How do you decide when it’s time to overhaul your engine? If not at TBO, then when?
Regular readers of this column know that I’m not a big fan of the idea of overhauling engines at TBO. I consider engine TBO to be a thoroughly discredited concept that has cost aircraft owners hundreds of millions of dollars by causing perfectly healthy engines to be euthanized arbitrarily. The notion of overhauling aircraft engines at a particular number of hours was abandoned many decades ago by the airlines and the military. Piston GA is the last segment of aviation that still subscribes to this ridiculous idea.
The TSIO-520-BB engines on my Cessna T310R have a published TBO of 1,400 hours. Both of my engines are now at 2,800 hours—200% of TBO—and still doing just fine, thank you very much. Many of my managed-maintenance clients are well past TBO. One whose engine has a 2,000-hour TBO is now at 3,200 hours and doing just great.
There are several reasons that TBO is such a flawed concept. One is that engine life has very little to do with engine hours in service. Hours is not what limits the life of our engines. The biggest life-limiting factor is exposure to corrosive environments during periods of disuse. The next biggest is operator abuse, particularly cold starts and improper powerplant management. None of these factors are reflected in the manufacturer’s published TBO.
Does it make any sense at all that the engine on an aircraft tied down outdoors in Tampa would have the same TBO as one hangared in Tucson? Or that one that flies 400 hours a year would have the same TBO as one that flies 40 hours a year? Or that one that flies mostly long-distance cross-country missions would have the same TBO as one used primarily for flight training? Of course not! The whole notion of a one-size-fits-all TBO is inherently nonsensical.
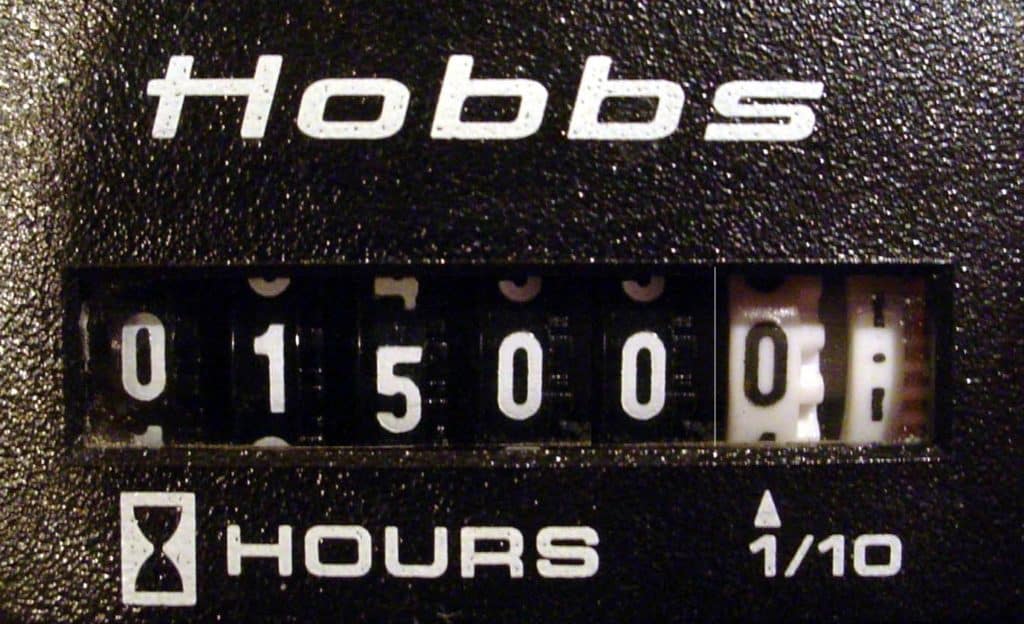
So why are so many owners still euthanizing healthy engines just because the hour meter rolled over to some fixed value?
On-condition maintenance
The smart way to deal with engine maintenance—including deciding when to overhaul—is to do it “on-condition” rather than on a fixed timetable. This means is that we use all available condition-monitoring tools to monitor the engine’s health, and to let the engine itself tell us when maintenance is required. This is how the airlines and military have been doing it for decades.
For our piston aircraft engines, we have a marvelous multiplicity of condition-monitoring tools at our disposal. They include:
- Oil filter visual inspection
- Oil filter scanning electron microscopy
- Spectrographic oil analysis
- Digital engine monitor data analysis
- Borescope inspection
- Differential compression test
- Visual crankcase inspection
- Visual cylinder head inspection
- Oil consumption trend analysis
- Oil pressure trend analysis
If we use all these tools on an appropriately frequent basis and understand how to interpret the results, we can be confident that we know whether the engine is healthy or not—and if not, what kind of maintenance action is necessary to restore it to health.
Use those tools!
The moment you abandon the TBO concept and decide to make your maintenance decisions on-condition, you take on an obligation to use these tools—all of them—and pay close attention to what they’re telling you. Unfortunately, many owners and mechanics don’t understand how to use these tools appropriately or to interpret the results properly.
Just today, for example, I received an email from the owner of a 2002 Beechcraft A36 Bonanza which said in part:
“My engine has 1,700 hours [it’s at TBO] and is running fine. It uses only 2 to 3 quarts of oil per 50-hour oil-change interval. I send in an oil sample to the lab at each oil change, and so far there have been no issues. I don’t regularly cut open the filter. My plan is to install a factory rebuilt engine when the time comes…”
Yikes! This owner is not cutting open his oil filters on a regular basis. How the heck is he going to know “when the time comes”? Oil filter inspection is by far the single most important tool we use in deciding when to overhaul, and he’s not doing it.

In a subsequent email exchange, the owner told me that his mechanic felt that there was no need to cut open the oil filters because the engine is on an oil analysis program. Boy oh boy, what terrible advice! Oil analysis is a complement to oil filter inspection, not a substitute. The purpose of oil analysis is to detect microscopic wear metal particles that are too small to see and too small to be caught in the filter.
If the engine develops a serious problem that throws off large quantities of metal chips, flakes, whiskers or fines, chances are that metal will be caught in the oil filter and never make it into the oil sample bottle. Rapid wear events such as cam lobes, lifters or starter adapters coming apart almost never show up in oil analysis because the metal they throw off is too large to pass through the oil filter. If we don’t do regular oil filter inspections, we’ll never detect problems like this.
Don’t panic!
Time after time, I see aircraft owners and their mechanics overreact when elevated wear metals appear in an oil analysis report or visible metal shows up in the oil filter or a cylinder exhibits a drop in compression. You need to resist this urge. Don’t panic!
A single bad oil analysis report is pretty meaningless. For our managed-maintenance clients (all of whom are on oil analysis), we generally do not take action until we’ve seen three consecutive reports so we can determine whether the initial bad report was a transient anomaly or the start of a worsening trend. We will typically put the engine on a short oil-change interval (e.g., 25 hours) so we can gather data more rapidly. More often than not, the elevated wear metal values wind up self-resolving over the next 50 to 100 hours and no follow-up action is necessary.
Even if the oil analysis results keep getting worse, we never suggest grounding the airplane or taking the engine apart based solely on oil analysis results alone. Keep in mind that what oil analysis is reporting on is microscopic wear metal particles that are too small to see and too small to be caught in the oil filter. Metal particles that small certainly do not represent any sort of safety-of-flight hazard. No matter how ugly the oil report looks, we’re not going to do anything drastic.
A series of deteriorating oil analysis reports simply tells us that we need to start looking more aggressively using other condition-monitoring tools at our disposal. For example, we might perform a borescope inspection of all the cylinders to see if we can spot anything wrong (scored barrel, burned exhaust valve, etc.) Or we might send the oil filter media out to a lab for scanning electron microscope evaluation, which will tell us the shape and alloy of the metal, and often provide a good indication of where it’s coming from. Or we might dump the engine monitor data and analyze it to see if we can spot any combustion anomalies, oil pressure fluctuations, etc.
Similarly, if we cut open an oil filter and spot a significant amount of metal, we won’t ground the aircraft unless the amount of metal found is huge (e.g., a quarter-teaspoon). Most of the time, we will put the engine on a short oil-change interval, and we’ll send the filter media out for scanning electron microscopy. If the amount of metal in the filter continues to increase, we might decide to pull some lifters, the prop governor, or perhaps the starter adapter in hopes of finding out exactly where the metal is coming from.
Low compression readings always trigger a careful borescope inspection. If we can’t see anything unusual under the borescope to explain the low compression, we’ll have the owner fly the airplane for awhile and then re-check the compression at a later time. (Continental service bulletin SB03-3 provides exactly this guidance.)
Time to overhaul?
It takes something pretty serious before we conclude it’s time to send the engine off to an engine shop for teardown—or to replace it with an exchange engine. Here’s a list of the sort of findings that would prompt us to recommend that “the time has come”:
- An unacceptably large quantity of visible ferrous metal in the oil filter; unless the quantity is very large, we’ll often wait until we’ve seen metal in the filter for several shortened oil-change intervals.
- A crankcase crack that exceeds acceptable limits, particularly if it’s leaking oil.
- A serious oil leak (e.g., at the crankcase parting seam) that cannot be corrected without splitting the case.
- An obviously unairworthy condition observed via direct visual inspection (e.g., a bad cam lobe observed during cylinder or lifter removal).
- A prop strike, serious overspeed, or other similar event that clearly requires a teardown inspection in accordance with engine manufacturer’s guidance.
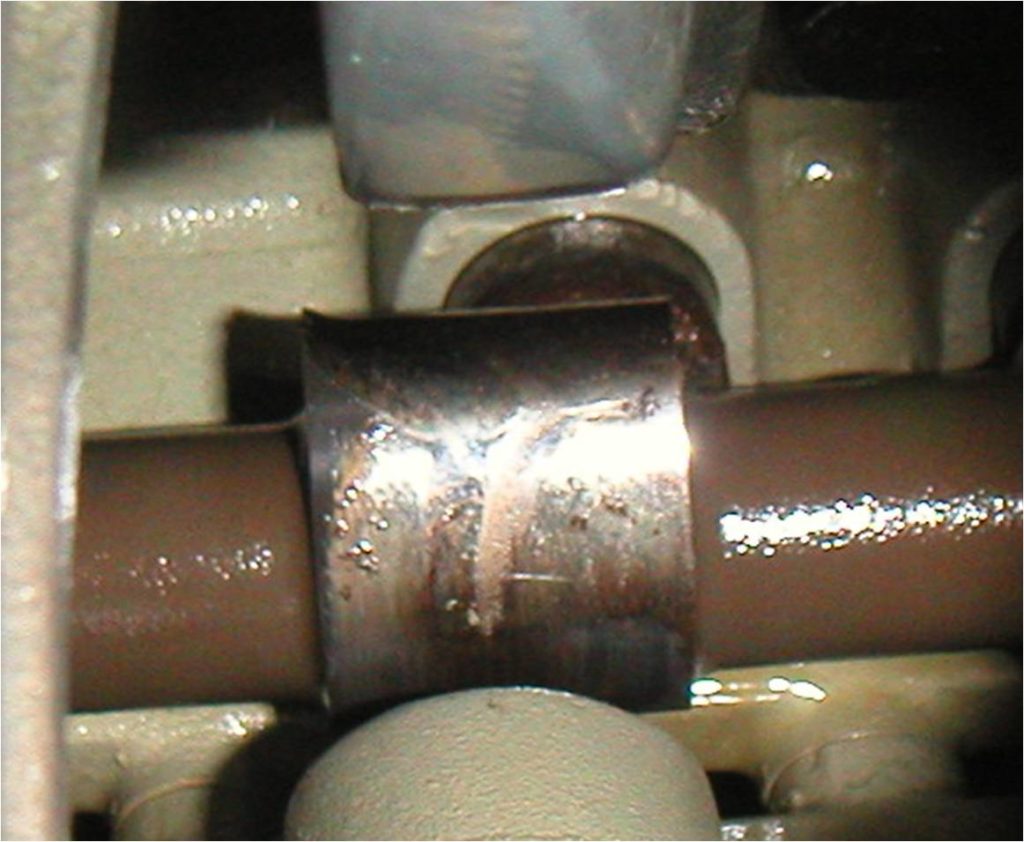
To summarize: Ignore TBO, maintain your engine on-condition, make sure you use all the available condition-monitoring tools, make sure you know how to interpret the results (or consult with someone who does), and don’t overreact to a single bad oil report or a little metal in the filter.
Using this reliability-centered approach to engine maintenance, we’ve helped hundreds of clients obtain the maximum useful life from their engines, saving them a great deal of money, downtime and hassle. And we haven’t had one fall out of the sky yet.
You bought a plane to fly it, not stress over maintenance.
At Savvy Aviation, we believe you shouldn’t have to navigate the complexities of aircraft maintenance alone. And you definitely shouldn’t be surprised when your shop’s invoice arrives.
Savvy Aviation isn’t a maintenance shop – we empower you with the knowledge and expert consultation you need to be in control of your own maintenance events – so your shop takes directives (not gives them). Whatever your maintenance needs, Savvy has a perfect plan for you: