They can be deadly if the pilot hasn’t been taught what to do
The release of my book Mike Busch on Engines prompted lots of reader correspondence. One particularly interesting email came from the owner of a 2007 Cessna Turbo Stationair (T210H)—I’ll call him Chuck—based in Aspen, Colorado:
I am terrified of the turbocharger. There have been several fatal accidents in Cessna T206s and T210s caused by turbocharger failures. Worse, there does not seem to be any way to determine the condition of the turbocharger or wastegate other than visual inspection during an annual. Even then, it doesn’t seem as if we can tell much about turbocharger condition by simple visual inspection.
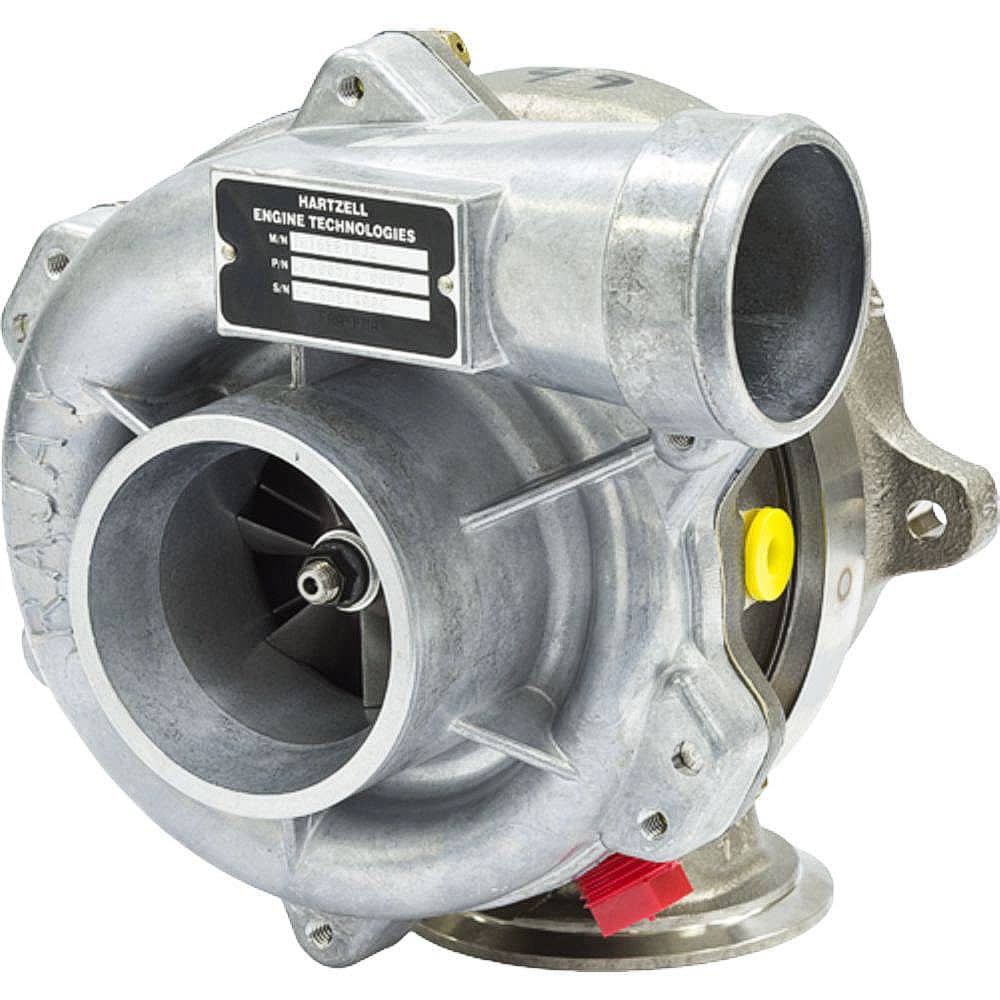
I replied to Chuck that I’d been flying behind turbocharged engines for more than 30 years and that a turbocharging system was nothing to be frightened of, provided that it’s inspected and maintained conscientiously. I added that I had personally experienced an in-flight turbosystem failure in my own airplane several years ago and that it was no big deal: The engine simply reverts to being normally-aspirated.
Chuck offered his opinion that at least two fatal Lycoming-powered T206 accidents involving turbocharger failure may have been caused by engine stoppage due to an excessively rich mixture. He quoted the Emergency Procedures section of his T210H Pilot Operating Handbook:
If the turbocharger failure results in power loss, it may be further complicated by an overly rich mixture. This rich mixture condition may be so severe as to cause a total power failure. Leaning the mixture may restore partial power.
This is spot-on, of course. The turbocharger is an exhaust-driven air pump that pumps pressurized air into the engine. If the turbocharger fails, the engine gets less air—and therefore needs less fuel to maintain a combustible mixture. Therefore, the pilot may have to pull back on the red knob to maintain engine power after the loss of turbocharging. This is true of any turbocharged engine, but it’s especially true of turbocharged Lycoming engines because of the design of the RSA fuel injection system used by those engines.
The problem is that we pilots typically receive primary training in normally aspirated airplanes. During that training, a CFI pounds into our heads that in event of a power loss, we should shove the mixture to full-rich, turn on the electric boost pump (if available), and switch tanks (if possible). That’s exactly the right thing to do in the event of an engine failure caused by fuel starvation or exhaustion.
But it’s precisely the WRONG thing to do in the case of turbocharger failure. If the turbocharger fails, the engine will be running too rich. Shoving the red knob forward and/or turning on the boost pump will only make it richer (and unhappier). We need to lean the mixture to restore power, something that’s the very the opposite of what our CFIs taught us to do long ago.
NTSB recommendation
Chuck’s email referenced two specific NTSB accident reports. The first (LAX92FA092) described the January 1992 crash of a Cessna T210L in Temple, Arizona:
The pilot said that during descent from 10,500 feet the manifold pressure dropped to 18 inches. He decided to land at a nearby airport. While diagnosing the problem, he turned on the boost pump and the engine lost more power. The cockpit began to fill with smoke. The pilot secured the engine and turned the electrical system off. He began a power-off descent over the airport and manually extended the landing gear. He thought he was too high, so he turned the battery on to lower the flaps. With electric power restored, the landing gear returned to the up position. The pilot again lowered the landing gear. Unable to reach the runway, he tried to re-start the engine on final approach, but did not have enough time. Subsequently, the aircraft impacted an up-slope about 300 feet short of the runway and crashed.
An examination of the turbocharger revealed the turbine shaft failed due to multiple fatigue cracks. About 125 flight hours before the failure, the turbine shaft had been reworked (ground and chromium-plated), but not in accordance with the manufacturer’s specifications. Turbocharger malfunction was not addressed in the POH.
Cessna’s POH for the T210 did not address turbocharger failure in its Emergency Procedures section. To restart the engine after a power loss, the POH explicitly directs the pilot to advance the mixture control to the rich position if restart does not occur. The NTSB determined the probable cause of this accident was:
Fatigue failure of the turbocharger’s turbine shaft due to inadequate maintenance, and the pilot’s improper in-flight planning/decision after experiencing a turbocharger failure. A factor related to the accident was the lack of information in the pilot operating handbook concerning turbocharger failure or malfunction.
The Temple, Arizona accident resulted in two fatalities and three serious injuries, and prompted the NTSB to issue Safety Recommendation A-94-81 asking the FAA to “require the amendment of pilot operating handbooks and airplane flight manuals applicable to aircraft equipped with engine turbochargers by including in the “Emergency Procedures” section information regarding turbocharger failure. The information should include procedures to minimize potential hazards relating to fire in flight and/or loss of engine power.”
In its July 1995 response to the NTSB, the FAA stated that it agreed with the intent of this Safety Recommendation but did not believe there was sufficient basis to issue an Airworthiness Directive requiring POHs and AFMs of turbocharged aircraft to be amended. The FAA did agree to require manufacturers to include turbocharger failure information in new AFMs going forward. In 1998, Cessna issued a “safety supplement” that addresses in-flight turbocharger failure.
Then, in January 2007, a 1999 Cessna T206H (same model as Chuck’s but eight years older) experienced a fatal crash near Homer Glen, Illinois after its turbocharger failed:
The 1999 Cessna T206H was operated as a public aircraft when the pilot reported a loss of engine power during cruise flight about 1,150 feet above ground level. … Witnesses reported that they heard several attempted engine restarts while the airplane was being positioned for a forced landing on a 500-foot long fallow agricultural field north of a house. A witness reported that black smoke would emanate from the airplane during each start attempt. The airplane’s wing and horizontal stabilizer contacted trees near the house resulting in a steep descent into the garage adjacent to the house. A post-crash fire/explosion then ensued. The A&P Mechanics Handbook states that a mixture “too rich” is indicated by black smoke.
Examination of the airplane systems and related components revealed that the turbocharger could not be rotated, and a hydraulic press was utilized to effect the removal of the turbocharger turbine wheel. The engine crankcase halves exhibited fretting, and the nut of one crankcase thru-bolt was not in place. Maintenance records indicate that the crankshaft was replaced in response to airworthiness directives and service bulletins. No other anomalies that would have precluded normal operation were found.
In 1994, the National Transportation Safety Board issued recommendation A-94-81 relating to emergency procedures for turbocharger failures to be included in airplane pilot operating handbooks (POHs) and airplane flight manuals. The Cessna T206H POH does not list emergency procedures for turbocharger failures. The Cessna T206H POH states, under emergency procedures, to advance the mixture control to the rich position if restart does not occur.
The manufacturer’s airplane pilot safety supplement, which was reissued in 1998 to incorporate turbocharger failures, states that “If a turbocharger failure results in a loss of power, it may be further complicated by an overly rich mixture.”
The pilot, who was the sole occupant of the T206H, was fatally injured. The NTSB determined the probable cause of this accident was:
The seized turbocharger, the altitude/clearance not maintained/obtained during approach to a forced landing on an agricultural field, and the unsuitable landing area encountered by the pilot. Contributing factors were the inadequate emergency procedures by the manufacturer, the trees, and the residential area.
FAA response (?)
On June 30, 2004, the FAA issued an Airworthiness Concern Sheet (ACS) applicable to turbocharged Cessna airplanes: T182, T-R182, T206, T207, P210, T210, T303, T310, 320, T337, 340, 401, 402, 411, 414, 421. The ACS states that engine power loss or engine stoppage can be exacerbated due to the fuel mixture becoming excessively rich following the failure of the turbocharger system. It further states that the POH may not contain adequate instructions to cope with in-flight turbocharger system failure. Additionally, the aircraft maintenance instructions may not adequately address the turbocharger system performance to detect an impending failure.
Although the issuance of an ACS by the FAA often portends that an AD will follow, that was not the case in this instance. It also strikes me as odd that the FAA would single out turbocharged Cessna singles and twins in the ACS, since this issue is quite generic for all turbocharged Continental and Lycoming engines and doesn’t care about what airframes they’re mounted in.
In June 2012, the NTSB finally threw up its hands and classified Safety Recommendation A-08-21 as “Closed/Unacceptable Action” based on the FAA’s decision not to take the action recommended by the NTSB. In its classification letter, the NTSB stated it “remains concerned that, without the establishment of an FAA requirement, manufacturers of aircraft equipped with turbochargers still have not voluntarily included emergency procedures for turbocharger failures, and as a result, accidents and incidents continue to occur.”
Diagnosing a turbocharger failure
In his email to me, Chuck asked me how a pilot experiencing power loss “can determine in a couple of seconds if he has had a fuel interruption problem (requiring boost pump and rich mixture) or a turbocharger failure (requiring leaning the mixture and no boost pump).” That is, of course, precisely the question that POHs should be addressing (but don’t).
My answer to Chuck was straightforward: A turbosystem failure results in a significant uncommanded loss of manifold pressure—with a concomitant perceptible loss of power—before the engine quits. A fuel interruption doesn’t do that—the engine just quits suddenly without warning (as anyone who has ever run a tank dry can attest). Furthermore, an engine that quits because of a turbocharger failure continues to indicate fuel flow (too much, actually), while one that quits because of a fuel interruption indicates zero fuel flow. Thus, there should no ambiguity between turbosystem failure and a fuel system failure if the pilot is paying attention. An unexplained loss of manifold pressure in a turbocharged engine plus the presence of fuel flow should be always be treated as a turbosystem failure.
The question of how to respond to a turbosystem failure is a bit more complicated. There are lots of things that can cause the turbosystem to fail. Most of them are reasonably harmless if the situation is properly handled by the pilot, but one possible cause—a breach of the exhaust system—can be extremely serious and result in a pilot’s worst nightmare: an in-flight fire.
Therefore, in a turbocharged piston twin (like the Cessna T310R that I fly), an unexplained and uncommanded loss of manifold pressure plus continued fuel flow indication should provide the pilot good cause to shut down the engine in an abundance of caution, and then make a single-engine precautionary landing as soon as practicable. That’s precisely what I did when my right engine suffered a turbosystem failure in July 2014 while overflying Las Vegas, Nevada at 13,000 feet. As it happened, there was no exhaust system breach so the engine shutdown was arguably unnecessary, but I had no way of knowing that at the time I had to make my in-flight decision.
In a single-engine turbocharged airplane (like Chuck’s Cessna T206H), shutting down the engine is not usually a viable option. The appropriate action is to restore partial (normally-aspirated) power to the engine by leaning the mixture, and then land as soon as practicable using the minimum power necessary to accomplish that.
Oh, and if you’re a CFI who has students who fly turbocharged airplanes, you really need to be teaching them this stuff. It just might save their lives someday.
You bought a plane to fly it, not stress over maintenance.
At Savvy Aviation, we believe you shouldn’t have to navigate the complexities of aircraft maintenance alone. And you definitely shouldn’t be surprised when your shop’s invoice arrives.
Savvy Aviation isn’t a maintenance shop – we empower you with the knowledge and expert consultation you need to be in control of your own maintenance events – so your shop takes directives (not gives them). Whatever your maintenance needs, Savvy has a perfect plan for you: