Contrary to popular belief, more maintenance isn’t necessarily better. Often it’s worse—a lesson that was learned during WWII.
I’ve written at length in prior issues of EAA Sport Aviation on the subject of Reliability-Centered Maintenance (RCM), the scientific and engineering discipline of designing optimum maintenance programs to provide the highest levels of safety and reliability at the lowest cost. RCM originated in the late 1960s from the work of Stanley Nowlan and Howard Heap at United Airlines, and quickly became the “bible” for how maintenance was done throughout the air transport industry. RCM was adopted by the U.S. military beginning in the mid-1970s, by the U.S. commercial nuclear power industry in the 1980s, and by many other industries in the 1990s.
Today, RCM is the way maintenance is done in all segments of aviation except one: general aviation. Actually, RCM is now being widely adopted in high-end GA—at the Citation X, Gulfstream, Challenger and Global Express level—but not yet at the low end of the aviation food chain where most of us hang out. (One of my missions is to change that.)
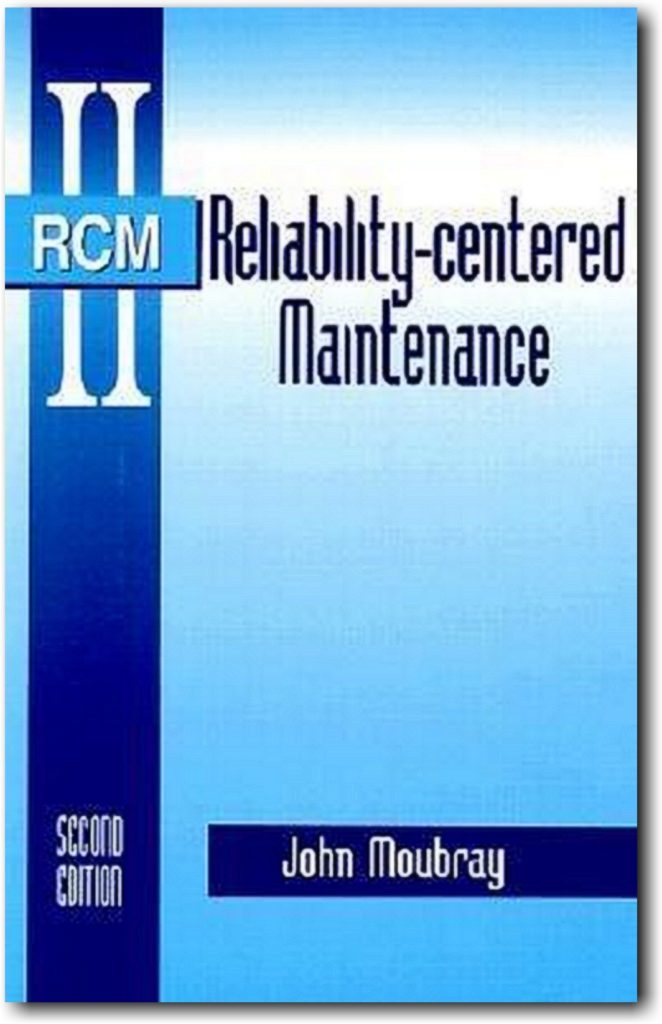
RCM Principles
Fifty years ago, in the 1960s (when I first became a pilot and aircraft owner), aviation maintenance was predicated on the belief—held almost universally by the aeronautical engineers and maintenance experts of that era—that every aircraft, subsystem and component had a predictable “useful life” during which it could be expected to operate reliably, and after which it needed to be replaced or overhauled in order to prevent failures. (Many GA mechanics and aircraft owners still believe this to be true.)
However, research conducted by the airlines in the late 1960s—notably the work of Nowlan and Heap at UAL—demonstrated that this belief was flat wrong in almost every instance they investigated. This resulted in a paradigm shift in the way maintenance was done in the air transport industry. The new RCM way of thinking about maintenance included:
- understanding that the vast majority of failures are not age-related, and that a very large number of them are either infant mortality or maintenance-induced;
- changing from efforts to predict life expectancies to trying to manage failures;
- shifting from fixed-interval, time-directed maintenance to on-condition maintenance;
- eliminating most TBOs and life limits in favor of condition monitoring and failure prediction; and
- recognizing that that many component and subsystem failures have acceptable consequences, and that “run to failure” is often the best maintenance strategy.
The shift from traditional to RCM-inspired maintenance in the late 1960s and early 1970s was a watershed event. It resulted in massive reductions in maintenance expenditures and scheduled downtime by eliminating most TBOs and life limits and slashing both the amount and frequency of preventive maintenance. To the astonishment and disbelief of most maintenance experts of the time, component failures and unscheduled downtime plummeted.
This defied the conventional wisdom of the time. How could it possible that by doing less preventive maintenance to the aircraft, it actually becomes more reliable?
WWII Operations Research
It turns out that this seemingly counterintuitive result was first discovered during World War II, more than 20 years before Nowlan and Heap did their pioneering RCM studies at UAL. I was completely unaware of this until recently when Colleen Keller, a professional military operations analyst (and Cessna Cardinal owner) emailed me a fascinating paper written by Professor James P. Ignizio of the University of Texas that appeared in the September 2010 issue of Phalanx, the quarterly journal of the Military Operations Research Society (MORS).
In his paper, Professor Ignizio cited the little-known work of a gifted British scientist named Conrad Hal (C.H.) Waddington (1905-1975), who was a developmental biologist, paleontologist, geneticist, and embryologist—certainly a rather unlikely person to make major contributions to the field of aircraft maintenance. During the War, however, Waddington’s career in biology was temporarily interrupted when he became involved in operations research for the Royal Air Force Coastal Command.
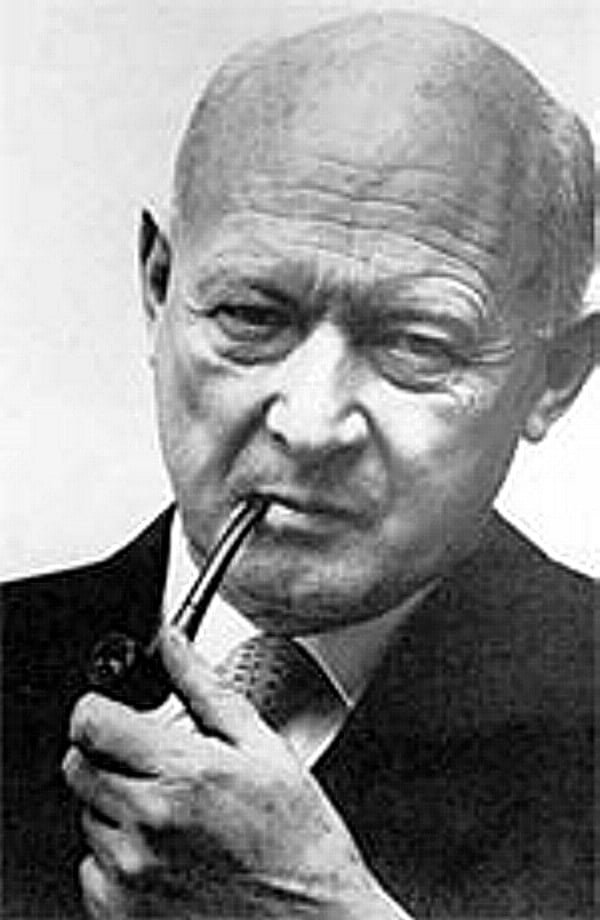
The principal assignment of Waddington and his fellow scientists in the Coastal Command Operational Research Section (CC-ORS) was to advise the British military on how they could more effectively combat the threat from German submarines. Waddington and his colleagues developed a series of astonishing recommendations that defied military conventional wisdom.
For example, the bombers used to hunt and destroy U-boats were mostly painted black. At the suggestion of CC-ORS, a test was run to determine the best color to camouflage the aircraft, and it turned out that bombers painted white were not spotted by the U-boats until they were 20% closer, resulting in a 30% increase in successful sinkings. Waddington’s group also issued a recommendation that the depth charges dropped by the bombers be set to explode at a depth of 25 feet instead of 100 feet. This recommendation, initially resisted strongly by RAF commanders, ultimately resulted in a sevenfold increase in the number of U-boats destroyed.
Waddington subsequently turned his attention to the problem of what today would be called “force readiness.” Specifically, the RAF’s B-24 “Liberator” bombers were spending an inordinate amount of time in the maintenance shop, both for scheduled preventive maintenance and for unscheduled resolution of what the British called “breakdowns” or “downs” or “gripes” and that we’d call “squawks.” Obviously, the more time bombers spent in the shop, the less time they could spend hunting and killing U-boats. As Professor Ignizio put it:
“In July 1943 the two British Liberator squadrons located at Ballykelly, Northern Ireland, consisted of approximately 40 aircraft. However, at any given time only about 20 of these were flight ready. Aircraft were down for any number of reasons, but mostly as a consequence of undergoing or awaiting maintenance—either scheduled or unscheduled—or perhaps waiting for maintenance personnel or spare parts. Conventional wisdom held that if more preventive maintenance events were performed on each aircraft, fewer problems would exist—and potential problems could be caught and fixed—and thus the effectiveness of the fleet would surely improve. Conventional wisdom was, as is so often the case, wrong. It would take H.C. Waddington and his Operational Research team to prove just how wrong.”
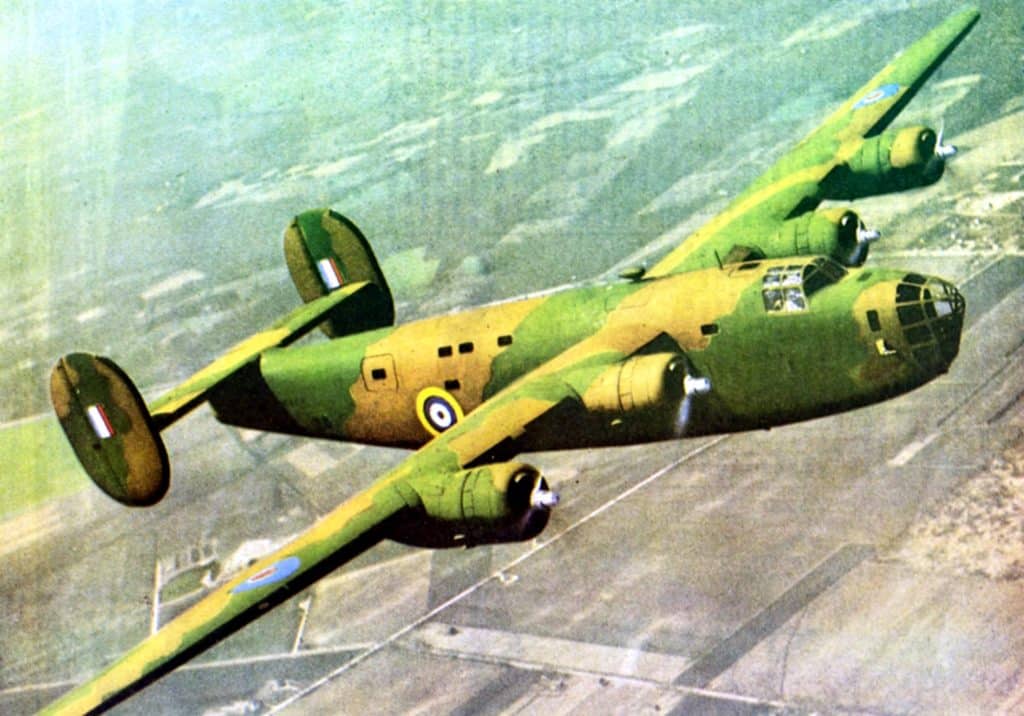
Waddington and his team started gathering data about the scheduled and unscheduled maintenance of these aircraft, and began crunching and analyzing the numbers. When they plotted the number of unscheduled aircraft repairs as a function of flight time, they discovered something both unexpected and significant: Such unscheduled repairs increased sharply immediately after each scheduled 50-hour maintenance event, then declined steadily over time until the next scheduled 50-hour maintenance, at which time they spiked once again.
Waddington Effect
When Waddington examined the plot of this repair data, he concluded that the scheduled maintenance (in Waddington’s own words):
“…tends to increase breakdowns, and this can only be because it is doing positive harm by disturbing a relatively satisfactory state of affairs. Secondly, there is no sign that the rate of breakdown is beginning to increase again after the 40-50 flying hours, when the aircraft is coming due for its next [scheduled preventive maintenance event].”
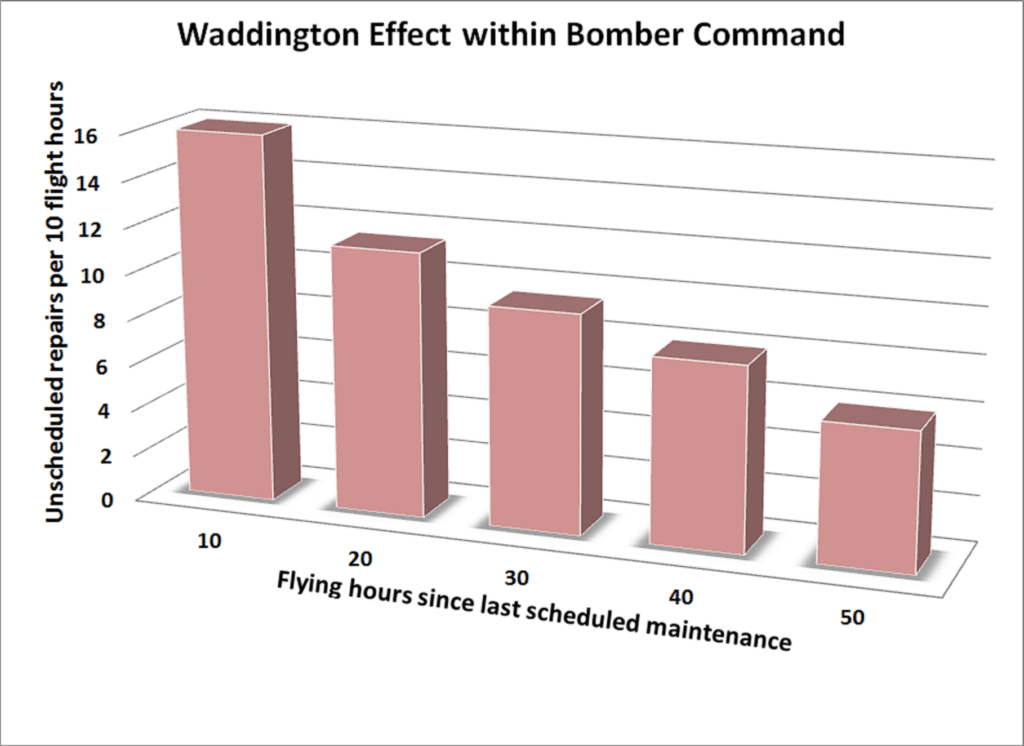
In other words, the observed pattern of unscheduled repairs—dubbed “the Waddington effect” by Professor Ignizio—demonstrated that:
- the scheduled maintenance was actually doing more harm than good; and
- the 50-hour scheduled maintenance interval was inappropriately short.
The solution proposed by Waddington’s team—and ultimately accepted by the RAF—was the development of an improved maintenance program that:
- increased the time interval between scheduled maintenance events;
- eliminated preventive maintenance tasks that were not demonstrably beneficial;
- improved the scheduling of maintenance personnel; and
- created better, clearer maintenance guidance and documentation.
Once these recommendations were implemented, the number of effective flying hours of the British Coastal Command bomber fleet increased by more than 60%.
Fast Forward
Two decades later, two other gifted scientists, aeronautical engineer Stanley Nowlan and mathematician Howard Heap at United Airlines, rediscovered these same principles in their epic work on Reliability-Centered Maintenance that changed the face of how maintenance is performed in air transport, military aviation, high-end GA, and numerous industrial applications outside aviation. Ironically, Nowlan and Heap were almost certainly unaware of the work done by H. C. Waddington and his colleagues at the British Coastal Command Operational Research Section, because their work was classified. It remained so until 1973, when Waddington’s meticulously kept diary of his wartime research activities was finally declassified and published under the title Operational Research in World War II by Elek Science [ISBN 023615463X].
Every aircraft owner and aviation maintenance technician would do well to heed the lessons learned about preventive maintenance through the brilliant, insightful research of Waddington, Nowlan and Heap. More preventive maintenance isn’t necessarily better. Often it’s worse.
You bought a plane to fly it, not stress over maintenance.
At Savvy Aviation, we believe you shouldn’t have to navigate the complexities of aircraft maintenance alone. And you definitely shouldn’t be surprised when your shop’s invoice arrives.
Savvy Aviation isn’t a maintenance shop – we empower you with the knowledge and expert consultation you need to be in control of your own maintenance events – so your shop takes directives (not gives them). Whatever your maintenance needs, Savvy has a perfect plan for you: