During every annual inspection, there’s a particular point in time when you and your IA need to sit down and make decisions.
Regular readers of this column know how strongly I feel about aircraft owners taking charge of their maintenance and managing the mechanics and shops they hire to work on their aircraft. An owner should never authorize any maintenance without first fully understanding the scope and detail of each proposed maintenance task to be done, and knows the answers to these questions:
- Why is this work being recommended?
- Is it an airworthiness issue?
- Is it required by regulation?
- Is it necessary for safety or dispatch reliability?
- How long will it take to accomplish?
- What will it cost?
- Are there any lower-cost alternatives?
- What’s the worst that could happen if it isn’t done?
The annual inspection is generally the most difficult time for an owner to exercise such management and oversight. It’s difficult for two reasons. First, when you put your aircraft in the shop for an annual inspection, you have no idea what sort of discrepancies will be found during the inspection. So you have no way of anticipating the extent, time and cost of the work.
Second, the aircraft is usually in the shop for quite a while at annual—typically a week or two, sometimes longer—and most owners don’t have the time or inclination to hang around the shop and oversee the work.
Despite these difficulties, the annual inspection is the most important time for you to exercise your management and oversight role. That’s because the annual is usually when the lion’s share of maintenance dollars are spent, and when there’s the greatest risk of misunderstandings, surprises, ruffled feathers, aggravation, sticker shock, disputes, litigation and other nasty manifestations that often occur when owners let the maintenance process get out of control.
One obvious way for you to manage and oversee the annual inspection is to do an owner-assisted annual. In fact, I strongly urge every aircraft owner to go through this experience at least once during their aircraft ownership career, because it’s such a marvelous and invaluable education. (I got my own start in aircraft maintenance 25 years ago by participating in an owner-assisted annual, never suspecting where that might lead.)
I recognize, however, that most aircraft owners are not in a position to do owner-assisted annuals on a regular basis. So short of taking time off from work and camping out at the maintenance shop, how can you stay in control? Before I try to answer that question, let’s take a moment to review exactly what goes on at the shop when you bring your aircraft in for its annual inspection.
Anatomy of an Annual
The ritual that aircraft owners refer to as the “annual” involves quite a bit more than just the inspection required by FAR 91.409 whose scope is defined by FAR Part 43 Appendix D (“Scope and detail of annual and 100-hour inspections”). It also involves preparing the aircraft for inspection, repairing unairworthy items and other discrepancies uncovered by the inspection, performing normal once-a-year preventive maintenance, and doing a considerable amount of paperwork.
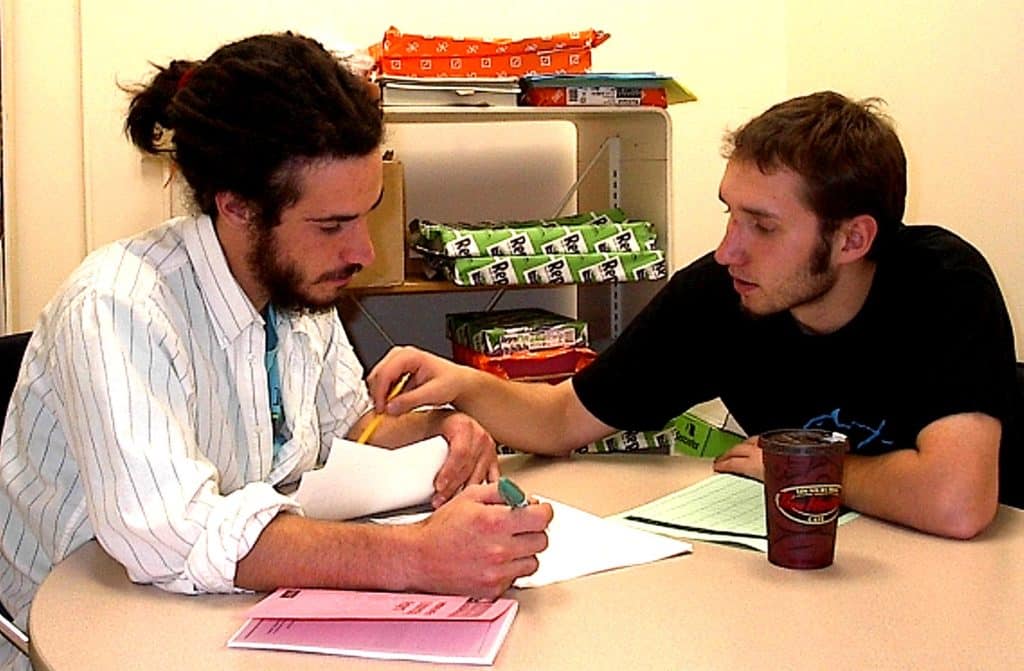
There are eight distinct steps in this annual ritual:
Step 1: Open the aircraft. The aircraft is prepared for inspection by removing inspection plates, cowlings, spinners, fairings, seats, carpets, floorboards, trim panels and anything else necessary to expose the guts of the airframe and engine. On retractable-gear aircraft, this often involves disconnecting gear doors and positioning jacks to ready the aircraft for the gear swing and rigging checks. This step might take perhaps a day for a fixed-gear single, a day and a half for a retractable single, and two days or more for a twin.
Step 2: Inspect the aircraft. This is the actual inspection as mandated by the FARs. It must be done personally by an authorized inspector, usually an A&P mechanic who holds an FAA Inspection Authorization (colloquially, an “IA”). The inspection might take a half-day for a fixed-gear single, a full day for a retractable single, perhaps as much as two days for a twin.
Step 3: Inspect the maintenance records. The IA is also required to research the aircraft maintenance records each year to determine whether it is in compliance with all applicable Airworthiness Directives (ADs) and airworthiness limitations, and whether any new or recurrent ADs or other required inspections (such as biennial altimeter and transponder certs) are due. This phase can take minutes or hours, depending on whether the aircraft maintenance records are complete and well organized. (I remember performing one annual inspection where the records were such a mess that this phase took longer than inspecting the aircraft.) I recommend a recordkeeping system called “adlog” (www.adlog.com) that IAs love because it makes this research a snap, and I use this system for my own airplane.
Step 4: Create a list of discrepancies. When the IA has finished inspecting the aircraft and its paperwork, he prepares a list of unairworthy items and other discrepancies. In preparing this list, the IA should identify which discrepancies he considers unairworthy (i.e. must be corrected before the aircraft can be approved for return to service) and which he considers discretionary (i.e. may be fixed or deferred at the owner’s discretion).
Step 5: Repair the discrepancies. This is the “variable portion” of the annual ritual, and there’s no good way to predict how long it will take until the inspection is done and the discrepancy list is in hand. Some years you luck out and get off easy, while others involve one or more heavy or costly repairs.
Step 6: Perform preventive maintenance. Although not technically required by regulation, the annual ritual usually includes a bunch of standard preventive maintenance tasks like changing the oil and filter, cleaning and gapping the spark plugs, greasing the wheel bearings and landing gear retraction mechanism, servicing the battery, changing or cleaning fuel and air filters and so forth. This is typically a day or two of work, depending on the aircraft.
Step 7: Close the aircraft. At this point, it’s time to put the aircraft back together— reinstalling all the stuff that was removed at the beginning. As with the opening step, you can figure on between a half-day and two days of work, depending on the complexity of the aircraft.
Step 8: Make the logbook entries. The final step is for the IA to make the required entries in the aircraft maintenance records. These entries document all the maintenance performed, memorialize the annual inspection and include a signed statement by the IA that the aircraft has been found airworthy and is approved for return to service.
The Decision Point
There is a crucial point in this process when you need to get involved. I call it “the decision point” because it’s the point when critical decisions are made that affect what work will be done, what parts will be purchased and what you will wind up paying to get the annual signed off and the aircraft back in the air.
The decision point occurs between Step 4 (when the IA creates the discrepancy list) and Step 5 (when the discrepancies are repaired). At this critical juncture, it is essential for you to sit down with the IA and go over the discrepancy list point by point.
You should require the IA or shop to provide a detailed written estimate of what it will cost (both parts and labor) to correct each discrepancy, and you should discuss which items must be addressed right away and which could be prudently deferred.
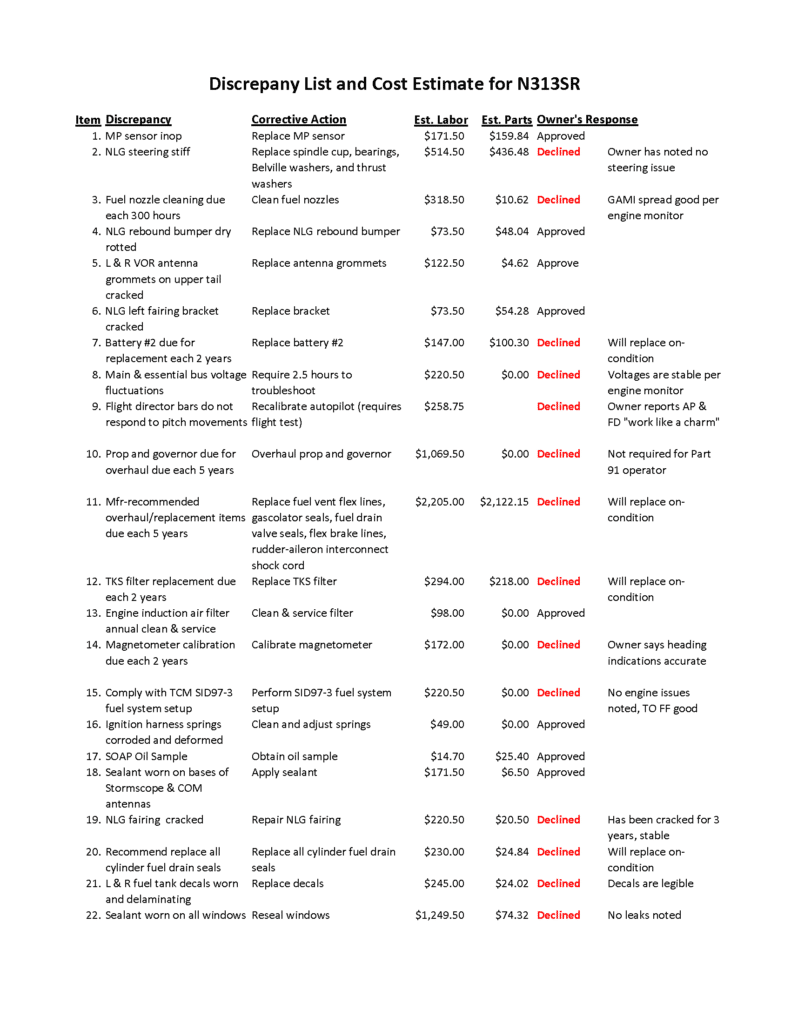
At the conclusion of this meeting, you and the IA should jointly agree on a plan of action, and be sure that you are on the same page concerning exactly what repairs will be made, what replacement parts will be ordered and what those repairs and replacement parts will cost. Your decision about which recommended repairs you wish to approve and which you wish to decline or defer needs to be put in writing so there’s no possibility of confusion or misunderstanding.
There must also be a clear agreement by your IA that should unforeseen contingencies arise that could have significant impact on the agreed-to cost and schedule, the shop will not proceed without first informing you and obtaining your explicit authorization to proceed. That should be in writing, too.
Although it’s usually best to accomplish this in a face-to-face meeting between you and your IA, it can be done via email or fax if necessary. However, I recommend against trying to do it over the telephone, because without a written record it’s just too easy for miscommunication to occur. If you do communicate with your IA verbally, you should immediately memorialize the conversation in writing and provide your IA with a copy.
This kind of involvement at the decision point is the best way I know to ensure that you remain in control of the maintenance process and have the information necessary to manage and oversee it. It goes a long way toward eliminating misunderstandings, unwelcome surprises, and unpleasant disputes. The most professional IAs and shops insist on having the customer come in for a conference at the decision point, but at most shops this will not occur unless the owner insists on it and takes steps to ensure it happens.
You need to make sure that your IA completes the inspection phase before starting any repairs. Beware of the phenomenon I like to describe as “inspect a little, repair a little, lather, rinse, repeat.” Some IAs like to make repairs as they go through the inspection, but when they do that it deprives you of a well-defined decision point and invariably you lose control of the situation. So it’s essential for you to avoid this like the plague.
Consequently it is very wise to give your shop explicit instructions when you bring them your aircraft for the annual, along the following lines:
“I’m authorizing you to open the airplane, perform the inspection and prepare the discrepancy list. However, do not perform any repairs or order any parts until we go over the discrepancy list together and jointly decide on a plan of action. Please let me know as soon as you are ready for me to come in to do this, and make sure you have detailed written estimates prepared for each recommended repair and other maintenance items so I know how much each is expected to cost and can make an informed decision about what work to approve and what to decline or defer.”
You bought a plane to fly it, not stress over maintenance.
At Savvy Aviation, we believe you shouldn’t have to navigate the complexities of aircraft maintenance alone. And you definitely shouldn’t be surprised when your shop’s invoice arrives.
Savvy Aviation isn’t a maintenance shop – we empower you with the knowledge and expert consultation you need to be in control of your own maintenance events – so your shop takes directives (not gives them). Whatever your maintenance needs, Savvy has a perfect plan for you: