My hapless blunder en route to Oshkosh triggered a series of incredibly fortuitous events.
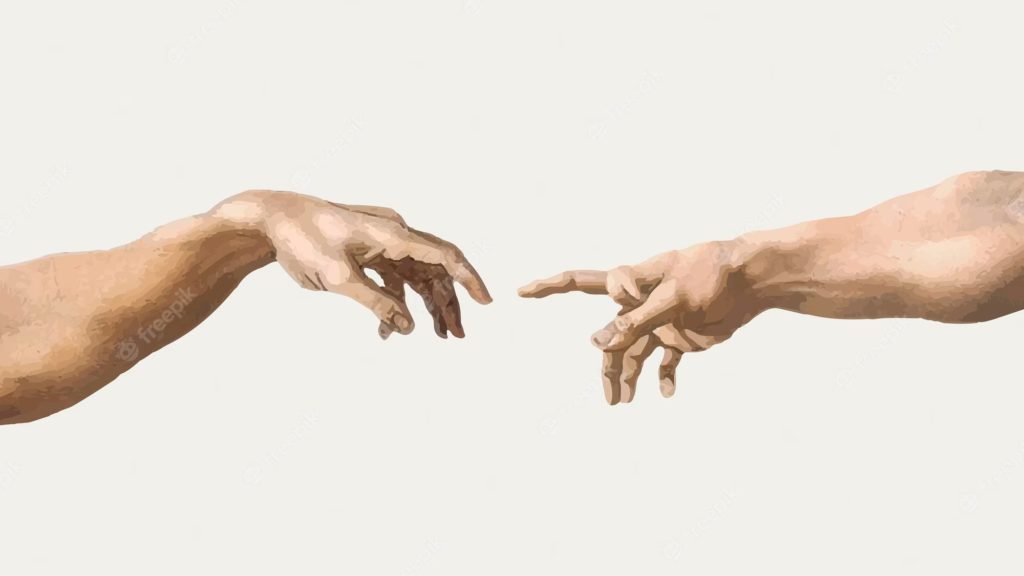
It was mid-July and my annual pilgrimage to AirVenture Oshkosh was rapidly approaching. I’d finished preparing PowerPoint for the 11 different presentations I would be making. Now I started thinking about the upcoming flight. Flying from California to Wisconsin solo can get lonely, so I called my colleague Colleen Sterling and asked if she was interested in flying with me. After conferring with her husband Dave, they both accepted my invitation.
Colleen and Dave are two of my favorite people. Both are very accomplished pilots—Dave’s a recently retired 787 captain—and both are A&P/IAs. They own five airplanes between them, all based at San Diego’s Gillespie Field (KSEE), and race three of them at Reno. Serious aviators!.
On Friday, I flew my Cessna 310 to KSEE and stayed overnight with Colleen and Dave. We planned to launch early Saturday morning and fly at least two-thirds of the way to Oshkosh, remain overnight (RON), then depart Sunday morning to arrive at Wittman Field by noon.
Northern Route
Colorado looked awful on NEXRAD, so a northerly route via Salt Lake City looked prudent. Using Foreflight, I found a promising fuel stop—Evanston, Wyoming (KEVW)—with cheap 100LL and a beautiful 7,300-foot runway. Field elevation was 7,143 feet, minimizing the descent from and climb to cruising ltitude. The best RON options were Sioux City (KSUX) or Sioux Falls (KFSD), which would put us two hours from Oshkosh. Avgas was a buck cheaper at Sious Falls, clinching the deal.
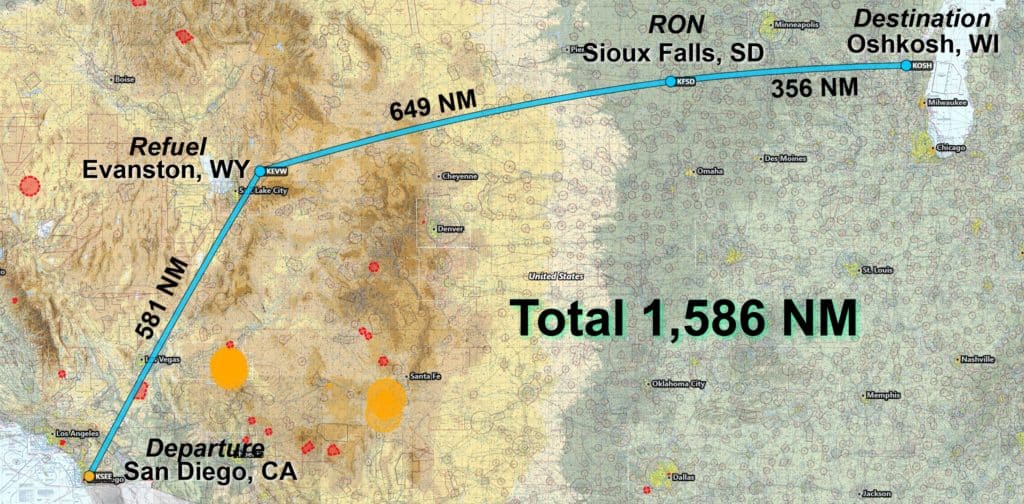
On Saturday, we rose at oh-dark-thirty, drove to KSEE, loaded our stuff into my 310, and launched for KEVW about 0730 on an IFR flight plan. The three-hour flight was beautiful, smooth and CAVU cruising at11,000 feet. I shot the GPS approach for practice, then taxied to the self-serve pump. With density altitude of 10,000 feet, I topped the mains but left the aux tanks half full.
KEVW to KFSD was a four-hour flight at 200 knots groundspeed. Upon reaching cruise altitude, Colleen passed out sandwiches, seedless grapes, and bottles of cold water. With the two-hour timezone change, our ETA was 1800 local. The flight was smooth and pleasant, although we did have to request a few minor weather deviations. As we neared Sioux Falls, all seemed right with the world.
Sioux Falls Arrival
The ATIS reported sky clear, surface winds from the southwest at 12 knots, landing and departing runway 21, with rain showers north. Both ADS-B and XM weather showed a nasty looking cell near the approach end of runway 21. We figured it would move out of the way by the time we got to the airport.
Minneapolis Center handed us off to Sioux Falls Approach, who advised us to expect the visual to runway 21. The cell was still near the approach end of the runway looking just as nasty. Colleen checked out several small non-towered fields near KFSD but none seemed like suitable RON candidates. We were getting close to the one-hour fuel reserve that is my personal minimum.
“Twin Cessna 38X, would you prefer runway 15?” the approach controller asked, as if reading our minds. “Sounds good,” Dave replied. “Twin Cessna 38X, cleared for a visual approach to runway 15, contact Sioux Falls tower on 118.3.” Dave called the tower, who cleared us to land on 15.
Our right downwind for 21 suddenly became right base for 15. I dropped the gear and ran through my pre-landing checklist. Turning final, I verbalized there would be a 10-knot crosswind component fron the right.
We crossed the threshold right on speed—90 KIAS—with the expected crab into the crosswind. I applied left rudder and right aileron to align the airplane with the runway centerline. We touched down gently on the right main, then on the left. I gently lowered the nosewheel. “Nice,” said Dave. My plan was to turn left off the runway to taxi to Maverick Air Center on the north side of the field. I lifted my heels from the floorboards and gently applied the brakes.
Then things went to hell…
Déjà Vu
The airplane started drifting to the right of runway centerline. I applied left rudder and a bit more left brake, but the airplane continued to drift to the right. Then I felt the right wing start to drop. I instantly knew what that meant, because I’d experienced the same thing about two years earlier. (See my column “Blowout!” in AOPA Pilot, September 2021 issue.)
Oh no! Oh %!@#*!
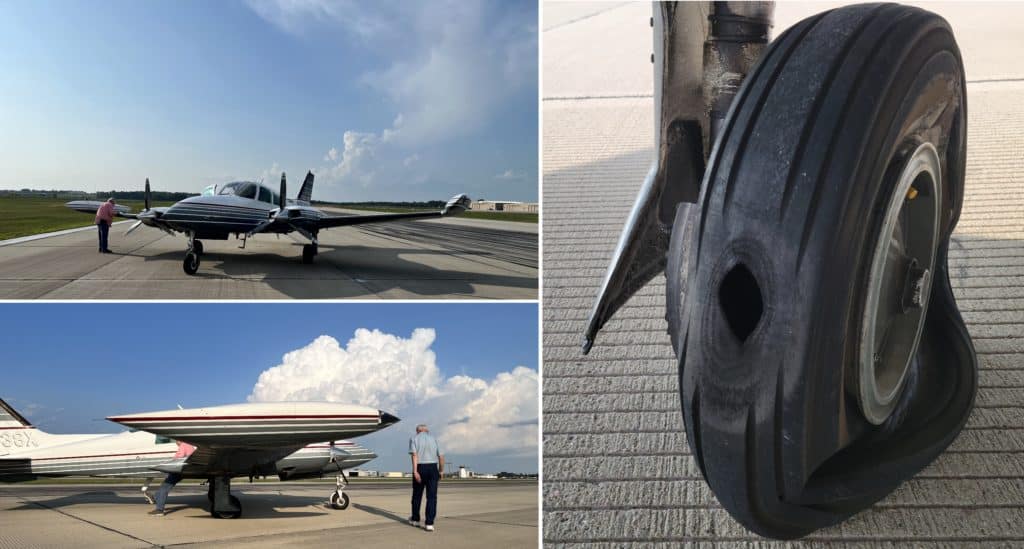
I felt like a complete idiot. It had been a perfect crosswind landing EXCEPT that I’d neglected to hold full right aileron during the rollout, and I’d neglected to retract the flaps before applying the brakes. As a result, the right wing hadn’t quite finished flying, the right wheel locked up, flat-spotting the tire and taking out the tube.
“Never stop flying the airplane until it’s in the chocks.” Sigh.
I shut down the engines. Dave advised the tower that we were immobilized on the runway with a blown tire and would require assistance. I shut down the avionics and electrics and the three of us climbed out of the airplane.
So Now What?
.Our first order of business was obviously to get the crippled airplane extracted from the runway and recovered to a safe location. Colleen checked Foreflight on her iPhone and found that while there were two FBOs on the field—Maverick and Signature—there was only one maintenance shop—Elite Aircraft Services LLC. A phone number was listed for Elite, but by now it was 6:30 PM on Saturday evening and we figured the chance anyone would answer was zilch.
Colleen dialed the number anyway. To her amazement, the phone was answered by an actual human! Colleen described our predicament, and was told someone would be there in about 30 minutes. Yay!
While waiting for help to arrive, we discussed our next steps. The 310 requires 6.50×10 tires and tubes, and I figured there was no chance that Elite would have one in stock. The earliest we could get one there would be Tuesday or Wednesday. Colleen and I absolutely had to be in Oshkosh on Sunday since our first speaking engagement was Monday morning. So, we would have to leave the plane in Sioux Falls, rent a car, and drive eight hours to Oshkosh, and then drive eight hours back to Sioux Falls the following Sunday. Ugh!.
Meantime, I was stressing over the logistics of recovering my airplane from the runway. Based on my experience two years earlier, I knew the normal wing jack for a Cessna 310 was too tall to fit under the wing when the tire was flat, and a shorter wing jack for a Bonanza or Mooney wouldn’t lift the wing high enough to raise the wheel off the ground. Then there was the matter of finding a suitable dolly that could be slipped under the wheel to allow the aircraft to be towed.
In short, I worried recovery could get difficult, and I was determined not to let my airplane get damaged in the process.
Help Arrives
A half hour after our “arrival” a white pickup approached down the runway. Two men got out and walked towards us. One was Logan Parr A&P/IA, Elite’s shop supervisor, and the other was his assistant who sported head-to-toe ink and a beard reminiscent of ZZ Top. The bed of the pickup contained a massive yellow wing jack that looked like it could lift a C-130, an equally massive blue dolly fully capable of r moving a Gulfstream or Challenger, and a large orange towbar.
This will never work, I thought.
Logan and his bearded assistant wrestled the heavy jack onto the runway and rolled it toward the right wing of my 310. “Where’s the jack point,” Logan asked. I pointed it out to him. He positioned the jack under the jack point—somehow it was not too tall to fit—chocked the left main wheel, and started pumping the jack handle. The right wing started to lift and the right main landing gear strut started to extend. I was sure we would run out of jack height before the strut fully extended and the wheel lifted off the pavement.
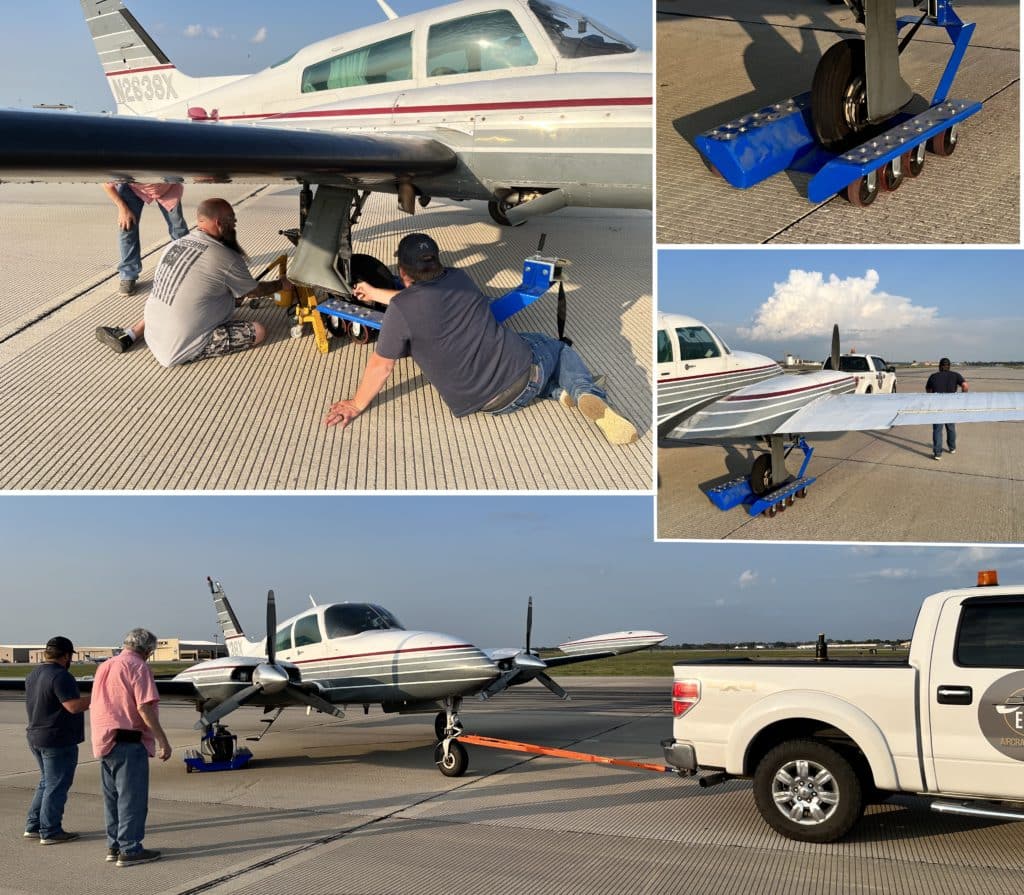
I was wrong. The wheel made it to about six inches off the pavement before the wing jack ran out of travel. This was almost enough to slide the dolly under the wheel, but not quite. Dave, ZZ and I got under the right and pushed up with all our might, which provided just enough additional lift for Logan to coax the wheel onto the dolly and secure the strut with the dolly’s winch strap. The jack was removed. ZZ repositioned the white pickup so Logan could hook the towbar to the 310’s nosewheel and the pickup’s hitch.
Logan, ZZ and I got into the pickup truck. Dave and Colleen elected to walk. After coordinating with ground control via handheld radio, the airplane was slowly towed about a mile to Elite’s hangar. By now, it was 7:30 PM with sundown rapidly approaching.
Saturday Night Fever
I tried to figure out the best way to get a 6.50×10 tire and tube shipped to Elite. Meantime, Dave hiked to the terminal to rent a car for the week. We were now resigned to the prospect of driving eight hours to Oshkosh.
Then Logan had an idea.
“I’m pretty sure the shop at Mitchell Municipal Airport maintains a bunch of twin Cessnas,” Logan told me. “They might have the correct tire and tube in stock. It’s west of here, about an hour and a quarter drive.”
“I assume there’s no way to find out until Monday morning?” I said.
“Well, I know a guy who used to work there and might be able to give me the cellphone number of the lead mechanic at Mitchell,” Logan said. “Let me try making some phone calls.” He disappeared into his office.
Dave returned with a rental car—a Hyundai crossover SUV. We transferred all our stuff from the airplane to the car. Logan reappeared.
“You might want to start driving to Mitchell,” he said. “It’ll be dark when you get there, but the outer vestibule of Wrught Brothers Aviation will be unlocked and you’ll find a 6.50×10 tire and tube inside. If you can leave it in Elite’s vestibule tonight, I’ll come in first thing in the morning and get you on your way.”
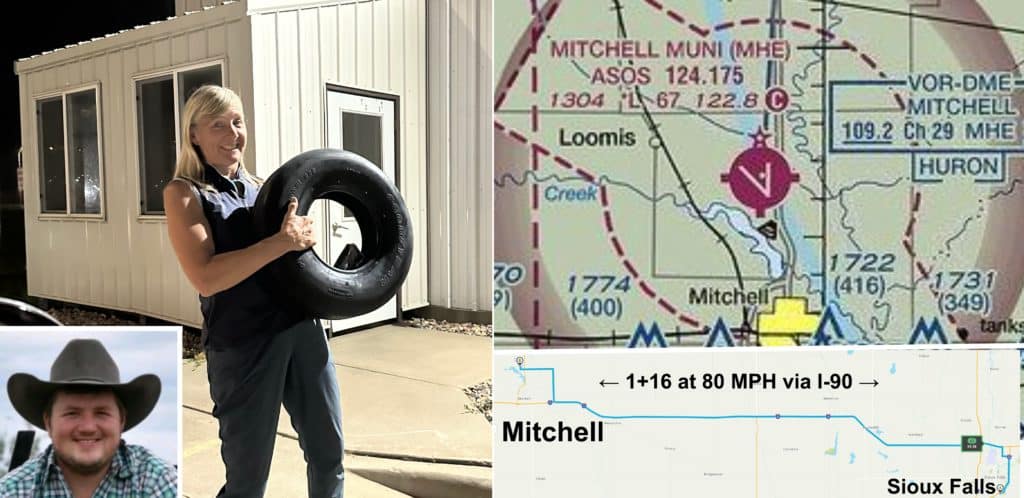
We couldn’t believe this unexpected turn of events!
Dave, Colleen and I jumped into the Hyundai and Dave drove like a bat out of hell—the speed limit on I-90 is 80 MPH—and we made it to Mitchell by 9:30 PM. Wright Brothers Aviaton was easy to find, even in the dark. Colleen disappeared into the vestibule and reappeared triumphantly holding the tire and tube. We loaded it into the car. Dave drove at the speed limit back to Elite while Colleen found overnight accommodations at a Holiday Inn Express.
The tire and tube were stashed in Elite’s vestibule by 11 PM. I sent Logan a text and said we’d meet him Sunday morning at 8:30 AM. We drove to the hotel and checked in.
End Game
By the time we arrived at Elite the next morning, Logan had already jacked the wing, removed the dolly, removed and disassembled the wheel (which fortunately was not damaged), dismounted the blown tire and tube, and mounted the new ones. This dude was FAST!.
“What tire pressure would you like?” were Logan’s first words to me.
By 9 AM, he had the wheel on the axle and eased the plane back down onto its feet. We called Maverick to send their 100LL truck and transferred our luggage from the car to the 310, then Dave returned the car. While the plane was being fueled, I filed a VFR flight plan to Oshkosh. We were wheels up by 10 AM and were parked on the Oshkosh FBO by 1 PM, more or less on our original schedule.
Amazing!
Logan Parr describes himself as “aircraft mechanic.” In truth, he’s a miracle worker with a degree of dedication that’s rare. Hopefully I’ll never again blow a tire, but if I ever do, I’ll try to make sure it’s in Sioux Falls.
You bought a plane to fly it, not stress over maintenance.
At Savvy Aviation, we believe you shouldn’t have to navigate the complexities of aircraft maintenance alone. And you definitely shouldn’t be surprised when your shop’s invoice arrives.
Savvy Aviation isn’t a maintenance shop – we empower you with the knowledge and expert consultation you need to be in control of your own maintenance events – so your shop takes directives (not gives them). Whatever your maintenance needs, Savvy has a perfect plan for you: