I’ll admit that coming up with a clever title is one of the rewards of writing a monthly article. But I didn’t spend a second trying to find a clever or arcane title for this one. I wanted it to be clear what this month’s topic is. The puzzle is which engine data parameters should we look at, and what patterns should we expect to see?
Before we formally opened the doors for SavvyAnalysis in 2012, we knew that engine data could reveal clogged injectors, misfiring spark plugs, failing sensors, and other common maintenance issues. As time marched on, we began to recognize the oscillating patterns of failing valves, which evolved into FEVA, then FEVA 2.0 and now FEVA 2.1. We now have a pretty good decision tree for spotting a sticking valve, which I wrote about in December and January. In the 79 Puzzlers preceding this one, we’ve looked at failed mags, detonation, vapor lock, runaway props, induction leaks, and some catastrophic failures. In some of those cases, we thought it through and looked for a rise in this or a drop in that. So let’s apply that process to cam lobes.
Every time your cam rotates those lobes wear just a little more. They’re built to take a lot of spins, but sadly, pitting, spalling, corrosion and lack of lubrication from infrequent flying are more likely to cause trouble for your cam than an excess of spins. Savvy doesn’t officially endorse products, but we recommend CamGuard whether you use Shell or Phillips oil in your engine. If you want to know more about cam failure and what to do about it, Mike’s 2012 EAA Sport Aviation article about cams and cam wear is here. Mike’s 2015 EAA webinar about cam distress is here. Our mission with this month’s Puzzler is to determine if engine data can help you recognize a worn cam. Let’s think it through.
Presumably a brand new cam in a new or freshly overhauled engine would push the lifters and rods to the proper spec, so intake and exhaust valves are opening as far as they can go. At mid-time, the cam lobes would have worn so that the valves aren’t quite opening as far as they can go, but they’re still within spec. As the lobes continue to wear, the valves open a fraction less each time.
How would a worn cam effect performance? As the engine develops a little less power, takeoff rolls would be a little longer. Climb performance would be a little more sluggish. These would be hard to detect because the increments of degradation are so small.
Would oil analysis help? Sure. A new Continental cam has a surface coated with a 0.15″ manganese phosphate layer to resist corrosion and lower friction. When that wears, you can expect to see higher iron levels in the oil. You might also see an increase in ferrous material in the oil filter – typically whiskers and flakes.
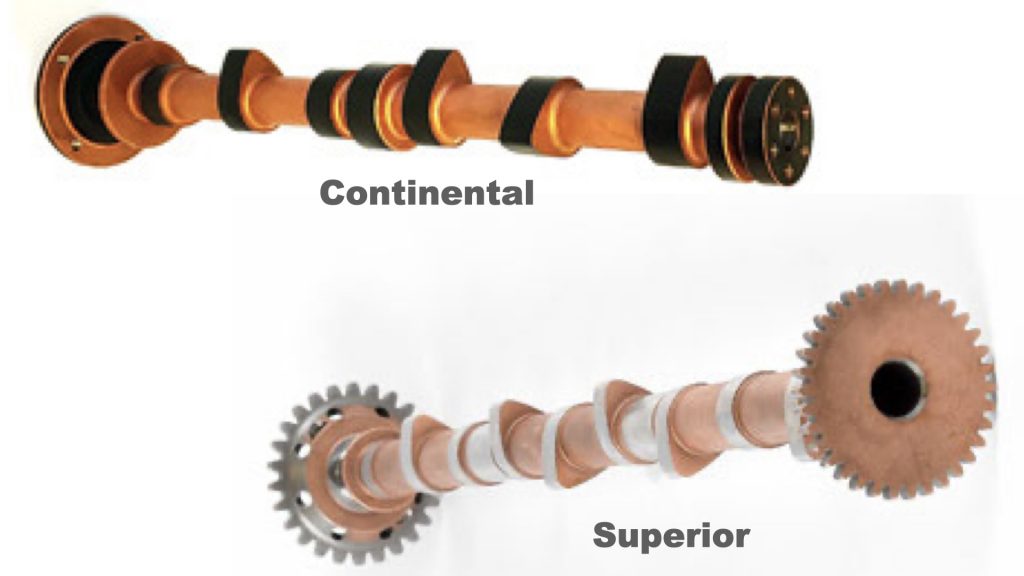
When it comes to the data, the fact that opposing cylinders share cam lobes for the intake valves helps the diagnosis a little. If we see something suspicious in 4, for instance, we’d look at its lobe partner – 3. In fact, that’s one of the steps in determining whether the problem is isolated to one cylinder, or is shared by the pair. Here’s data from a restart 182 with a Lycoming IO-540 and data from a JPI 730 with a 6 sec sample rate. For the first two samples we’ll look at EGT and CHT only.
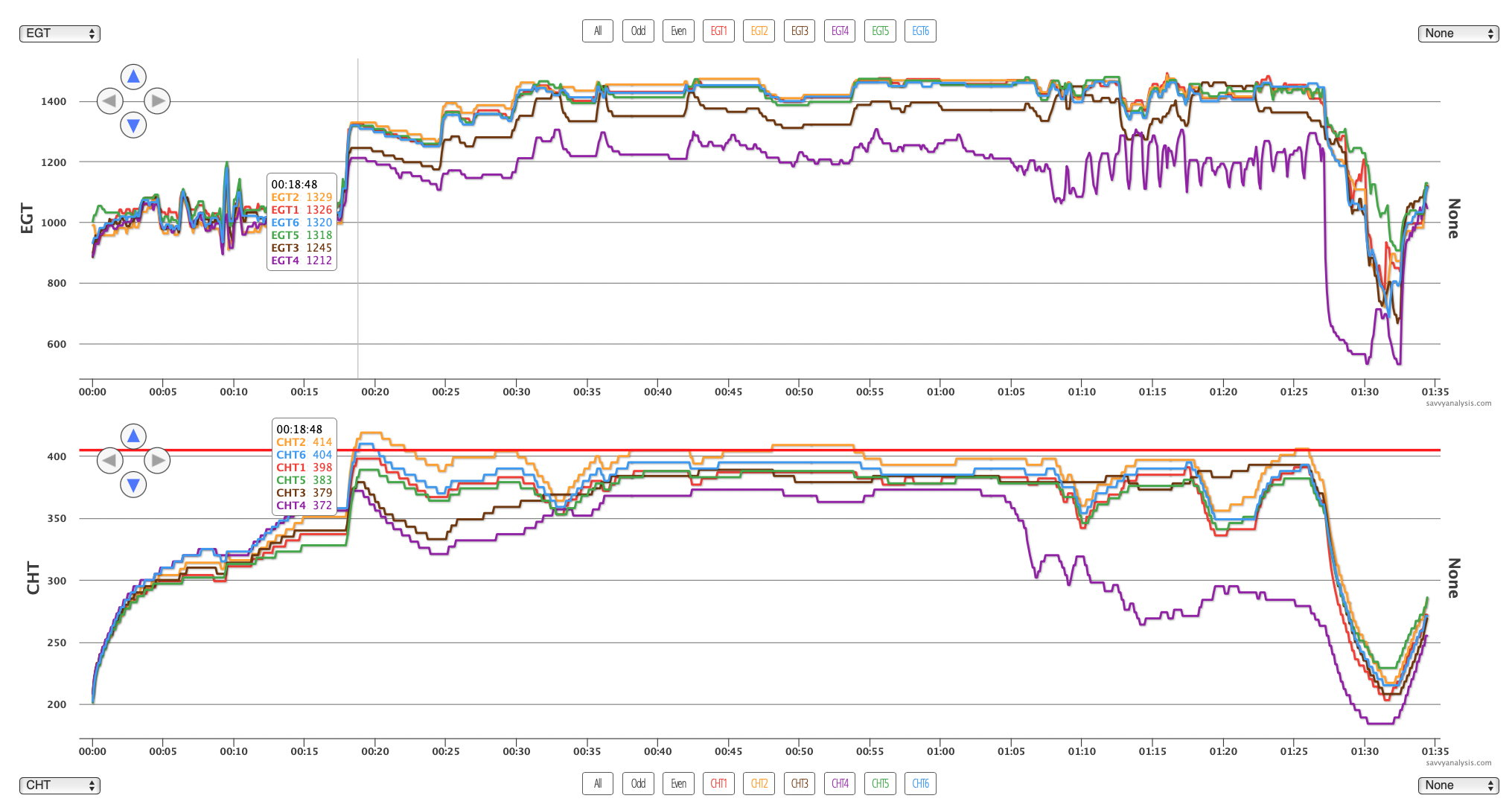
This is a sluggish takeoff from cyls 3 and 4. They had been trending lower in recent flights, and about an hour into the flight cyl 4 stops making power. Engine teardown revealed the cam was at fault. I don’t have more details than that.
Here’s data from a Mooney M20E with a Lycoming IO-360 and data from a JPI 700 with a 6 sec sample rate.
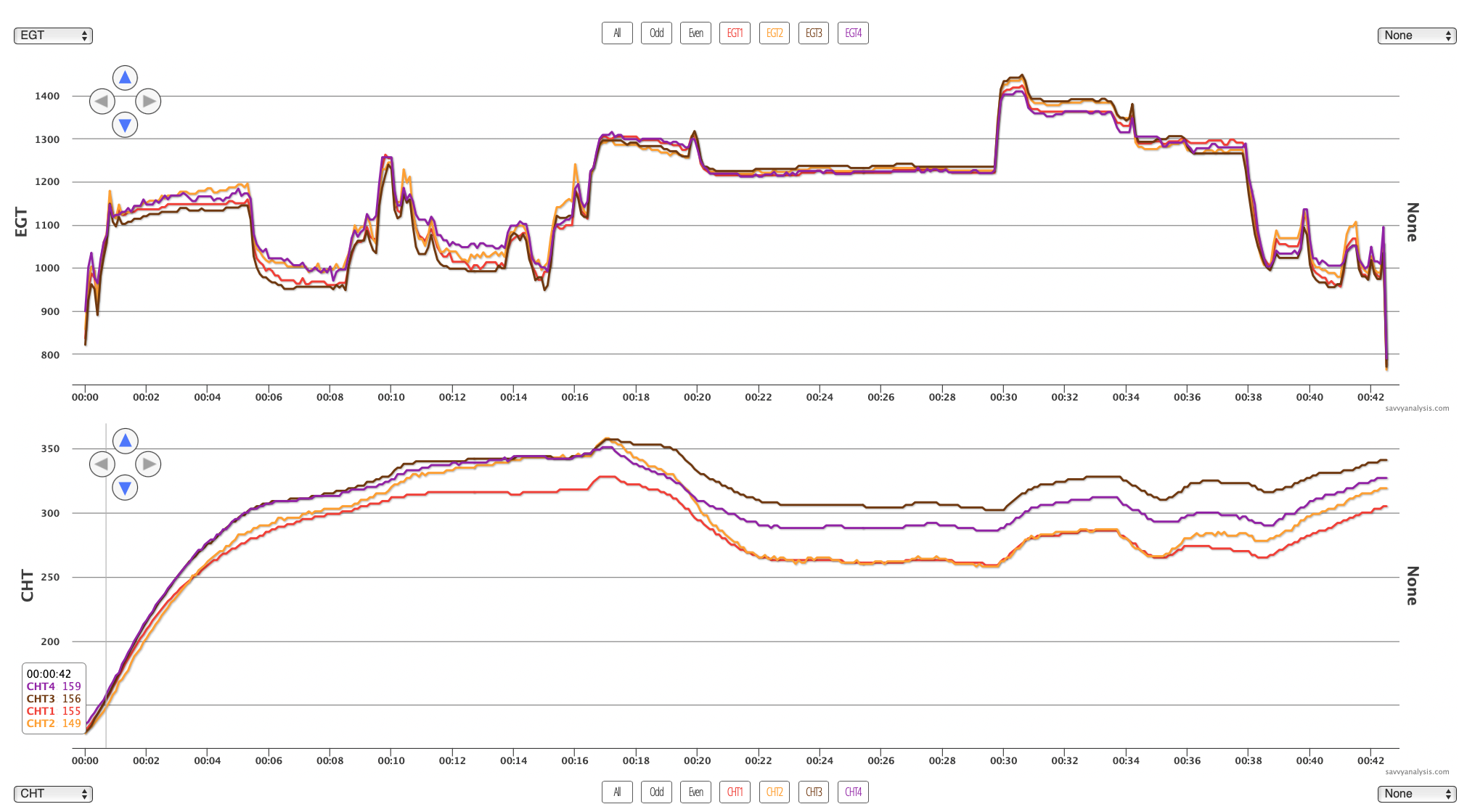
The pilot reported sluggish performance as the plane went in for annual. The most recent oil analysis had shown an increase in iron and nickel. Data showed that EGTs are normal, but CHTs indicate that’s where to begin the detective work. The shop measured the valve clearances —
#1 – .315 – .337
#2 – .311 – .337
#3 – .447 – .450
#4 – .463 – .474
which showed that 1 and 2 weren’t opening as far as 3 and 4. The decision was made to remove cyl 1 and they found a worn cam.
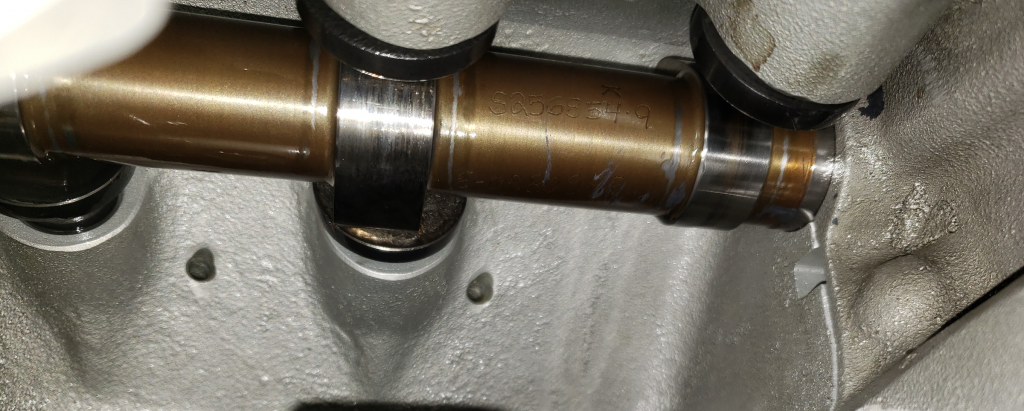
Here’s data from another restart 182 with a Lycoming IO-540 and data from a Garmin G1000 with a 1 sec sample rate. Nothing special about cursor placement – just getting it out-of-the-way.
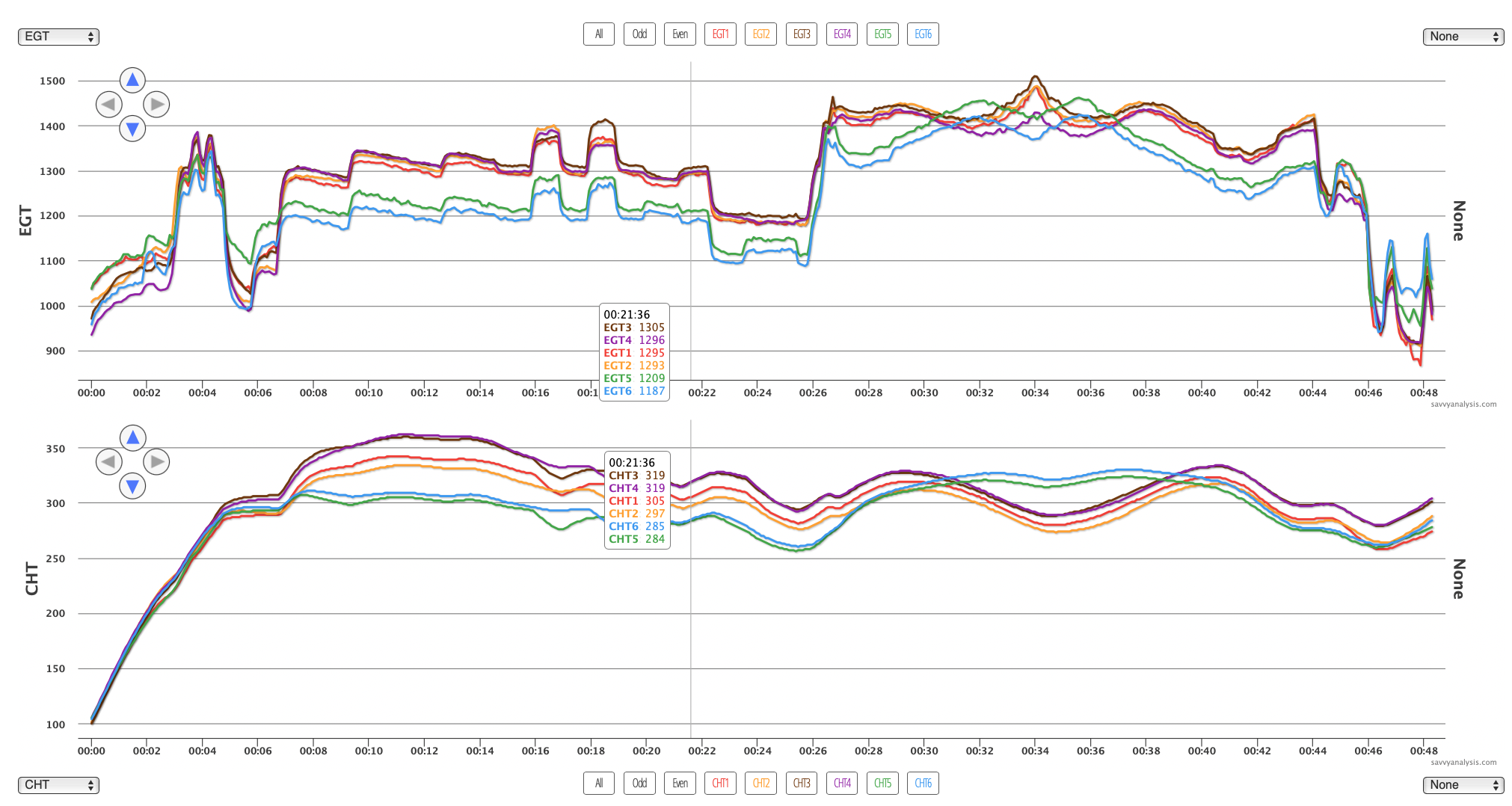
On this one it probably helps to look at FF, too.
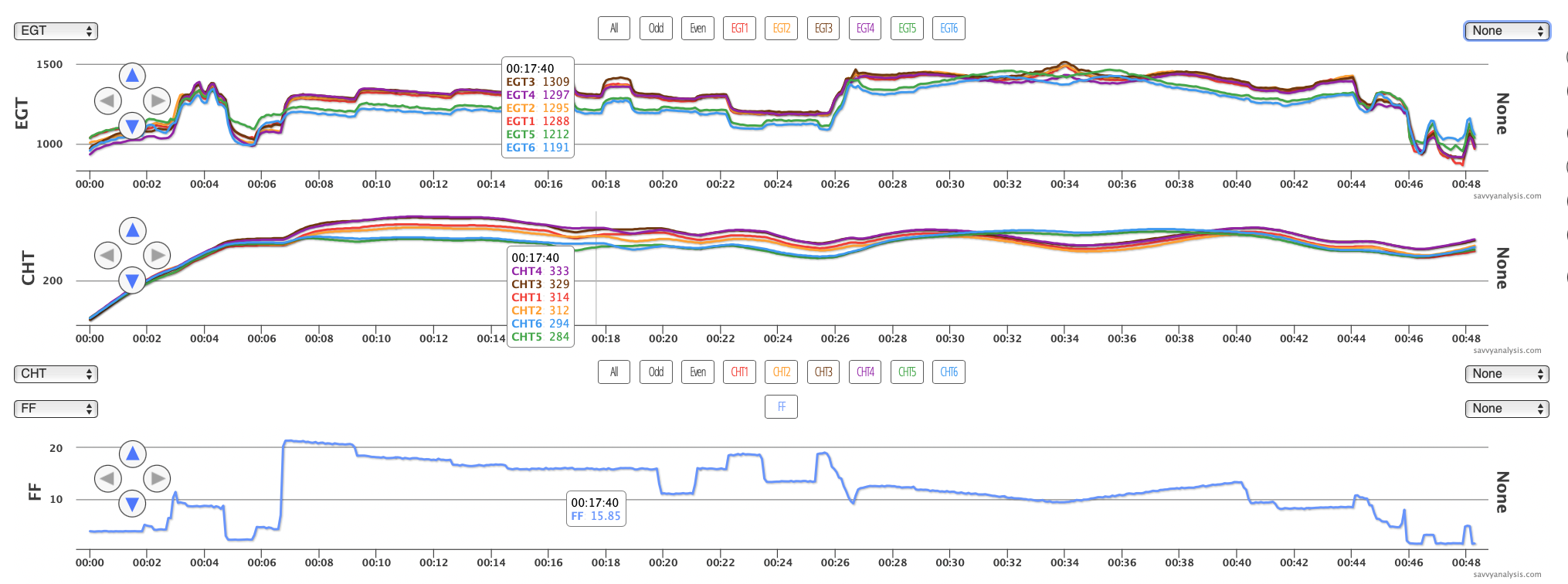
Takeoff is around the 7 min mark and a long slow mixture sweep begins at the 26 min mark. In the climb, 5 and 6 look like they’re putting out low power. As the mixture sweep begins, EGTs 5 and 6 peak well ahead of the others. And the high CHTs at the 32 min mark suggest that power is available – at the correct mixture. What would cause 5 and 6 to run rich? Or are the other 4 cyls running lean? We’d say no to that because max EGTs and CHTs don’t suggest overall lean-ness in 1-4, and the odds of those four injectors clogging are lottery-like. Could 1-4 have an induction leak? Again, long odds – plus they’re not lean overall, as indicated in the mixture sweep.
Investigation uncovered worn cam lobes for cyls 5 and 6 keeping the valves from opening fully and causing those two to run extra rich.
We’re a long way from announcing a FEVA-like scan for worn cam lobes. And, like FEVA, this may evolve into a machine-learning project where the computer determines which parameters are statistically significant. Meanwhile, the humans will be on the lookout for patterns like these.