s share of them high-performance singles and twins powered by Continental 520- and 550-series engines. So there are roughly 5,000 spark plugs flying in our “fleet” at any given point in time. The overwhelming majority of those spark plugs were Champions.
I’d been using Champion spark plugs in my own airplane for decades without any problems, but my personal experience had been exclusively with their conventional massive-electrode plugs (RHB32Es to be exact). In contrast, more than half the airplanes managed by my company were using Champion’s top-of-the-line fine-wire iridium RHB32S plugs. These exotic fine-wire plugs are very pricey—about $125 apiece (list price) compared with about $40 for massives. However, the fine-wire plugs should last about 1,500 hours (compared to 400-500 hours for massives), so their life-cycle cost should theoretically be comparable.
What we were seeing, however, was premature failures of these Champion RHB32S fine-wire plugs after just a few hundred hours in service, and occasionally after as little as 50 hours, These failures sometimes showed up when the aircraft owner complained about a rough-running engine, and when we had the owner perform an ignition-system stress test (i.e., an in-flight LOP mag check) and analyzed their engine monitor data, we could clearly see marginal ignition performance. Other times, the spark plug failures turned up at annual inspection when an IA removed and inspected the plugs.
Cracked Insulators
In every case, the failure mode was the same: cracking of the plug’s ceramic core nose insulator (see Figures 1 and 2). Typically we found the insulator cracked in two places approximately 180º apart; occasionally it cracked in three places. Most of these cracks were caught before the insulator came apart completely and fell into the combustion chamber, but sometimes major chunks of the insulators were completely missing. This really concerned me, because I knew this kind of failure had the potential of initiating a destructive pre-ignition event that could destroy a piston and potentially even trash an entire engine.
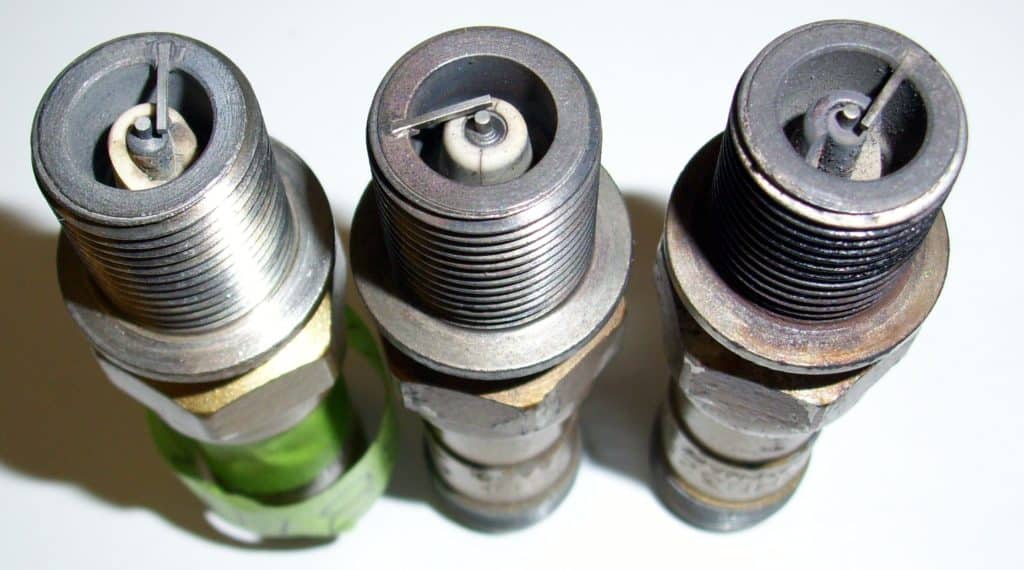
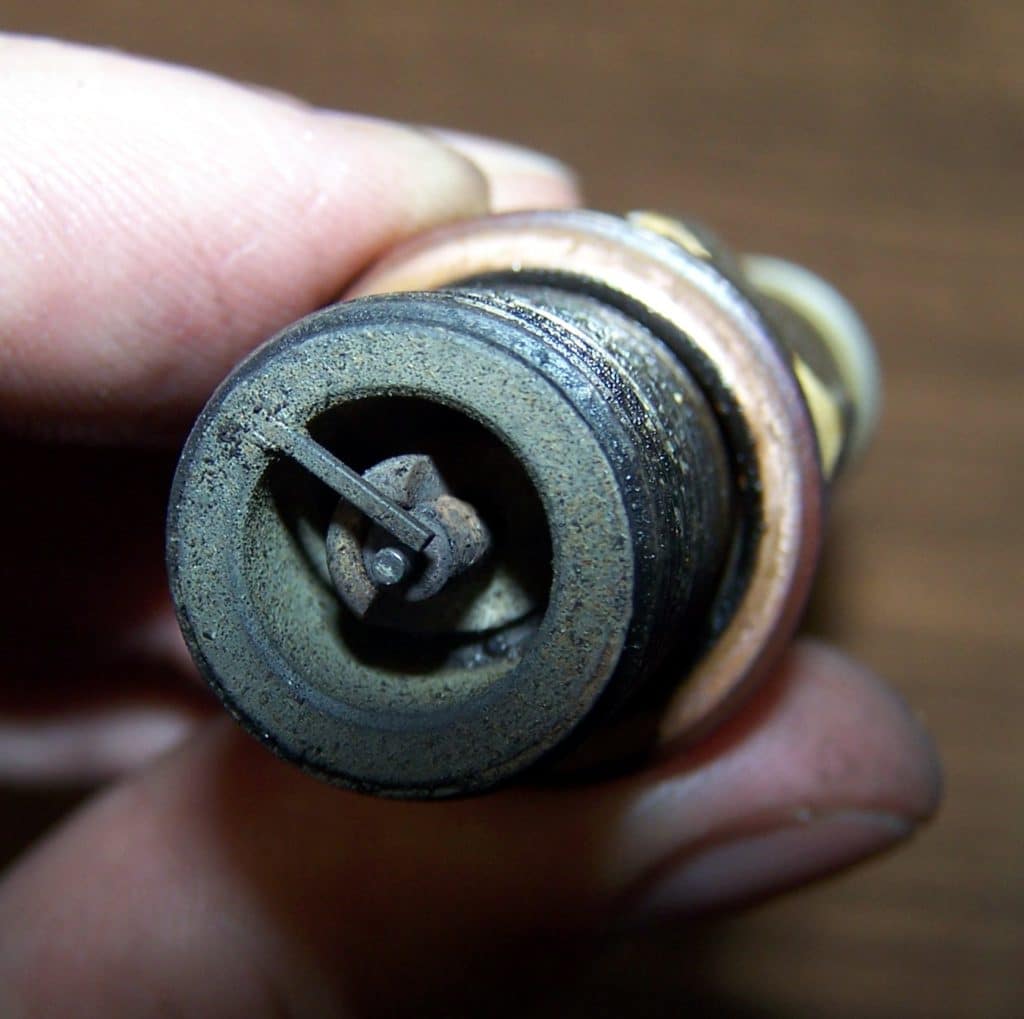
The initial insulator failures that came to my attention occurred in Cirrus SR22 Turbo aircraft—not surprising because my company manages more than 7% of the Cirrus fleet in the U.S., and more than half are turbos. At first, I assumed that the failures were confined to these aircraft because of their unusual powerplant configuration—they are powered by a Continental IO-550-N high-compression engine with an aftermarket turbonormalizing system provided by Tornado Alley Turbo, and they are often operated in cruise up to 85% power.
But soon we started seeing Champion RHB32S plugs with cracked insulators showing up in normally-aspirated Cirrus SR22s. And in Cessna Corvalis and T310 airplanes. And in Bonanzas and Barons, both turbo and normally aspirated. It gradually became clear to me that these problems were not limited to any particular aircraft make or model, nor to turbocharged/turbonormalized powerplants. The only common thread I could find was that these aircraft were all powered by Continental 520- and 550-series engines equipped with Champion RHB32S fine-wire spark plugs.
Much later, I learned that the same problem was rampant in the Piper PA-46-350P Malibu Mirage fleet. These aircraft are powered by a Lycoming TIO-540-AE2A engine. So the problem is not confined to Continentals.
So far, as I’m writing this, I’ve not seen this cracked-insulator problem occur in any Lycoming engine, nor with any Champion RHB32E massive-electrode spark plug, nor with any Autolite/Tempest URHB32S fine-wire or URHB32E massive-electrode spark plug. The cracked insulators seem to be occurring exclusively on Champion fine-wire plugs. I’m not a design engineer, but if you compare the construction of Champion RHB32S and Autolite/Tempest URHB32S fine-wire plugs (see Figure 3), it seems pretty obvious that the latter has a much more robust-looking core nose insulator than the former.
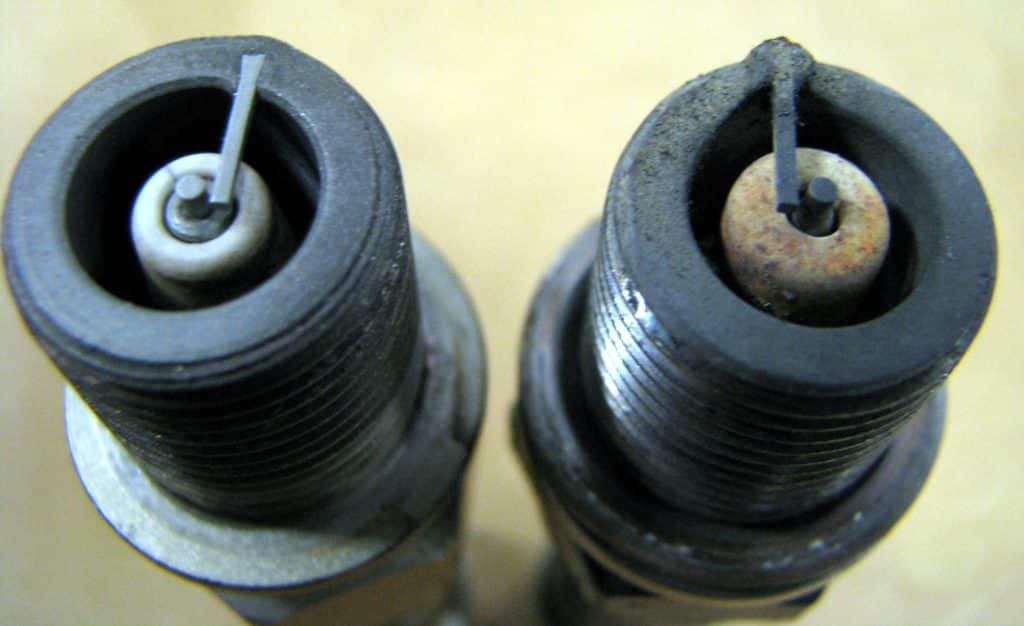
I figured if we were seeing these cracked insulators, others should be seeing them, too. So I started checking around. I talked to Jeanne Fenimore, proprietress of Aircraft Spark Plug Service in Van Nuys, Calif.—the premier spark plug reconditioning company that I’d used for years to clean, gap and test my spark plugs every 100 hours. Jeanne told me that she frequently found cracked insulators in Champion fine-wire spark plugs, and this was the leading cause of rejection for these plugs. I spoke with George Braly, chief engineer at Tornado Alley Turbo, who confirmed that they were seeing these same failures. I also contacted several large service centers and they told me the same thing.
Who ya gonna call?
George and I agreed that this was a potentially dangerous situation, and that something needed to be done. George spoke with his contacts at Champion Aerospace, but they seemed uninterested and unpersuaded, saying only that these plugs had been in service for decades and nothing had changed in their manufacture.
Meantime, I spoke with someone at the FAA’s Engine and Propeller Directorate at the New England Region, who referred me to someone else at the FAA’s Atlanta Aircraft Certification Office (ACO). After some dialog, I wound up sending a dozen RHB32S with cracked insulators to the Atlanta ACO, all carefully tagged to indicate the aircraft and engine make and model and the spark plug time-in-service.
Six months passed. Nothing happened. It became clear that Champion believed this was a non-issue, and that the FAA wasn’t interested in pressing the issue. Meantime, cracked RHB32S plugs kept showing up.
The finger pointing begins
George Braly finally ran out of patience. On September 23, 2011, Tornado Alley Turbo issued a pair of Mandatory Service Bulletins, SB11-05 covering TAT-turbonormalized Cirrus SR22s and SB11-06 covering TAT-turbonormalized Bonanzas. Both MSBs provided detailed photos of failed Champion RHB32S fine-wire spark plugs and provided details of a well-documented destructive pre-ignition event that TAT believed to be caused by a cracked RHB32S plug. The MSBs called for removing all RHB32S spark plugs within the next 50 hours time-in-service and replacing them with massive-electrode plugs.
A week later, on September 30, 2011, Champion Aerospace issued Service Letter SL74-10-001, with a very unusual title: “Official Champion Aerospace Position on the Service Bulletin published by Tornado Alley Turbo on 9/23/2011 – TAT SB11-05.” I found this to be an extraordinary document, because in the decades that I’ve been paying attention to such things, this is the first time I’ve ever seen an aviation manufacturer issue a service bulletin for the specific purpose of discrediting another manufacturer’s service bulletin.
In SL74-10-001, Champion states that they had examined a number of cracked core nose insulators and determined that there were no manufacturing defects. They said that the plugs had been manufactured on the same assembly line in the same plant for over 20 years, and that there had been “no significant process changes” during that time. They said they had conducted performance testing of the plugs and determined that their heat range was within specifications. I have no reason to believe that any of those statements are untrue.
Then SL74-10-001 goes on to say this:
“Champion believes the most likely cause of these fine wire core nose cracks to be excessive lean-of-peak operation in which precise control over the engine’s performance cannot be maintained to avoid detonation and/or pre-ignition. Champion recognizes that some limited groups advocate running engines aggressively lean of peak; outside the engine OEM recommended procedures. Champion’s belief is that running the engine outside the OEM operating guidelines can increase the likelihood of detonation and/or pre-ignition which will potentially cause significant engine damage, including damage to spark plugs.
“Finally, Champion has consulted with the engine manufacturers and other industry experts on the matter. These experts have reviewed the evidence and concluded the only common element is that the engine anomalies occurred where aircraft operators were likely running their engines outside the OEM recommended operating parameters. Champion advises operators to consult and strictly follow these recommended OEM engine operating parameters to avoid damage to their engine and spark plugs.”
Whoa! Time out!
Looks to me like the author of Champion SL74-10-001 might not be the sharpest knife in the drawer when it comes to the physics of combustion. It is damn near impossible to achieve detonation during LOP operation in a piston aircraft engine (unless you’re running it on Jet A or Jack Daniels). Minimum detonation margin occurs at approximately 50ºF ROP. The further away from 50ºF ROP you go—either rich or lean, but particularly lean—the more difficult it is to achieve detonation.
As for pre-ignition, this can only take place if there’s some piece of foreign material in the combustion chamber that starts glowing red-hot and acts like a glow-plug to initiate combustion before the spark plug fires. Excessive combustion chamber deposits can do this—the kind one often sees on engines that are run very rich, but never on engines that are run LOP. (A cracked or broken spark plug core nose insulator can to this, too.) Any way you look at it, an engine running LOP is far less likely to suffer either detonation or pre-ignition than one running ROP.
Also, I don’t know exactly which “engine manufacturers and other industry experts” Champion was talking to before writing SL74-10-001, but the notion that LOP operation is somehow against manufacturer’s guidance is just flat wrong. Continental has long approved LOP operation, and their Aerosance FADEC is programmed to operate engines LOP. The POH for the Cirrus SR22 Turbo specifically REQUIRES that the engine be operated LOP in cruise.
Lycoming traditionally disapproved LOP in the past, but even they have finally entered the 21st century. Lycoming’s chief engineer announced at EAA AirVenture 2011 (two months before SL74-10-001 was issued) that Lycoming now approves LOP operation.
My sense is that Champion was in such a rush to rebut TAT’s service bulletins that it didn’t take the time to do its homework.
Certainly the engineers at Cirrus Aircraft weren’t buying it. A couple of months after Champion’s issued its SL74-10-001, Cirrus published its own SB recommending against the use of Champion fine-wire plugs in all Cirrus aircraft (including normally aspirated ones not covered by the TAT MSB), and recommending the use of massive-electrode plugs.
The latest salvo in these finger-pointing exercises is an April 16, 2012 report commissioned by Champion and authored by Bill Brogdon, former chief engineer for TCM and now an independent consultant. In his report, Brogdon was smart and intellectually honest enough to admit that LOP operation doesn’t cause detonation and that cracked spark plug insulators can indeed cause pre-ignition. He offers a couple of interesting theories about what might be damaging the RHB32S plugs, including:
- The 85% LOP cruise settings approved by the Cirrus SR22 POH.
- The transition from ROP to LOP (“big mixture pull”) which briefly transitions through the 50F ROP region of minimum detonation margin.
- The fact that TAT’s turbonormalized engines have an 8.5-to-1 compression ratio and therefore presumably lower detonation margin than Continental’s turbocharged engines with a 7.5-to-1 compression ratio.
Unlike Champion’s fundamentally flawed arguments in its SL74-10-001, Brogdon’s arguments are somewhat plausible from an engineering point of view. Problem is, they do not explain why we’re seeing RHB32S spark plugs with cracked core nose insulators in normally aspirated aircraft and in low-compression TIO- and TSIO-series turbocharged engines.
What we know for sure
Regardless of whom you believe, the following points strike me as being incontrovertible:
- Champion RHB32S fine-wire spark plugs are failing at an unacceptable rate in the face of modern LOP engine operating procedures that are approved (and in some cases required) by the engine and aircraft manufacturers.
- These failures are not being seen in Champion RHB32E massive-electrode plugs on engines being operated in exactly the same fashion, nor are they being seen in Autolite/Tempest URHB32S fine-wires or URHB32E massives..
To my way of thinking, the debate about whether these failures are the fault of the spark plugs or the fault of the pilots is not particularly helpful. The salient point is that Champion RHB32S fine-wire plugs are substantially less robust and more failure-prone than the other alternative spark plugs approved for use in Continental 520- and 550-series and Lycoming 540-series engines. In my book, that’s a good reason to avoid using them. That’s certainly what we’re recommending to our managed-maintenance clients.
It strikes me as both ludicrous and arrogant for Champion to suggest that we modify our engine operating procedures to protect their temperamental fine-wire spark plugs, when the easier and more attractive course of action is simply to switch to more robust plugs (meaning pretty much any other spark plug on the market).
But wait, there’s more!
Completely unrelated to the problem of cracked core nose insulators in Champion fine-wire plugs, there’s another potentially serious issue with all Champion aviation spark plugs, both fine-wire and massive-electrode. It has to do what appears to be a failure-prone design of the internal resistor inside the spark plug.
All aviation spark plugs have such a built-in resistor. Its purpose is to limit the current that passes through the plug when the magneto fires it. The value of the resistance is fairly critical. If the resistance is too low, the spark plug electrodes will erode rapidly. If the resistance is too high, the spark will be weak and ignition performance will be marginal, particularly in demanding situations like engine starting and LOP operation. If the resistance is high enough, the plug will fire erratically and there’s a serious threat of crossfire inside the magneto distributor block, particularly with Slick magnetos.
The optimum resistance for an aviation spark plug is 1,500 to 2,000 ohms. Magneto guru Cliff Orcutt of Aircraft Magneto Service (who knows more about magnetos than anyone else I know) recommends checking every spark plug with an ohmmeter at each 100-hour spark plug maintenance cycle, and rejecting any spark plug that measures more than 5,000 ohms. We started doing that on our clients’ plugs a couple of years ago, and the results were nothing short of shocking.
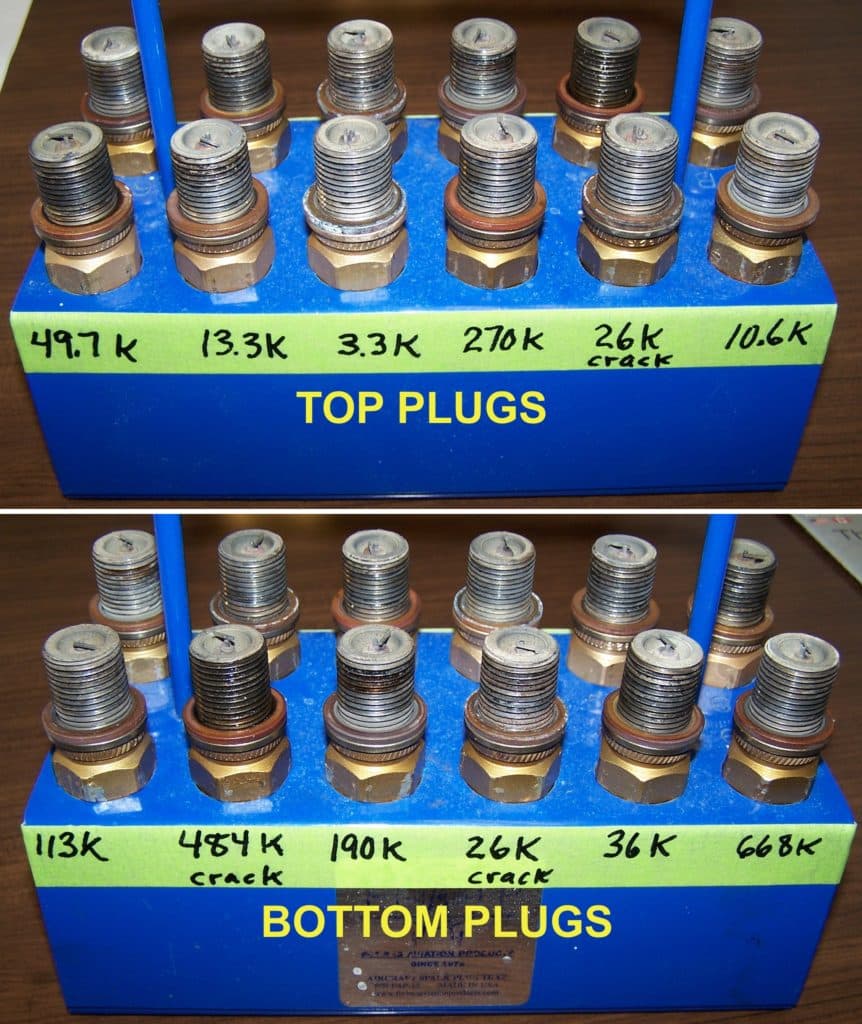
Figure 4—Ohmmeter measurements on 12 Champion spark plugs removed from an IO-550 engine. Only one measured within acceptable resistance limits; the other 11 were rejects.
Look at the resistance measurements found recently on the 12 spark plugs from one of our client’s engines (see Figure 4). Only one out of the 12 plugs measured less than 5,000 ohms. The rest were way out of spec, and four exceeded 100,000 ohms. (To make matters worse, these plugs were Champion RHB32S fine-wires, and three out of 12 had cracked insulators.)
This problem is not limited to Champion fine-wire plugs. It affects Champion massive electrode plugs as well. Recently, I ohmed out the five RHB32E massive-electrode plugs that I had been carrying in the wing locker of my Cessna 310 as spares, and came up with the following values: 1.7K, 1.8K, 4.2K, 5.6K, and infinity. Yes, you read that right, one of the plugs was totally open-circuit, or at least more than the 9.99 megohms that is the upper limit of what my digital volt-ohmmeter can measure. These plugs had approximately 100 hours on them, and looked almost new. Jeanne Fenimore had tested them on her “bomb tester” and all passed the test. Only an ohmmeter can detect a problematic resistor, and very few mechanics perform that test.
The design of the internal resistor in Autolite/Tempest plugs is entirely different than the one in Champion plugs. We have never found an Autolite/Tempest plug that measured more than 2,000 ohms, even ones that were very long in the tooth.
In case you were wondering, I now use nothing but Tempest URHB32E massive plugs in my own airplane, and my company strongly recommends to our managed-maintenance clients that they use only Tempest massives or fine-wires. For those that still prefer to use Champion massives, we recommend that the plugs be ohmed out every 100 hours during normal spark plug maintenance, and rejected if they measure more than 5,000 ohms.
Don’t get me wrong. I like Champion Aerospace. I like their oil filters. I love the fact that they acquired the Slick line of mags and harnesses from Unison when Unison decided they wanted to get out of the piston-engine ignition business. I love the fact that there is competition in the spark plug business between Champion and Tempest because that’s what keeps prices reasonable.
I only wish Champion would devote their energies to improving their spark plugs rather than working so hard to defend them. The company is clearly capable of innovation. They proved that several years ago when the totally redesigned their oil filters. I think it’s high time they did the same thing with their spark plugs and introduced a truly competitive product compatible with the way we operate our engines in the 21st century.
You bought a plane to fly it, not stress over maintenance.
At Savvy Aviation, we believe you shouldn’t have to navigate the complexities of aircraft maintenance alone. And you definitely shouldn’t be surprised when your shop’s invoice arrives.
Savvy Aviation isn’t a maintenance shop – we empower you with the knowledge and expert consultation you need to be in control of your own maintenance events – so your shop takes directives (not gives them). Whatever your maintenance needs, Savvy has a perfect plan for you: