“I flew my Skylane about three hours from Pompano to Tallahassee to drop off my daughter,” Alvin posted on his SavvyAnalysis ticket. “After refueling, I taxied out to take off for home. Although the plane performed beautifully on the flight to Tallahassee, on departure the engine started shaking badly and the plane would not climb.”
“I throttled back to idle and tried to put the plane back down on the runway,” Alvin continued, “but quickly realized there wasn’t enough room to stop. The plane bounced on the runway as I applied full throttle and prayed the plane would remain airborne. It did, but just barely with marginal power. I declared an emergency and managed to limp around to an adjacent runway.”
“After shutting down, I drained some fuel from the gascolator and it appeared normal in color and free of water. I then started the engine and did a 1500 RPM mag check, which also seemed normal. I then dumped the data from my JPI EDM-900 engine monitor and uploaded it to the SavvyAnalysis platform. Can you please take a look at let me know your thoughts?”
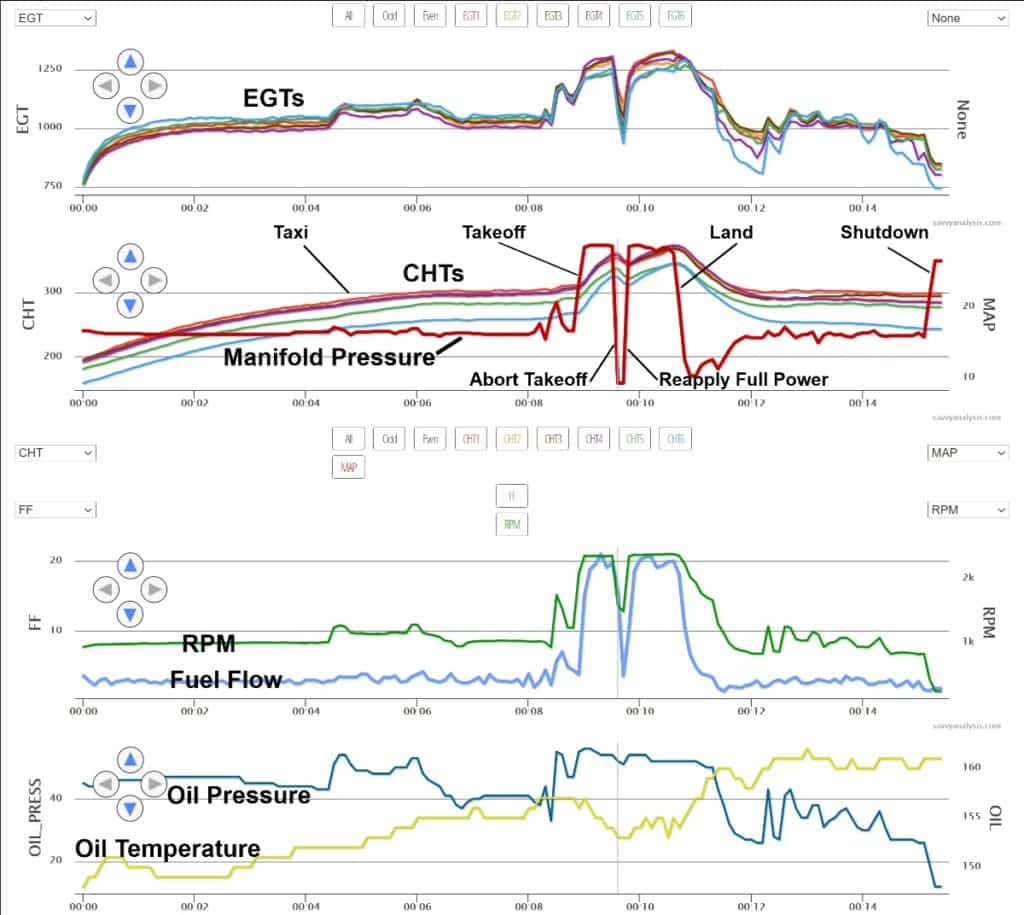
Unhelpful Data
Savvy analyst Ray Eaker reviewed Alvin’s data. Ray has been an A&P mechanic for over 30 years and is the builder/owner/pilot of a Van’s RV-7, so he definitely knows his stuff. But try as he might, Ray couldn’t find any smoking gun buried in the JPI data.
“Unfortunately, your emergency happened awfully fast,” Ray told Alvin, “and your EDM-900 was set to its very slow default sampling rate of only 10 samples per minute.”
When piston engines shake or run rough, it normally is because the cylinders aren’t all making the same amount of power. This usually shows up in the form of wide variation in EGTs. But when Ray looked at Alvin’s data, all the EGTs seemed to be tracking close together.
“To be honest, I’m not seeing anything in the captured data to suggest that your engine was running rough, much less why it was doing so,” Ray confessed. “Except for your attempt to abort the takeoff, everything I’m seeing in your JPI data looks pretty normal. I know this doesn’t help much, but I’m coming up dry.”
Ray suggested that Alvin should probably take the plane to one of the maintenance shops on the field and have them look over the Continental O-470-U to see if they could spot anything wrong. “But be careful,” Ray cautioned, “those guys have a reputation for running up a big bill unless you keep them on a short leash.”
Shotgunning
The shop pulled the Skylane’s cowling and looked over the engine, but couldn’t see anything obviously wrong. No significant fuel, oil, exhaust or induction leaks. The induction air filter looked fine, as did the carburetor airbox and carb heat valve. Mag timing was within tolerance. The spark plugs were worn but serviceable. The cylinders looked normal under the borescope.
The shop’s technician replaced the spark plugs on general principles. He gave the engine a thorough ground run without finding any issues. The shop presented Alvin with an invoice and a signed logbook sticker, and told him they had no explanation for what he’d experienced during that ill-fated takeoff.
Alvin took the plane up for a few trips around the pattern at Tallahassee. The plane performed normally. He flew the plane home to Pompano (about three hours) and all seemed fine. He was spooked about not having a credible explanation for the scary power-loss incident. Could it have been spark plug-related? Carb ice?
Meantime, because he’d declared an emergency with Tallahassee Tower, Alvin was contacted by an FAA inspector from the Birmingham FSDO, who quizzed him about the incident and asked him to email a written statement describing what had happened. Seems the FSDO was looking for an explanation, too, but Alvin didn’t have any good answers.
It happened again!
“It happened again on the last flight,” Alvin posted about three weeks later. “I was in a climb when the engine started to vibrate and lose power. It wasn’t nearly as bad this time, but definitely vibration. There was also a brief flutter as I was turning base-to-final before landing.”
“I had my shop pull the propeller and send it out for inspection, but the prop shop found nothing wrong. Now they’ve pulled the prop governor for inspection.”
This struck Ray as a desperation move, since it’s hard to imagine how a prop could cause vibration that is intermittent, and even harder to imagine how a prop governor could do so.
“Please review my flight data for my most recent flight. Let me know your thoughts about why the fuel flow dropped off when RPM remained constant.”
Nothing unusual about that, Ray thought, the RPM would remain constant even if you pulled the mixture control and just let the prop windmill. That’s why they call it a constant-speed prop.
An Important Clue
Ray pulled up the SavvyAnalysis chart of the JPI data for Alvin’s most recent flight. This time, something on the chart definitely caught his attention:
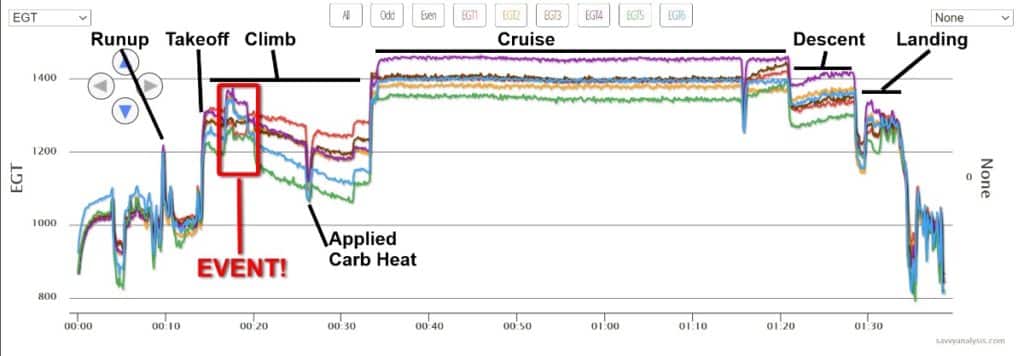
During the climb phase of the flight, Ray could clearly see two “events” that departed from the usual climb profile. He identified the second, a brief one that occurred about 27 minutes after engine start, as being caused by Alvin pulling out the carburetor heat control in an apparent attempt to check for carb icing. The first, a longer one that began about 17 minutes after engine start, was more puzzling. Ray zoomed in to get a better look at it:
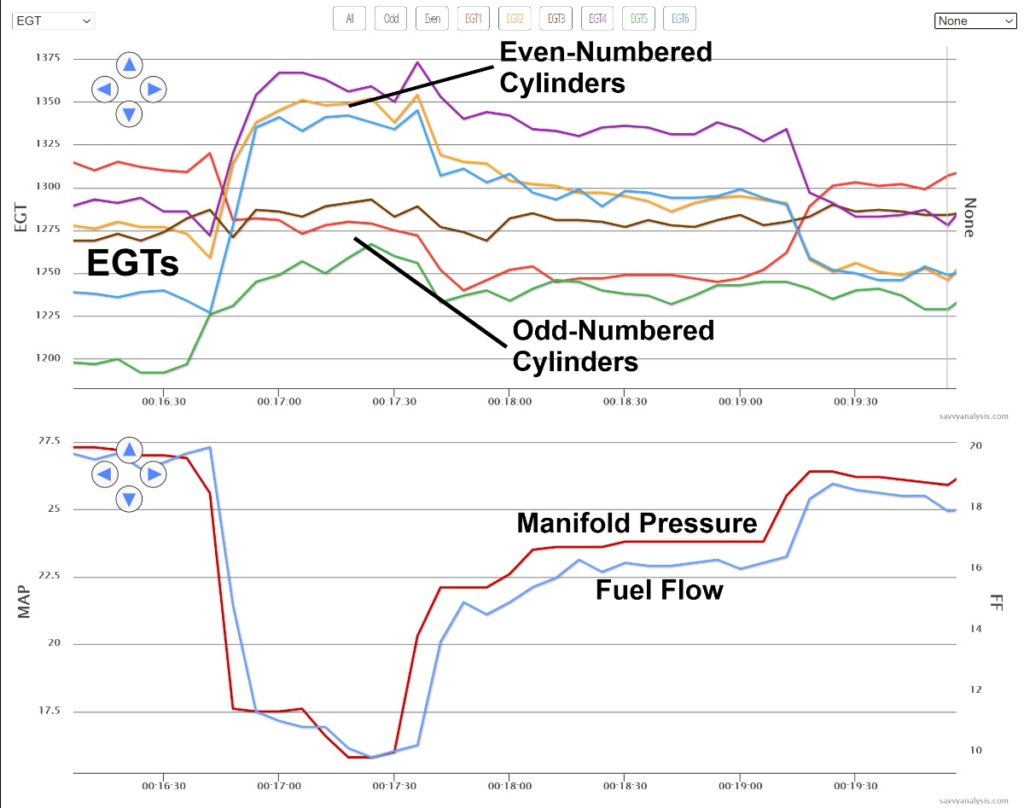
The engine experienced a rather profound loss of manifold pressure and fuel flow, lasting about a minute, after which things gradually normalized. This almost certainly corresponded to the vibration episode that Alvin had reported. But what could have caused it?
Ray spotted something interesting: During the “event” the EGTs of the left-bank cylinders (#2, #4, #6) shot up by 75-100 degrees Fahrenheit, while the EGTs of the right-bank cylinders (#1, #3, #5) remained basically unchanged. Something that affected half the cylinders but not the other half would certainly cause the engine to vibrate and run rough. But what could do that?
It couldn’t have been a sticking valve or clogged fuel nozzle or fouled spark plug, thought Ray, because those things would only affect one cylinder, not three. It couldn’t be a non-firing magneto, because that would affect all six cylinders and wouldn’t cause a big drop in MAP and FF.
Ray described what he was seeing in the data to Alvin. “There are only two things I can think of that could account for this,” Ray said. “One is a big leak in the left-side induction manifold, and the other is a significant obstruction in the left-side exhaust manifold. I suggest you focus on those two areas.”
Flame Cone!
A few days later, Alvin posted…
“As you suspected, no issues were found with either the propeller or the prop governor. Today, based on your suggestion, I shined a flashlight into the tailpipe of my Skylane and found a large piece of what appears to be perforated steel partially blocking the exhaust. I was able to fish it out and have attached pictures…”

“Do you think this type of exhaust blockage could cause manifold pressure and fuel flow to decrease?” asked Alvin. “Then perhaps the metal shifts position and everything goes back to normal?”
“I have ordered a new muffler that is due to be installed tomorrow, the inside of this one looks totally beat up. It was nice to find something, but I’m just not sure if this is the smoking gun I’ve been searching for. Let me know what you think.”
“Great catch,” said Ray. “I’m betting you’ve located the problem. That piece of perforated stainless steel is part of the muffler’s flame cone, and it’s clearly disintegrating quite badly. Often when that happens, the pieces are blown out of the tailpipe and don’t cause a problem. But if they get stuck the way yours did, it can cause excessive back-pressure and bring the engine to its knees. I’m certainly glad you were able to get a new muffler so quickly, and I’m betting it solves your problem. Please update me after you’ve test-flown the airplane with the new muffler.”
A subsequent Google search turned up FAA Advisory Circular 91-59A titled “: Inspection and Care of General Aviation Aircraft Exhaust Systems” which starts out this way:
Review of accident and incident reports reveal numerous fatalities and injuries to pilots and passengers as a result of exhaust system component failures. The following conditions can contribute to these accidents and incidents:
- Carbon monoxide (CO) poisoning,
- Partial or complete loss of engine power,
- and/or Fire.
As an example, we, the Federal Aviation Administration (FAA), received a safety recommendation concerning the internal failure of a muffler on a Cessna 207 airplane. The cone, which deflects or helps distribute exhaust gasses inside the muffler, came loose and blocked the exhaust gas outlet resulting in engine power loss during takeoff. This muffler configuration is common or similar to many other General Aviation (GA) airplane mufflers.
Case Closed
A week later…
“New muffler is in and the plane is running great again,” Alvin posted. “Here’s what we found when we cut open the old muffler…”
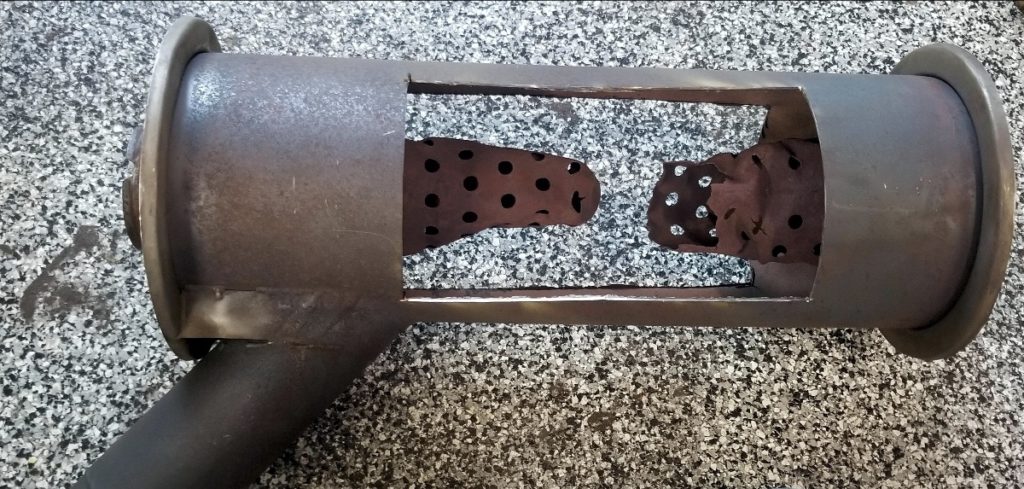
“I think this was also enough for the FAA to close the case.”
Maintenance has many facets, and troubleshooting is usually the most challenging of them. That’s doubly true when trying to troubleshoot an intermittent issue like the one Alvin faced, and triply true when the issue is one that only happens in the air and never on the ground.
Troubleshooting is essentially a process of elimination. It involves systematically ruling out possible causes until only one remains that must be the culprit. All too often, this is accomplished by “shotgunning”—removing and replacing components and hoping to get lucky. What happened with Alvin’s spark plugs, propeller and prop governor are good examples of this shotgun approach, sometimes also referred to as “throwing money at the problem.”
A better way is to gather as much data as possible and use it to guide and accelerate the search for the culprit. That’s a big part of what we do for SavvyAnalysis clients. It’s amazing how much our professional data analysts can learn by studying your engine monitor data. At a cost of just $129/year for a piston single like Alvin’s, it’s usually vastly less expensive than the traditional shotgun method…and a lot quicker, too.
If your plane is not enrolled in SavvyAnalysis, you don’t know what you’re missing.
You bought a plane to fly it, not stress over maintenance.
At Savvy Aviation, we believe you shouldn’t have to navigate the complexities of aircraft maintenance alone. And you definitely shouldn’t be surprised when your shop’s invoice arrives.
Savvy Aviation isn’t a maintenance shop – we empower you with the knowledge and expert consultation you need to be in control of your own maintenance events – so your shop takes directives (not gives them). Whatever your maintenance needs, Savvy has a perfect plan for you: