Does unleaded fuel really cause exhaust valve seat recession?
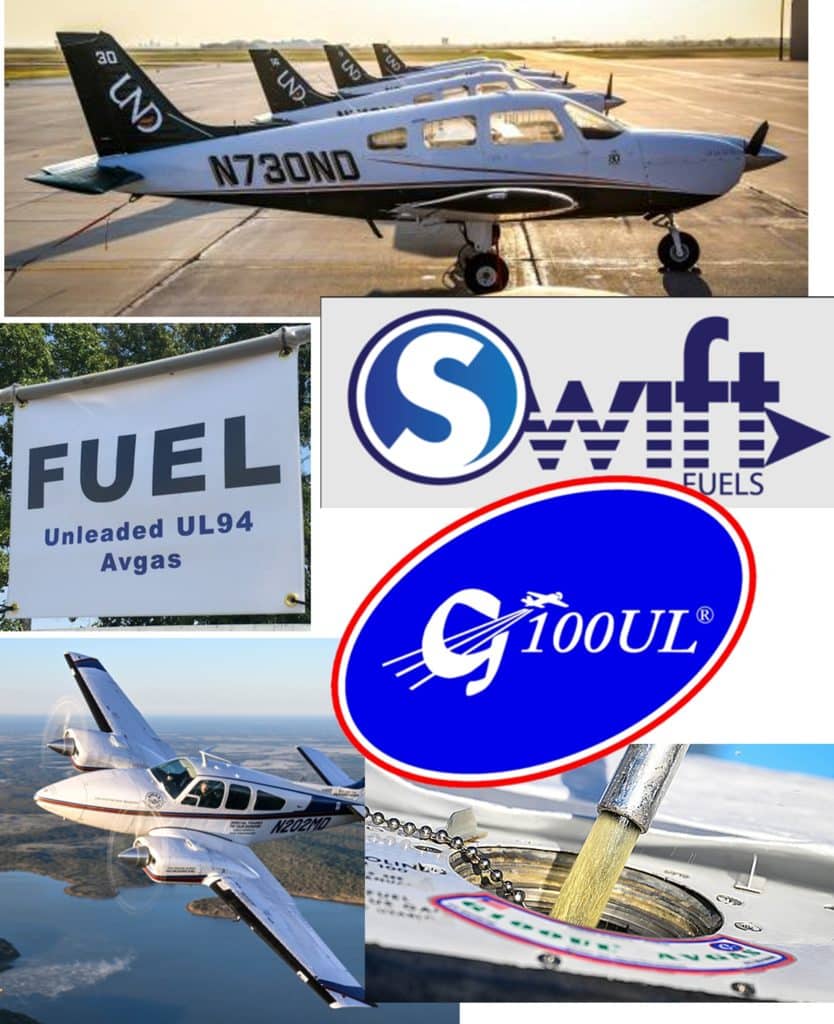
The October 27 announcement by the University of North Dakota (UND) flight school that it was terminating its year-long test of Swift UL94 unleaded avgas and returning to 100LL came as a shock and disappointment to many in the industry, me included. The school’s Director of Maintenance, Dan Kasowski, cited evidence of “significant” exhaust valve/seat recession in some of the Lycoming-powered Piper Archers in its training fleet. Kasowski was not more specific about the amount of recession or the percentage of cylinders or aircraft affected, saying only that the data is still being collected and is being forwarded to Lycoming for analysis.
The UND announcement was shocking because virtually all previous tests of FAA-approved unleaded avgas—both Swift UL94 and GAMI G100UL—seemed to indicate that the effects of operating piston aircraft engines on these fuels was all positive with no negatives. In addition, decades of experience using 91-octane premium unleaded automotive gasoline in a wide range of low-compression aircraft engines ranging from Lycoming O-320s to Continental O-470s uncovered no problems whatsoever. So the UND findings were quite unexpected, to say the least.
Is this a major setback for the long-awaited transition to unleaded avgas?
Fact or Myth?
In the automotive world, the problem of exhaust valve/seat recession reared its ugly head when the U.S. Environmental Protection Agency (EPA) mandated the availability of unleaded gasoline in 1974 in order to protect the catalytic converters first introduced in 1975 model cars. In 1996, leaded gasoline for on-road vehicles was completely phased out, at which point older cars designed to run on leaded gasoline were forced to run on unleaded fuel instead.
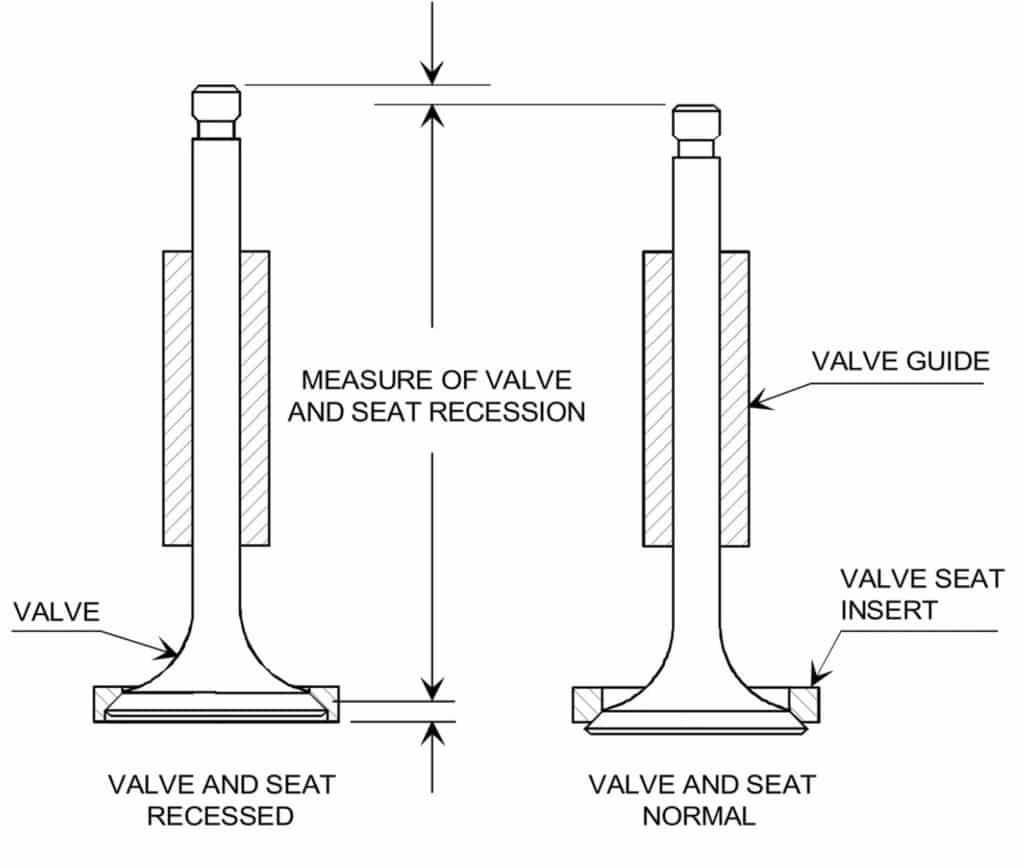
Many older cars of 1960s vintage and earlier started suffering greatly accelerated wear of exhaust valves and seats when run on unleaded gas, leading to an epidemic of burned exhaust valves. Later-model cars did not exhibit this problem. The difference was the metallurgy of the exhaust valve seats. Older cars either had their valve seats machined directly into the cylinder head casting or used valve seat inserts made of relatively soft material, while newer cars were fitted with hardened seat inserts that survived quite nicely without the presence of lead.
Now, piston GA is about to reprise the same sort of transition that the automotive world went through decades ago. Hopefully, we’ve learned a few things since then that should make our transition less painful.
What Causes Recession?
During the mogas transition from leaded to unleaded, numerous and extensive studies of exhaust valve/seat recession were undertaken, both in university laboratories and by several major oil companies. The recession phenomenon turned out to be a complex combination of factors, with various studies using different terminology and disagreeing about which factors were most important.
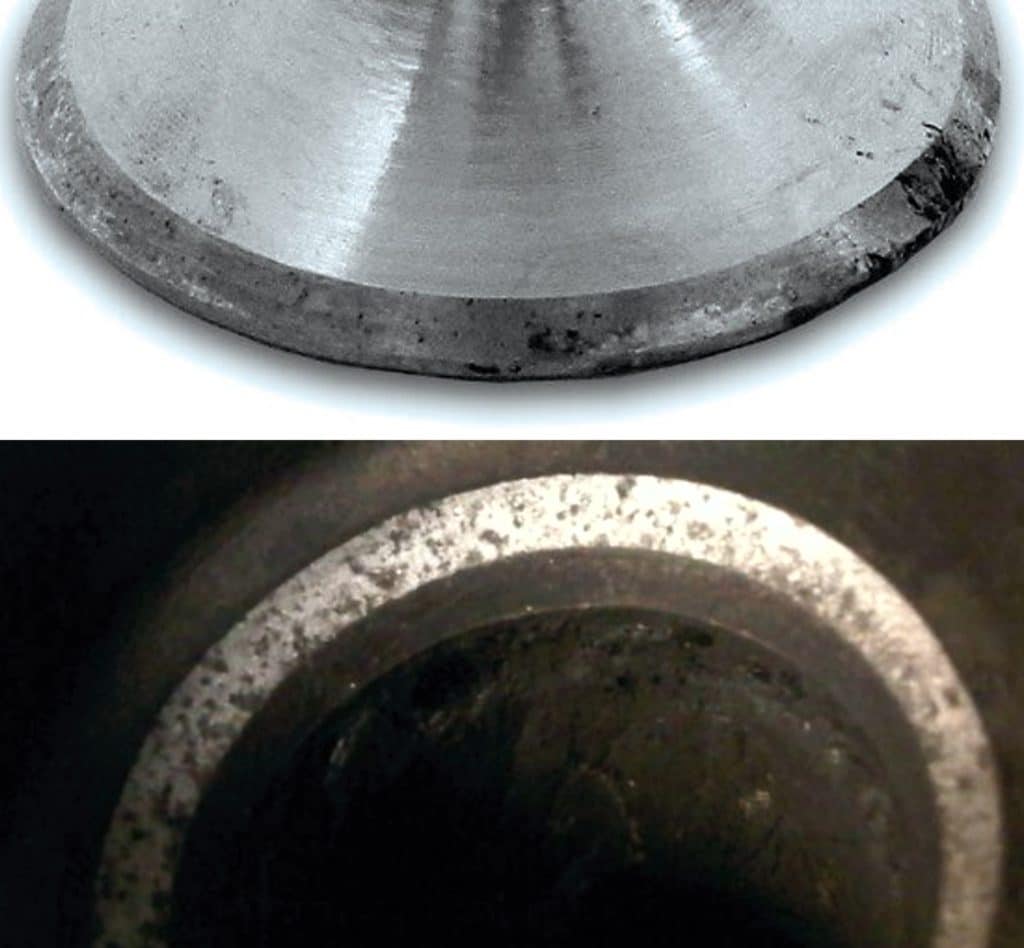
The general consensus seemed to be that exhaust valve/seat recession occurs in two phases. First, the combustion pressure of the valve face against the valve seat causes “micro-welding” that results in material transfer between the two surfaces and causes them to be come rough and abrasive. Then sliding action of the valve face relative to the valve seat—aggravated by the valve rotation in engines that employ exhaust valve rotators—causes the roughened valve face to grind down the sealing surface of the valve seat.
Micro-welding can occur both at the moment of impact as the valve makes contact with the seat as it closes and also at the moment of peak dynamic pressure during the combustion event. In direct-drive piston aircraft engines, the impact force is quite modest because of the comparatively low RPM of these engines, so the dominant factor is the peak combustion chamber pressure. Peak pressure is increased by high compression ratio, low octane fuel, and advanced ignition timing—all of which aggravate the problem of micro-welding at the valve/seat interface.
Micro-welding can be mitigated either chemically—there’s good evidence that lead oxides inhibit micro-welding—or by optimal choice of hard-yet-ductile valve seat material that is inherently less susceptible to micro-welding. That’s why both leaded fuel and hardened seats help minimize recession.
How Hard Are Your Seats?
Lycoming switched to hardened exhaust valve seats more than 30 years ago, so virtually all Lycoming cylinders now in the field have hardened seats that should do just fine on unleaded fuel. In 1989, the FAA commissioned a 150-hour side-by-side test involving a pair of Lycoming O-320 engines running on test stands, one running on 100LL and the other running on unleaded 100-octane fuel. As expected, there was no significant difference in exhaust valve or seat wear between the two engines.
Since then, Lycoming has become an enthusiastic supporter of unleaded gasoline. Lycoming Service Instruction No. 1070AB issued in April 2020 contains a table that lists virtually every Lycoming engine model and which fuels—both leaded and unleaded—they are approved to run on by Lycoming. This S.I. shows that the overwhelming majority of Lycoming models are approved for UL91 and UL94 fuels, and lots are approved for premium unleaded mogas.
In contrast, Continental has been late to the party. According to an outstanding investigative report by AVweb’s Paul Bertorelli, Continental did not switch to improved (hardened) exhaust valve seats until 2019, which means that a very large number of cylinders with non-hardened seat inserts are still in the field. As recently as 10 years ago, Continental was actively warning that the use of unleaded auto fuel could result in unacceptable exhaust valve/seat deterioration in as little as 10 hours—a little hard to believe given the excellent results we’ve seen with low-compression Continentals running mogas in the field. Continental no longer warns against the use of unleaded fuel, but does not approve it either.
To date, Continental has refused to test or approve GAMI’s G100UL despite the fact that the FAA has issued an STC approving its use in virtually all Continental and Lycoming engines. Prior to obtaining the STC, GAMI performed more than 700 hours of endurance testing involving both Continental and Lycoming engines with absolutely no evidence of exhaust valve/seat recession.
Bottom line: We really shouldn’t expect any problem running unleaded avgas in any engine with hardened exhaust valve seats—this includes all Lycoming engine and any Continental engine with cylinders manufactured in 2019 or later. There’s also plenty of anecdotal evidence that low-compression Continentals—such as the ubiquitous O-470-R/S engines in legacy Cessna 182s—do just fine on unleaded fuel despite their older-style unhardened seat inserts.
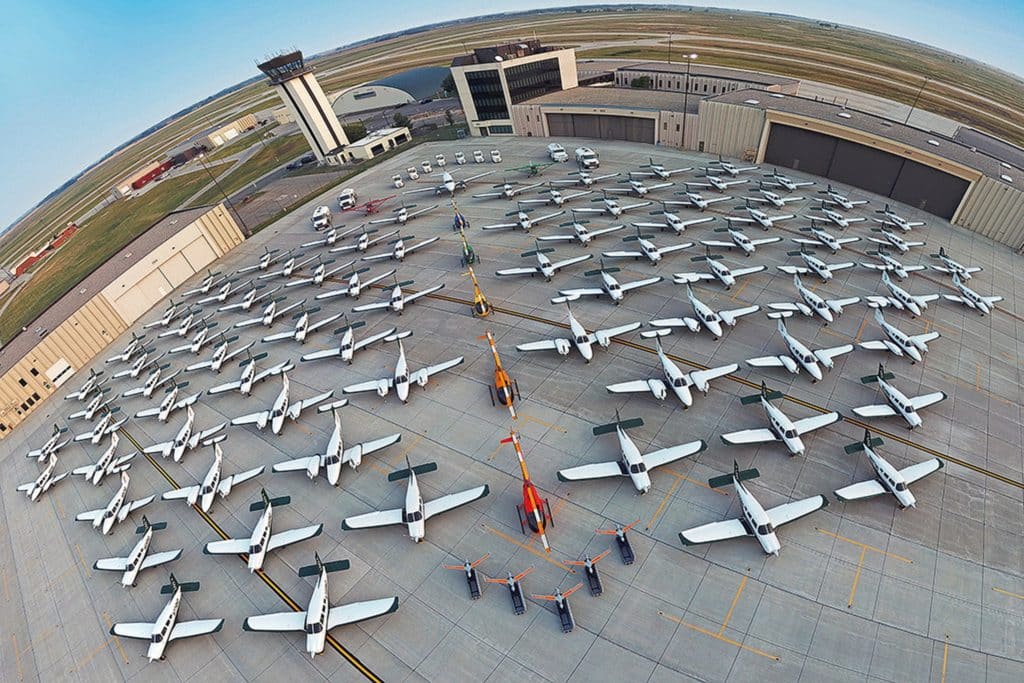
Given all this background, what are we to make of UND’s decision to terminate its use of Swift UL94 due to “significant” exhaust valve/seat recession? To say this is a real head scratcher would be a “significant” understatement. Since UND has elected not to make its data public—they’ve shared it only with Lycoming, who isn’t talking—we can only speculate at this point. Therefore, what follows is my own unvarnished speculation unsupported by any hard data. (Your unvarnished speculation may vary.)
Honestly, UNDs decision to withdraw from the UL94 trial leaves me with more questions than answers. How “significant” was the recession? Was it actually causing a substantial increase in the number of burned exhaust valves, the number of cylinders that had to be changed, and/or the amount of maintenance-related downtime in UND’s fleet of Piper Archers? Or was it simply a technical measurement of recession with no real operational significance? As I’m writing this, we don’t know.
Dry Tappet Clearance
According to UND, the concerns about exhaust valve/seat recession was derived from their measurements of “dry tappet clearance,” which is a measurement of how much “lash” (slop) there is in a cylinders valve trains when the hydraulic valve lifters (“tappets”) have been bled down so they no longer contain any oil (“dry”). This strikes me as a rather peculiar method of measuring valve/seat recession, and so bears some scrutiny.


Measuring dry tappet clearance.
Normally, the only time mechanics measure dry tappet clearance is when a cylinder is replaced. The purpose of the measurement is to make sure that the amount of mechanical lash (slop) in the valve train is within the range of what the hydraulic valve lifter can eliminate when it is pumped up with engine oil. If the value is too large, then it’s possible that the valve might not open all the way; if it’s too small, it’s possible that the valve might not close completely.
Lycoming’s spec for dry tappet clearance is wide enough to drive an eighteen-wheeler through: .028 inch minimum and .080 inch maximum. Anything within this very broad range is acceptable. If a mechanic replaces a cylinder and the dry tappet clearance value is outside this range (which is rare), then an approved undersize or oversize pushrod needs to be installed to bring the measurement within tolerance.
UND’s decision to monitor dry tappet clearance as a measure of valve/seat recession strikes me as problematic in two ways. First, it measures total valve train lash (slop) which is the sum of numerous elements of which valve/seat recession is only one component. A decrease in dry tappet clearance might indicate recession, but it might also be caused by other things, notably failure to ensure that the tappet body is totally devoid of liquid. As one experienced engine builder told me, “there’s really no such thing as a dry tappet.”
Second, I’m a bit troubled by UNDs unorthodox decision to monitor dry tappet clearance on an ongoing basis as suggesting that they were actively “looking for trouble” in this area, despite a mountain of testing by the FAA, Lycoming and others suggesting that it wouldn’t be a problem. That raises the obvious concern about “observer bias”—the natural human tendency to see what one expects to see. I’m not saying that this occurred, only that it might’ve.
But What If It’s Real?
Despite all these questions, it’s entirely possible that UND has uncovered a “significant” operational issue, seemingly against all odds, that is actually resulting in more burned valves, more cylinder replacements, and more Archer downtime running on Swift UL94 than what occurred with 100LL. If that turns out to be the case, what could the explanation be? Would this be a major setback for GA’s transition to unleaded fuel, or just a blip?
Interestingly, UND’s Piper Archers are powered by Lycoming 180 hp O-360-A4M engines. This engine is among Lycoming’s highest-compression engines (8.5-to-1) with a rather aggressive ignition timing of 25° BTDC. A bit of research revealed that it was originally certified for grade 91/96 octane minimum. (Grades 80/87 and 91/96 avgas have not been available for many years.) The current revision of the Type Certificate Data Sheet (TCDS) lists a minimum fuel octane rating of 100. The high compression ratio and aggressive ignition timing cause this engine to have significantly greater peak combustion pressure—that’s what presses the valve into the seat and can cause micro-welding—than the lower-compression engines (typically 7.0-to-1) that have been running successfully on unleaded auto fuel for decades.
Reducing the fuel octane rating from 100 to 94 as allowed by Lycoming Service Instruction 1070AB results in even higher peak combustion pressure—since lower-octane fuel burns faster—and so might aggravate the micro-welding problem even more. Since both eliminating lead and reducing octane can aggravate the micro-welding problem, doing both at the same time might not be the best idea. I can’t help but wonder whether anyone considered the possibility of retarding the ignition timing by a degree or two to compensate for the lower-octane fuel? Seems to me that might have been prudent.
Perhaps by the time you read this we’ll have some answers. Perhaps not.
One Airplane, Two Fuels
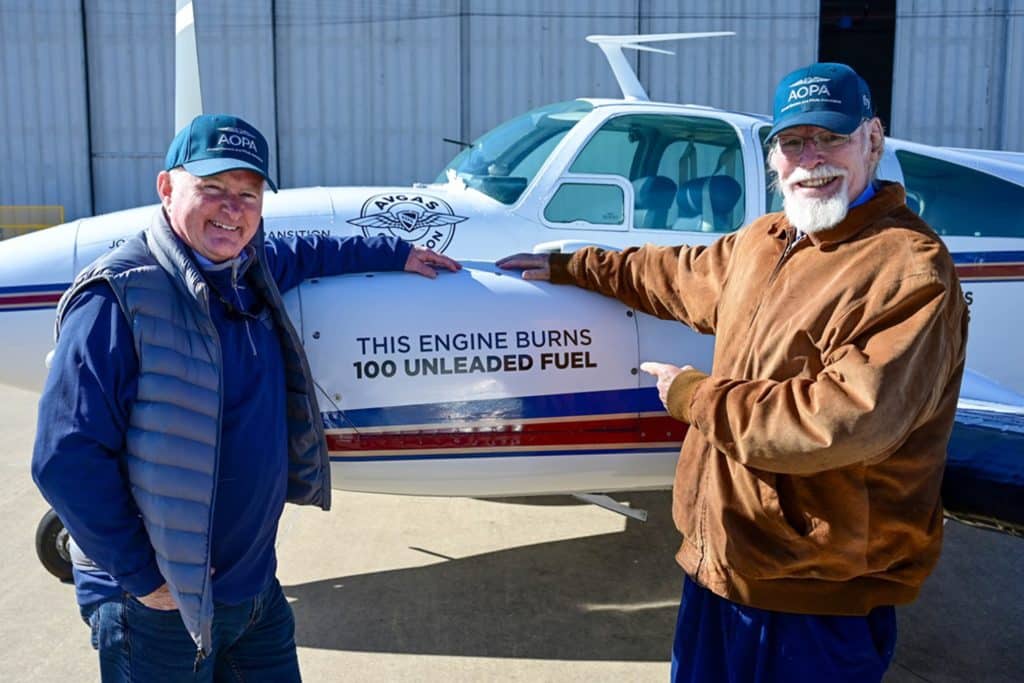
In the meantime, AOPA has commenced what I expect to be a very interesting and enlightening side-by-side test of leaded vs. unleaded avgas. It involves a recently refitted Beechcraft 55 Baron with a pair of freshly overhauled Continental IO-520 engines and a fancy glass panel that is now operating with GAMI G100UL high-octane unleaded avgas on the left side and traditional 100LL avgas on the right side. The plan is to put hundreds of hours on this airplane during the next couple of years. The two-fuels Baron is presently based in Ada, Oklahoma, but will be redomiciled to Frederick, Maryland in a few months once the logistics of transporting a supply of G100UL to Frederick can be completed.
AOPA asked my company Savvy Aviation to manage the maintenance and data analysis for this project. We will be doing intensive comparative analysis of digital engine monitor data, borescope inspections, and laboratory oil analysis for both engines. In addition, we will be carefully measuring exhaust valve/seat recession—using a far more precise methodology than dry tappet clearance—which should allow us to track recession with thousandth-of-an-inch accuracy. Since the two fuels have the same octane rating, this should be a very pure and well-controlled test of effects of getting the lead out.
You bought a plane to fly it, not stress over maintenance.
At Savvy Aviation, we believe you shouldn’t have to navigate the complexities of aircraft maintenance alone. And you definitely shouldn’t be surprised when your shop’s invoice arrives.
Savvy Aviation isn’t a maintenance shop – we empower you with the knowledge and expert consultation you need to be in control of your own maintenance events – so your shop takes directives (not gives them). Whatever your maintenance needs, Savvy has a perfect plan for you: