It’s riskier business than most owners or A&Ps realize.
Regular readers of this column know how I feel about changing cylinders in the field. I hate it. Especially when several cylinders are changed at one time; this is risky business. Changing them all (the so-called “top overhaul”) is even riskier.
In my column in the June 2014 issue (“Cylinder Work: Be Afraid”), I explained the nature of the risk: Changing cylinders involves messing with the ultra-critical clamping force (“preload”) of critical threaded fasteners. And it’s extremely difficult to ensure that the correct preload is achieved when tightening those fasteners with a torque wrench, even if the manufacturer’s procedures are followed to the letter.
A couple of recent NTSB Probable Cause reports illustrate this issue rather vividly. Both of these reports were literally hot off the press as I’m writing this column. I offer them here without comment, because they speak for themselves.
Spun bearing, broken crankshaft
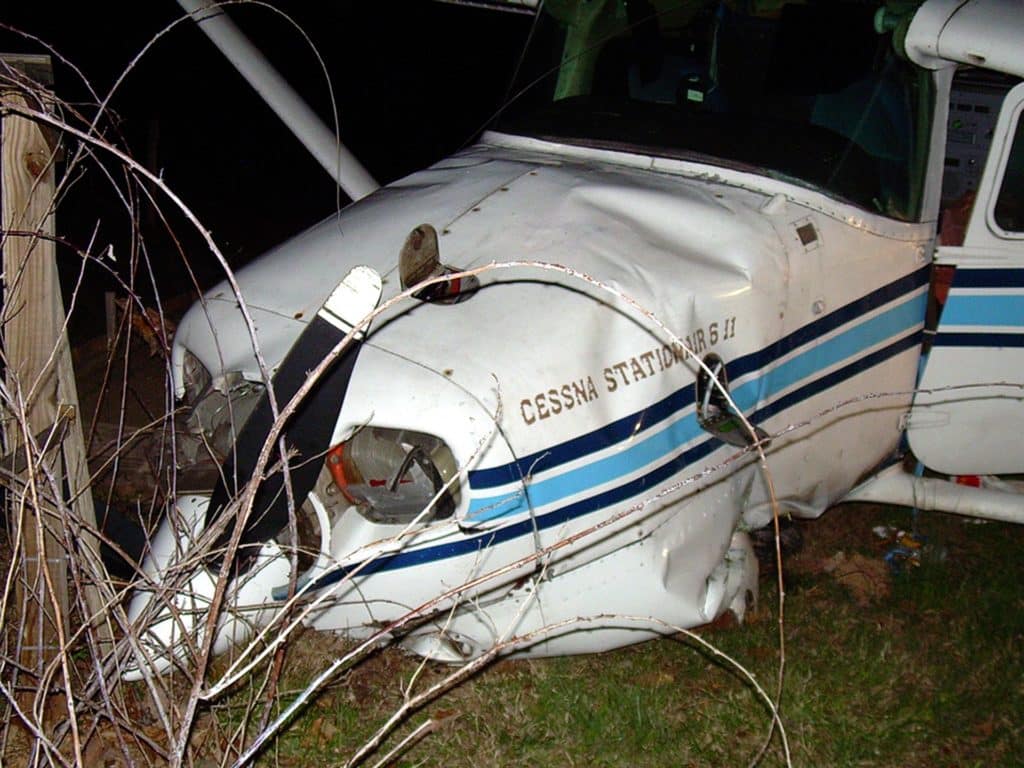
NTSB Identification: ERA14LA193
Accident occurred: Friday, April 11, 2014 in Louisa, VA
Probable Cause Approval Date: 04/27/2015
Aircraft: CESSNA U206G, registration: N156SA
Injuries: 1 Serious, 1 Minor.
Narrative: The pilot reported that, during the flight before the accident flight, he noted that the oil pressure was slowly fluctuating, so he chose to change the engine oil and filter. Airport personnel provided the supplies and observed the pilot perform the maintenance. The pilot removed and then opened the oil filter and “an excessive amount of metal” was observed. The pilot’s mechanic had replaced four cylinders about 4 months earlier, and the pilot assumed that the metal was chrome from the overhauled cylinders and was the result of “break-in.” Although airport personnel expressed concerns about the metallic debris, the pilot chose to finish the oil change and continue with his next flight. About 30 minutes after departure, the engine made “a strange sound,” and it lost power about 20 seconds later. The pilot conducted a forced landing, and the airplane landed hard in an open field, which resulted in structural damage to the airframe.
Disassembly and examination of the engine revealed that the engine cylinder through bolts on the Nos. 1 through 5 cylinders were significantly undertorqued. The crankshaft was fractured near the No. 2 main bearing. The areas adjacent to the No. 2 bearing on the inside of the engine case exhibited rotational scoring, indicating that bearing movement had occurred before the crankshaft failure. The Nos. 1 and 3 main bearings also exhibited evidence that bearing movement had occurred before the engine failure. It is likely that the mechanic did not properly torque the through bolts when he replaced the four cylinders, which allowed the bearings to move and led to the eventual failure of the crankshaft.
Probable cause: The National Transportation Safety Board determines the probable cause(s) of this accident as follows:
The pilot’s decision to continue operation of the airplane with known mechanical issues (fluctuating oil pressure and metal in the oil filter), which was the result of undertorqued cylinder through bolts. Contributing to the accident was the mechanic’s failure to properly torque the engine through bolts, which led to the eventual failure of the crankshaft.
Cylinder separated from engine
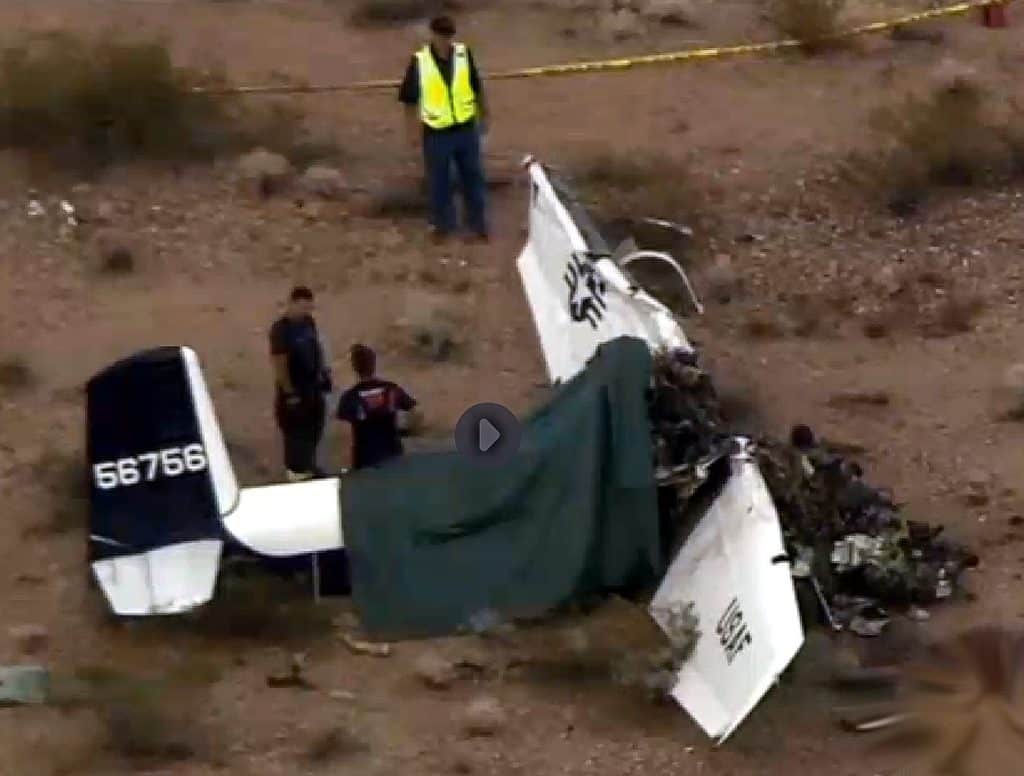
NTSB Identification: WPR13FA284
Accident occurred: Sunday, June 23, 2013 in Boulder City, NV
Probable Cause Approval Date: 04/27/2015
Aircraft: BEECH A45 [T-34 Mentor], registration: N434M
Injuries: 2 Fatal.
Narrative: The pilot, who was also the mechanic for the airplane, had replaced all six cylinders on the engine during the airplane’s annual inspection; he reported that, 3 days before the accident, the engine was operated and ran well. On the day of the accident, he was returning the airplane to its home base following a maintenance inspection on the wings. The pilot was near the end of the flight when he contacted approach control and requested priority handling because an engine chip light had illuminated. Shortly thereafter, the pilot stated that the engine had lost power on a cylinder, and he declared an emergency. When the airplane was at 9,500 ft mean sea level, the pilot said that he was going to attempt to land at a nearby airport (elevation 2,201 ft). Before switching to the airport’s common traffic advisory frequency (CTAF), the pilot reported to the approach controller that the airplane was at 3,800 ft with the landing gear down and that the situation was under control. The pilot did not contact approach control again and did not broadcast over the CTAF. The airplane collided with terrain in a nose- low attitude about 1 mile west of the airport.
Postaccident examination of the airframe revealed no evidence of mechanical anomalies that would have precluded normal operation.
Postaccident examination of the engine revealed that the No. 6 cylinder had separated, and no nuts were located on its through bolts. Magnified examinations of the bolt threads found the thread profiles intact and only locally distorted, consistent with the nuts not being present during the No. 6 cylinder separation, which appeared to be the result of the incorrect assembly of the cylinder at the last cylinder change. Fretting damage on the mounting pad was observed, which indicates looseness and movement between the cylinder and the case that resulted from inadequate preload in the fasteners either through insufficient initial torque or loss of torque during operation. Considering the short time since cylinder installation, it is likely that the cylinder fasteners, or at least some of them, were not correctly torqued at installation.
Probable cause: The National Transportation Safety Board determines the probable cause(s) of this accident as follows:
The pilot/mechanic’s loss of control during an emergency descent following a loss of engine power while in cruise flight. Contributing to the accident was the pilot/mechanic’s incorrect assembly of the No. 6 cylinder at the last cylinder change, which resulted in a separation of the cylinder and the loss of engine power.
Takeaways
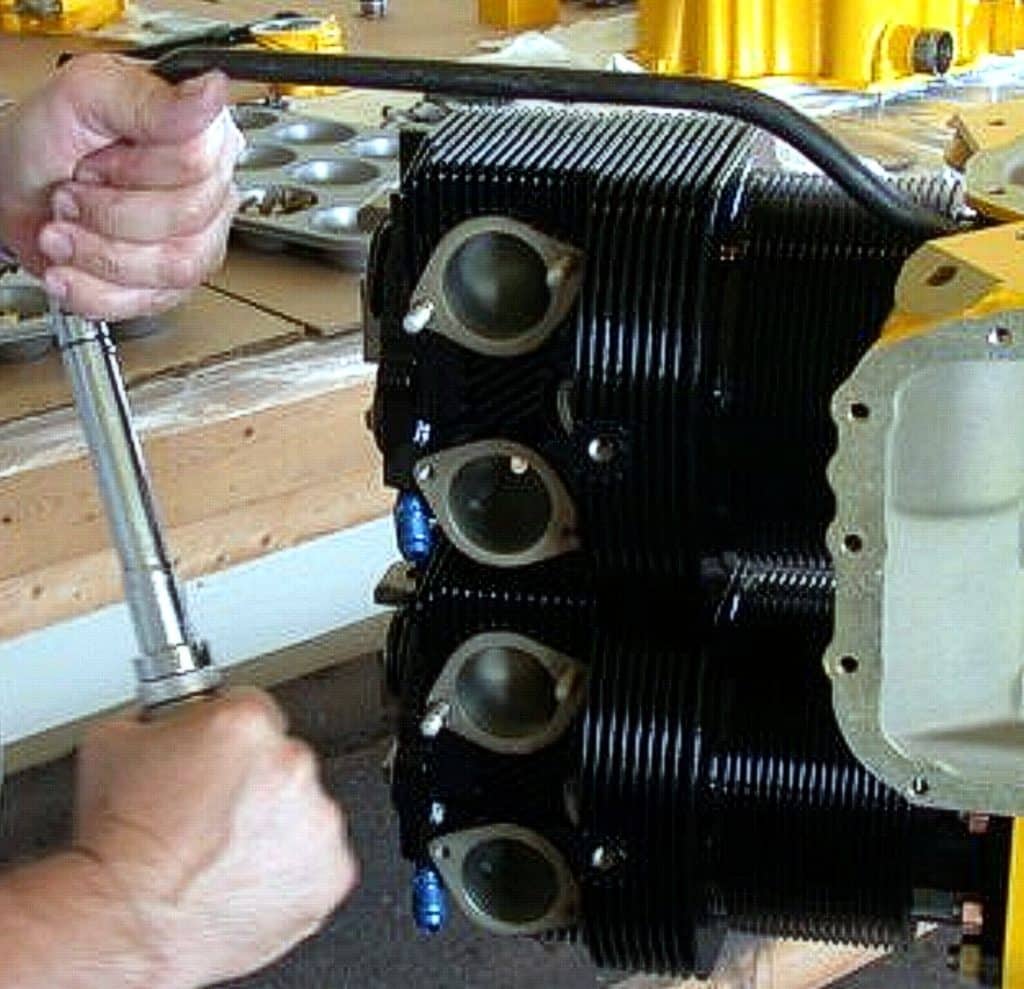
Cylinder changes are sometimes necessary. But there are a number of things that can be done to mitigate the risk.
Never change a cylinder unless it’s absolutely necessary. Try hard to avoid changing more than one cylinder at a time. When cylinder changes are unavoidable, extreme care must be exercised during cylinder installation. Clean through-bolt and hold-down stud threads meticulously, and inspect them carefully for damage. Slather all threads liberally with lubricant to minimize friction. Never reuse hold-down nuts, always install new ones. Use a recently calibrated torque wrench to tighten the nuts, following the manufacturer’s torque values and torque sequence to the letter. Take great care to achieve the final torque value with one smooth motion of the torque wrench, rather than taking multiple “bites.”
Even if all these procedures are followed, there’s no guarantee that the fastener preload will be correct or consistent. But it’ll help a lot.
You bought a plane to fly it, not stress over maintenance.
At Savvy Aviation, we believe you shouldn’t have to navigate the complexities of aircraft maintenance alone. And you definitely shouldn’t be surprised when your shop’s invoice arrives.
Savvy Aviation isn’t a maintenance shop – we empower you with the knowledge and expert consultation you need to be in control of your own maintenance events – so your shop takes directives (not gives them). Whatever your maintenance needs, Savvy has a perfect plan for you: